Is Your OEM-Provided SECS/GEM System Falling Short in Performance and Reliability?
The SECS/GEM communication protocol is the lifeline of semiconductor manufacturing, enabling seamless communication between equipment and factory automation systems. It ensures efficient data exchange, standardized operations, and the scalability required to meet the demands of modern fabs.
However, not all SECS/GEM implementations are created equal. Many Original Equipment Manufacturer (OEM)-provided systems fall short in terms of performance and reliability, leaving manufacturers grappling with inefficiencies, delays, and costly downtime.
In this blog, we explore the common challenges of OEM-provided SECS/GEM systems and why third-party solutions may hold the key to achieving better results.
Common Performance and Reliability Challenges
Limited Customization
OEM solutions are often designed for broad compatibility rather than specific use cases. This lack of flexibility can result in mismatched workflows, suboptimal data formats, and inefficiencies in fab operations.
Scalability Issues
As production scales or new automation technologies are introduced, OEM systems frequently struggle to adapt. These limitations hinder the ability to respond to market demands or incorporate advanced manufacturing processes.
Data Latency & Throughput Concerns
Real-time processing is critical in semiconductor manufacturing, but OEM systems can suffer from data exchange delays and limited throughput, impacting operational efficiency and decision-making.
Poor Error Handling & Recovery Mechanisms
Downtime caused by communication errors or equipment failures can be exacerbated by inadequate error-handling protocols in OEM systems, leading to extended production disruptions.
Compatibility Problems
Many OEM systems face challenges when interfacing with legacy equipment or tools from other vendors, resulting in costly integration issues or requiring additional workarounds.
Why a Third-Party SECS/GEM Solution May Be the Answer
Third-party SECS/GEM solutions offer a range of advantages that can address these challenges effectively:
Improved Adaptability & Customization
Unlike one-size-fits-all OEM systems, third-party solutions can be tailored to match unique fab requirements. Custom workflows, data mapping, and specific automation commands ensure seamless integration.
Enhanced Performance Optimization
Advanced communication protocols in third-party systems enable faster and more reliable data exchange. This results in reduced latency, improved throughput, and smoother operations.
Robust Error Handling & Predictive Diagnostics
Modern SECS/GEM systems from third-party providers feature proactive monitoring, predictive analytics, and advanced error recovery mechanisms to minimize downtime and maintain operational stability.
Seamless Interoperability
Designed with compatibility in mind, third-party solutions integrate effortlessly across a diverse range of equipment vendors and legacy systems, eliminating the need for complex modifications.
Key Considerations When Upgrading
Transitioning from an OEM-provided SECS/GEM system to a third-party solution is a significant decision. Here are some key factors to evaluate:
ROI Analysis
Weigh the costs of implementing a third-party solution against the tangible benefits, such as improved efficiency, reduced downtime, and scalability. Consider the long-term gains in productivity and operational reliability.
Compatibility Assessment
Evaluate how the new system will interact with your existing equipment and automation platforms. Ensure the provider offers comprehensive support for integration.
Vendor Expertise and Support
Choose a third-party provider with a proven track record in SECS/GEM implementations. Reliable technical support and expertise are essential for a smooth transition.
Case Studies and References
Review successful case studies of other fabs that have upgraded to third-party SECS/GEM solutions. Learning from their experiences can provide valuable insights and confidence in your decision.
Conclusion
While OEM-provided SECS/GEM systems may fulfill basic operational needs, they often fall short in performance, reliability, and scalability as manufacturing demands evolve. Upgrading to a third-party SECS/GEM solution can provide the adaptability, efficiency, and robustness needed to meet the challenges of modern semiconductor manufacturing.
Investing in a tailored solution not only optimizes your operations but also future-proofs your fab for growth and innovation.
Are you ready to take your SECS/GEM system to the next level? Contact us today to explore customized solutions for your fab's unique needs.
Featured Product
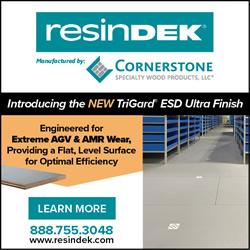
ResinDek® TRIGARD® ESD ULTRA FOR HIGH-TRAFFIC ROBOTIC APPLICATIONS
To maximize the productivity of an autonomous mobile robot (AMR) or automatic guided vehicle (AGV) deployment, it's critical to create the optimal environment that allows the vehicles to perform at their peak. For that reason, Cornerstone Specialty Wood Products, LLC® (www.resindek.com) created the TriGard® ESD Ultra finish for its ResinDek® engineered flooring panels. The TriGard ESD Ultra finish is ideal for high-traffic robotic applications characterized by highly repetitive movement patterns and defined travel paths.