Flexxbotics Presents Robot Compatibility with Hexagon In-line Inspection Equipment at Sixth Sense Summit
Flexxbotics’ patent-pending FlexxCORE technology enables the robots to securely connect and communicate with Hexagon machines to provide closed-loop feedback and real-time updates to the inspection equipment for autonomous process control.
London, England - February 7, 2024 - Flexxbotics, delivering workcell digitalization for robot-driven manufacturing, today announced it will present robot connectivity compatible with the entire range of Hexagon inspection products at Hexagon's Sixth Sense Summit being conducted at the CodeNode innovation center in Central London on Wednesday 7 February 2024. Attend in-person or watch online with free registration.
Flexxbotics' patent-pending FlexxCORE technology enables the robots to securely connect and communicate with Hexagon machines to provide closed-loop feedback and real-time updates to the inspection equipment for autonomous process control. With Flexxbotics manufacturers can enable advanced robotic machine tending with CNC machinery and Hexagon inspection technology to achieve six sigma quality for increased yields with improved margins.
Hexagon provides a wide range of Coordinate Measuring Machines (CMMs) for high precision measuring tasks, as well as, laser scanners, laser tool setters, infrared probing systems, radio wave-probing systems and production probe systems. Flexxbotics compatibility includes Hexagon's PC-DMIS CMM for bridge and gantry CMMs, NC measuring software, the full Q-DAS product line for Statistical Process Control (SPS), and Intelligent Machine Control (IMC).
Flexxbotics was selected from hundreds of applicants across 27 countries by Hexagon's Manufacturing Intelligence division to join the elite Sixth Sense program. The initiative is designed to nurture high-growth companies within the manufacturing industry by supporting them with Hexagon's extensive resources.
Flexxbotics robotic workcell digitalization is the backbone of the Smart Factory, delivering robot-driven manufacturing at scale with autonomous process control for advanced machining operations. Flexxbotics' SaaS/hybrid architecture also runs both online and offline so production continues with or without internet access, and Flexxbotics works with existing business systems such as CAD/CAM, DNC, SCADA/HMI, IIoT, MES, ERP, PLM and others for enterprise-wide synchronization.
A full set of bidirectional communication, transform and routing capabilities are available in Flexxbotics for the robots and machinery that are connected including loading programs, sending instructions, updating parameters and status awareness depending on the equipment's capabilities so the robots drive the Hexagon equipment along with the CNC machines in the smart factory.
"We believe that the inspection equipment in the smart factory effectively becomes the ‘eyes & ears' of the robots running production in ‘lights out' manufacturing," said Tyler Bouchard, Co-founder & CEO of Flexxbotics. "By connecting Hexagon's inspection capabilities to robots with Flexxbotics, global companies are able to achieve continuous operations through robot-driven manufacturing with autonomous process control."
About Flexxbotics
Flexxbotics robotic workcell digitalization is the backbone of the Smart Factory delivering autonomous process control for next generation machining environments. Flexxbotics SaaS/hybrid solutions enable robot-driven manufacturing at scale. Flexxbotics breakthrough, the FlexxCORE™ technology, seamlessly connects and coordinates robots with existing automation equipment, IT systems and people. More powerful, flexible and open, Flexxbotics revolutionizes the use of robotics in complex production. Visit www.flexxbotics.com to learn more and follow us on LinkedIn.
Featured Product
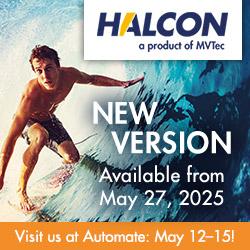