How YiHai Laser’s Precision Tools Are Fueling the Next Wave of Robotic Manufacturing
The quietest revolution on your factory floor isn't the robots - it's the photon beams empowering them. As global manufacturers grapple with skilled labor shortages and tolerance demands approaching the width of a human hair, the marriage of industrial robotics and advanced laser technology has shifted from luxury to survival. For automation engineers tired of compromising between speed and precision, YiHai Laser's robotic-ready systems are rewriting production rules.
Why Lasers Are Becoming Robotics' Right Hand
- Automotive Tier 1 Supplier, Bavaria
The math is brutal:
72% of manufacturers cite welding/cutting as their largest skilled labor gap (McKinsey 2024)
Traditional processes waste 18-37% of material on complex contours
Post-process grinding consumes 22% of robotic cycle time
YiHai's answer: Integrated laser systems that turn robotic arms into hyper-precise tools:
Cutting: ±0.03mm tolerance vs. plasma's ±0.8mm
Welding: 10 m/min speeds vs. TIG's 0.5 m/min
Zero post-processing on 93% of applications
Inside YiHai's Robotic Revolution: Where Photons Meet Automation
1. The SeamTracker™ Difference: No More Teach Pendant Guesswork
While standard laser systems stumble on uneven seams, YiHai's patented vision system:
Scans joints at 500 Hz with 0.005mm resolution
Auto-adjusts beam focal position ±1.5mm in real-time
Compensates for thermal distortion during welding
Case Study: Heavy equipment maker reduced pressure vessel scrap from 17% to 0.4% using SeamTracker on 80mm thick Inconel.
2. HyperSync Integration: One Language for Bot and Beam
Forget clunky communication protocols. YiHai's native support includes:
ROS 2.0 for research environments
FANUC DCS, KUKA. KRL, ABB RAPID for production
Single-cable solutions (power + data + coolant)
"We integrated 6 YiHai 8kW lasers with 32 KUKA KR QUANTEC arms in 11 days - half our projected downtime."
- SpaceX Fabrication Partner, Texas
3. Lights-Out Laser Architecture
When your graveyard shift runs unmanned, reliability is non-negotiable:
Predictive Optics Health Monitoring: Warns of lens degradation 80+ hours pre-failure
Auto-Calibration: Maintains beam alignment after 10,000+ hours
Remote Power Adjustment: Cloud-based kW tweaks for material changes
Head-to-Head: YiHai vs. Traditional Automation Laser Solutions
Capability Legacy EU Systems YiHai RoboLase Pro Advantage
Max Cutting Speed (1mm SS) 48 m/min 82 m/min (BrightCore™) +71%
Weld Seam Consistency ±0.15mm ±0.03mm (SeamTracker™) 5X tighter
Recalibration Time 45-90 min 0 (AutoSync) Eliminated
Power-per-kW Footprint 1.8 m² 0.9 m² (StackCool™) 50% smaller
Multi-Robot Control 1:1 ratio 1:4 (HyperHub) 300% saving
Emergency Service Response 24-72 hrs 4 hrs (Global SLA) 92% faster
Real-World Applications Transforming Automation
1. Battery Manufacturing: Where Microns Equal Millions
YiHai's 200W pulsed lasers now dominate EV battery production:
Tab Welding: 0.08mm variance across 2,400 welds/hour
Case Sealing: Hermetic seals at 1.7m/min (vs. 0.3m/min laser competitors)
Zero Splatter: Eliminates short-circuit risks in prismatic cells
*"After switching to YiHai, our dendrite-related failures dropped from 1:800 to 1:12,000 cells."*
- Top 3 EV Battery Producers
2. Aerospace Robotics: Cutting Where Humans Can't
Automating titanium aircraft components demands insane precision:
3D Contour Cutting: 40mm Ti64 at 0.8m/min with 0.1° angular precision
EBW Replacement: Laser welding engine mounts at 60% cost of electron beam
Drone Frame Assembly: 120-second cycle time for complex carbon-fiber joints
3. Medical Device Automation: Sterilizable Precision
YiHai's cleanroom-certified lasers enable:
Get a free workflow analysis from YiHai automation engineers
Web: yihailasers.com
Email: yhlaser@yihaicnc.com
Stent cutting with 5µm tolerances
Hermetic sealing of pacemaker capsules
Marking surgical tools with subsurface engraving
The Cost of Compromise: Why "Cheaper" Lasers Cripple Automation Cells
The hidden expenses of underpowered lasers:
Positional Drift: Thermal instability causes 0.2mm/hour tool center point shift
Reject Rates: 4-7% typical on budget systems vs. <0.5% with YiHai
Robot Wear: Compensating for beam inconsistencies accelerates joint degradation
Independent Study: Systems using YiHai lasers showed 23,000+ hours before first robotic component failure vs. 11,000 hours with alternatives.
Future-Proofing Your Automation: YiHai's 2030 Roadmap
Already in beta with select partners:
AI Beam Shaping: Dynamically adjusts spot profile mid-weld based on thermal imaging
Quantum-Key Encryption: Prevents IP theft of cutting/welding parameters
Holographic Monitoring: 3D process visualization without cameras
The ROI Reality: Crunching the Numbers
Metric Traditional Automation YiHai-Powered Cell Improvement
Upfront Cost (6kW system) $412,000 $387,000 6% savings
Cycle Time (battery tray) 8.7 min 3.2 min 63% faster
Energy Consumption 38 kWh/hour 21 kWh/hour 45% less
Annual Maintenance $18,700 $6,300 66% lower
Scrap Rate 4.1% 0.6% 85% reduction
3-Year Savings - $1.4M+ -
Engineer to Engineer: Why We Built Differently
"While competitors focus on laser physics, we obsess over integration pain points."
- Dr. Elena Rodriguez, YiHai Chief Robotics Engineer
Problem: Robotic wobble during high-speed cutting
YiHai Solution: The Inertial Compensation Algorithm uses the robot's own encoders to predict vibration
Problem: Fogged optics during humid shifts
YiHai Solution: Nano-coated self-drying lenses (patent pending)
Problem: Cell integration complexity
YiHai Solution: Pre-validated robot calibration packages
Your Move Toward Uncompromised Automation
The race toward lights-out manufacturing isn't coming - it's here. YiHai's robotic laser systems deliver the trifecta:
German-level precision at Asia-level costs
Japanese reliability with Silicon Valley connectivity
American-scale support and 4-hour emergency response
Ready to eliminate your automation bottlenecks?
Featured Product
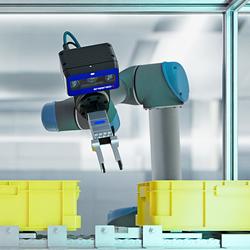
3D Vision: Ensenso B now also available as a mono version!
This compact 3D camera series combines a very short working distance, a large field of view and a high depth of field - perfect for bin picking applications. With its ability to capture multiple objects over a large area, it can help robots empty containers more efficiently. Now available from IDS Imaging Development Systems. In the color version of the Ensenso B, the stereo system is equipped with two RGB image sensors. This saves additional sensors and reduces installation space and hardware costs. Now, you can also choose your model to be equipped with two 5 MP mono sensors, achieving impressively high spatial precision. With enhanced sharpness and accuracy, you can tackle applications where absolute precision is essential. The great strength of the Ensenso B lies in the very precise detection of objects at close range. It offers a wide field of view and an impressively high depth of field. This means that the area in which an object is in focus is unusually large. At a distance of 30 centimetres between the camera and the object, the Z-accuracy is approx. 0.1 millimetres. The maximum working distance is 2 meters. This 3D camera series complies with protection class IP65/67 and is ideal for use in industrial environments.