Ultra-Low Profile XY-Theta Nanopositioning Stage Uses Air Bearings
Unique and compact 3-axis precision motion platform, new from PI
Auburn, MA - PI, a global leader in precision motion control and nanopositioning products releases a unique planar XY-Theta-Z nanopositioning stage based on air bearings and direct drive motors. Unlike conventional multi-axis stages, the A-361 employs only one moving platform shared among all three axes. One of its advantages is the ultra-low profile of only 40mm, despite featuring an integrated vacuum chuck to accommodate wafers or other samples. Engineered as a parallel-kinematic multi-axis system, this stage delivers exceptional precision in a remarkably compact package.
Non-Contact, Maintenance-Free
By incorporating non-contact components, it ensures frictionless operation, thereby offering not only ultra-high precision but also superior performance and a completely maintenance-free, virtually infinite service life. The built-in position-locking capability proves useful for operations requiring utmost stability with zero servo jitter.
Clean-room Compatible
Due to the completely contact-free operation, and the lack of lubricants, the XY-Theta stage is an excellent fit for clean room applications.
6-DOF Upgrade
If precision motion in 6 axes is needed, the A-361 XY-Theta stage can be seamlessly integrated with the A-523 Z Tip/Tilt stage creating a compact 6 degrees of freedom nanopositioning system with only 100mm total height. 6-axis nanopositioning systems are often used in photonics alignment and semiconductor inspection applications.
More information on the A-361 Low profile XY-Theta Air Bearing Multi-Axis Nanopositioning Stage
Industries Served
Semiconductor test and metrology, wafer inspection, photonics alignment, fiber positioning, optics alignment, flat screen inspection, maskless lithography, and ultra-LED manufacturing. The noncontact design is ideal for cleanroom applications.
Featured Product
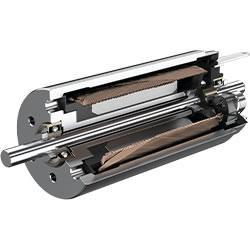