Granite-Based, Engineered Motion Systems Provide Easily Configurable High-Precision, Multi-Axis Motion
Integrated Multi-Axis Motion System (IMAS), geared towards a broad range of industrial precision motion applications, is highly customizable and available with short lead times.
Auburn, MA - PI's new X-417 Integrated Multi-Axis System (IMAS) provides machine builders and system integrators with a freely configurable solution, utilizing highly dynamic, precision XY linear stages as a base, with travel ranges from 4 to 16 inches (102 mm to 407 mm). The X-417's modularity allows users to configure the system according to their application needs, including travel ranges, the number of axes required, and a choice of accessories. They receive a custom-tuned system, aligned and calibrated to their specified requirements.
X-417 systems are available in three performance classes, each including a suitable EtherCAT®-based high-performance motion controller from PI. All systems, except for the entry-level performance class, are based on a linear motor-driven XY stage with a user-selected travel range and load capacity. The system is expandable with rotary and Z-stages, which can be mounted either on the XY stage or separately on the granite bridge or bracket. Users can also select base plates made of granite, brackets made of aluminum or granite, and additional accessories such as a base frame with integrated vibration isolation. The user-configured system will be delivered with suitable cables and appropriate cable management.
Application Fields
Metrology. Laser machining: Laser ablation. Laser welding. Ultrashort pulse laser machining. Laser micromachining. Laser drilling. Galvo integration. Ceramics and diamond cutting. Test & inspection. Electronics manufacturing.
Featured Product
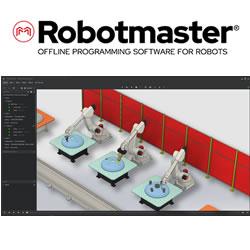