Closing the AI Ambition - Execution Gap in Manufacturing
While most manufacturing companies have begun to explore the next step in automation technology -- artificial intelligence (AI) and machine learning (ML) -- a large gap exists between where they want their organizations to be with AI technology and where they are.
In 2019, the Association for Advancing Automation (A3) surveyed its member companies about their adoption of AI. At the time, more than 76 percent of respondents said that AI will be important to their companies in the next three years, but fewer than 5 percent noted that they were already widely implementing AI. Nearly two years later, this gap between ambition and execution in manufacturing companies has largely remained static, even though — in many cases — the physical infrastructure for the “factory of the future” has already been deployed.
So what’s keeping companies on the wrong side of the ambition-execution gap? They're trying to do what they've always done and hoping for a better result. That won't work because traditional manufacturing systems and processes are incredibly inflexible.
Typically, a manufacturing process is created and optimized for a single product or function. If the process needs to be modified, say to produce a new version of a product or for the new model year, it requires a complete overhaul to accommodate the new product.
The challenge manufacturing companies face today is how to make these rigid systems more flexible, especially in the context of automation.Ripping out the existing systems and building something new from the ground up isn’t a viable option -- either financially or logistically. By deploying AI/ML software as a layer atop existing networking and compute infrastructure, companies can cost-effectively make their previously rigid manufacturing processes more flexible and close the ambition-execution gap.
In addition to cost savings and increased flexibility, acceptance of AI systems on the factory floor is an important metric in adoption. For Symbio, the key is that it’s not simply automation; it’s a collaboration between human and machine. Rather than displace humans, companies can design systems that people engage with more efficiently and, with efficient human-machine interaction, changes can happen automatically. What’s more, designing and valuing automation in the right way -- for example, along the lines of capacity rather than just the labor component -- develops trust between manufacturing teams. This creates an opportunity to generate more valuable, creative, and desirable jobs in other areas. Adding AI & ML to existing automation, or even to automation that’s currently being deployed, enables manufacturers to future-proof systems and processes.
Comments (0)
This post does not have any comments. Be the first to leave a comment below.
Featured Product
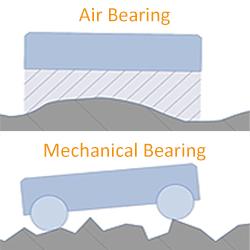