Digital Twins: Transforming Industrial Design and Maintenance in a Technological Revolution
In a groundbreaking leap forward for industrial automation, the concept of digital twins is taking center stage, promising to redefine the way industries design, operate, and maintain complex systems.
Pune, Maharashtra, 29th Oct — In a groundbreaking leap forward for industrial automation, the concept of digital twins is taking center stage, promising to redefine the way industries design, operate, and maintain complex systems. This revolutionary technology, powered by real-time data analytics and the Internet of Things (IoT), is set to improve efficiency, minimize downtime, and assist in a new era of predictive maintenance.
Digital twins are dynamic, data-driven virtual replicas of physical objects, processes, or systems. These virtual counterparts go far beyond mere 3D models, continuously gathering and updating data from their real-world counterparts to provide a comprehensive, real-time representation.
Implementing Digital Twins for Industrial Modernization
Digital twins are already playing an important role in the modernization of industries worldwide, bringing about considerable benefits:
1. Real-time Monitoring and Data Collection: Sensors and IoT devices are strategically embedded within physical assets to capture an array of vital data, including temperature, pressure, vibration, and more. This data is then transmitted to the digital twin, creating a dynamic reflection of the physical asset's state.
2. Simulation and Predictive Analysis: Digital twins are not static models; they are dynamic simulations capable of mimicking real-world scenarios. Leveraging advanced AI and machine learning algorithms, digital twins can estimate future behavior based on historical data and current conditions. This ability is essential for preemptive maintenance, enabling the identification and resolution of potential concerns before they result in downtime or costly failures.
3. Remote Monitoring and Control: With many industrial systems dispersed across huge geographical areas, digital twins facilitate remote monitoring and control. Operators can oversee and manage assets from anywhere globally, significantly enhancing operational efficiency and responsiveness.
The Role of Digital Twins in Modern Manufacturing and Predictive Maintenance
1. Modern Manufacturing: Digital twins have become the foundation of modern manufacturing processes. They streamline the design and optimization of production lines and equipment, enabling virtual testing and scenario analysis before implementation in the physical world. This not only minimizes trial-and-error but also accelerates time-to-market for new products.
2. Predictive Maintenance: Perhaps one of the most significant contributions of digital twins is their role in predictive maintenance. Unlike traditional maintenance practices, which are often reactive and based on fixed schedules, digital twins provide real-time insights into equipment health and performance. When anomalies or signs of wear and tear are detected, they trigger immediate alerts for proactive maintenance. This results in minimized downtime, extended asset lifespans, and substantial cost savings.
In conclusion, digital twins are leading a transformation in industrial design and maintenance, providing real-time, data-driven, and predictive capabilities that optimize asset management. As technology continues to advance, digital twins are set to play an increasingly important role in shaping the future of industrial automation. Adopting this groundbreaking technology is no longer an option but a necessity for industries aiming to maintain a competitive edge in today's dynamic landscape.
Links
Looking to improve your factory's manufacturing productivity, please visit us at: https://kneo.in/
About KNEO
Kneo has been engaged in the field of industrial automation in various sectors of the economy like Automotive, Food, and beverages, Textile, Process, etc. Along with Automation operations, they are also providing solutions in the IT- OT domain. KNEO helps in automating processes with various Industrial automation services. Their Industry 4.0 solution includes a Performance monitoring system, an advanced scheduling module, a track and trace module, etc.
Featured Product
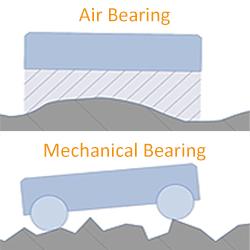