Kodiak Robotics Introduces 5th Generation Autonomous Truck; Increases Number of Sensors for Added Redundancy and Removes Center Sensor Pod for Faster Build Time and Maintenance
By relocating the sensors to the SensorPods located on the side-mounted mirrors, Kodiak has simplified the build process and fundamentally improved the maintainability of the system. By having sensors located in an easy-to-reach location on the mirrors, customers avoid having to access the roof to maintain sensors.
Kodiak Robotics, Inc., a leading self-driving trucking company, today introduced its fifth-generation autonomous truck hardware platform which increases sensor redundancy and GPU processing power, and more. Notably, Kodiak removed the roof-mounted "center pod" sensor suite and relocated the front-facing Luminar Iris LiDAR and wide field-of-view camera to each of Kodiak's proprietary mirror-mounted SensorPodsTM. By integrating sensors into the SensorPods, and eschewing the "unibrow" sensor suite common in the autonomous trucking industry, Kodiak has unlocked faster upfitting for customers, greater maintainability and serviceability, and better perception capability. The move also doubles the Kodiak Driver's, the company's self-driving technology, LiDAR coverage at long range.
By relocating the sensors to the SensorPods located on the side-mounted mirrors, Kodiak has simplified the build process and fundamentally improved the maintainability of the system. By having sensors located in an easy-to-reach location on the mirrors, customers avoid having to access the roof to maintain sensors.
Roads are designed around a human driver's line of sight. Kodiak's SensorPods are also designed to place sensors at the same height as a driver, maximizing road safety and improving perception. The SensorPods offer a better dual vantage point, as they provide redundancy and visibility on either side of the truck, as opposed to the single vantage point above the cab. In the event of a sensor damage, such as a rock or other piece of debris damaging a sensor, offering dual-redundant front-facing sensors increases resiliency. An on-the-fly replacement of SensorPods, which are compatible with any truck platform, can be performed in as little as ten minutes, maximizing uptime and customers' revenue generation due to increased asset utilization. The damaged SensorPod can then be returned to Kodiak for evaluation and repair.
Kodiak's already highly-modular hardware approach now includes fewer required modifications and touch points. This enables more cost-effective integration into trucks, which marks a significant step toward commercial deployment of the Kodiak Driver.
The Industry's Most Robust Sensor Array
The fifth-generation Kodiak truck improves upon the sensor array announced as part of its prior-generation platform. When removing the center pod, the company added a second forward-facing LiDAR and additional camera to add redundancy in the left and right SensorPods. The new truck increases the total number of sensors on-board from 14 to 18, including one new lidar and three new cameras—bringing the total camera count to 10. Two wide-angle cameras were added to the hood-mounted mirrors to cover blindspots. With the new sensor additions, Kodiak fifth-generation truck remains the most lean and fully-redundant platform in the industry.
Kodiak's long-range sensor suite includes the following split evenly between the two side-mounted mirror SensorPods: f four ZF Full Range Radar for redundancy; two Hesai 360-degree scanning LiDARs for side- and rear-view detection; two Luminar Iris LiDAR sensors; and 8 cameras, which include both wide and narrow field-of-views. The new truck includes the recently announced Ambarella CV2 perception system-on-chip (SoC) which handles all camera data processing. The Ambarella CV2 SoC improves image quality for longer range detections and unlocks improved dynamic range for nighttime driving.
"Customers and OEMs aren't sensor experts, and they shouldn't have to be, which is why they constantly tell us they love our modular approach that solves one of the biggest barriers to servicing and maintaining autonomous trucks," said Don Burnette, Founder and CEO of Kodiak Robotics. "We took a platform that our customers already love and made it better by adding more visibility, more power, and more flexibility, ultimately moving us closer down the path towards driverless deployment. By removing the sensors from the top of the truck and incorporating them at a human driver's line of sight, we have designed a system for the real world. Additionally, having sensors on top of the cab is actually very difficult to service while on the road and requires specialized equipment, which is nearly impossible to find roadside."
Kodiak's fifth-generation truck also includes aerospace- and military-grade technology. The main connector for data and power in Kodiak's SensorPods and compute system is designed for use in aviation, aerospace and military applications. The increased robustness of the hardware system is another step forward for Kodiak's deployment-readiness.
Improved Hardware Stack Offers Better Performance
Kodiak's hardware stack is designed for three activities: sensing, through its SensorPods; thinking, through its main compute; and acting, which is controlled through two onboard custom-designed safety computers, the Kodiak Actuation Control Engine, or ACE.
Kodiak also reduced the electrical power requirements for its fifth-generation truck, while simultaneously improving the processing power of the system. In addition to 130% more GPU processing power, the new system provides 60% more central processing power, and additional system redundancy. The reduced power consumption allowed for a 50% reduction in the size of the fifth-generation power system, and also decreased cooling needs.
Kodiak is also taking a modular approach to building its computing system, simplifying the integration of the system into the truck and making it easier to manage when the trucks are incorporated into a customer's fleet. Kodiak has consolidated its in-house compute system, networking, and power distribution into one physical unit, which can be built to accommodate the unique specs of each customer, giving more options for integration. The high-performance compute hardware is manufactured by Crystal Group, a global leader in manufacturing military and ruggedized computers, and is designed to handle the heavy and persistent vibrations onboard long-haul trucks.
Like Kodiak's fourth-generation truck, Kodiak's fifth-generation truck includes Cummins X15TM Series engines, and Bridgestone America's smart-sensing tire technology. The introduction of this new generation platform comes during a period of substantial growth for Kodiak. The company recently announced a 24-month United States Department of Defense (DoD) project to help automate future U.S. Army ground vehicles. Advancements made within the scope of the project have served as the foundation for the fifth-generation truck. Kodiak has recently announced partnerships with IKEA, Werner, Pilot Company, Forward and more. For more information about Kodiak, please visit https://kodiak.ai.
About Kodiak Robotics, Inc.
Kodiak Robotics, Inc. was founded in 2018 to develop autonomous technology that carries freight forward — so people, partners, and the planet thrive. The company is developing an industry-leading technology stack purpose-built for long-haul trucks, making the freight industry safer and more efficient. Kodiak's unique modular hardware approach integrates sensors into a streamlined sensor-pod structure that optimizes for perception, scalability, and maintainability. The company delivers freight daily for its customers across the South, operating autonomously on the highway portions of the routes. Kodiak also leverages its commercial self-driving software to develop, test and deploy autonomous capabilities for the U.S. Department of Defense. Learn more about Kodiak on the web at kodiak.ai, and on LinkedIn and Twitter.
Featured Product
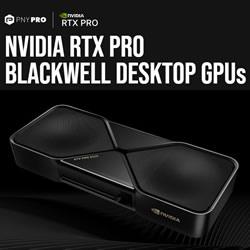