Why AMRs Are Being Adopted On Factory Floors
The autonomous mobile robot (AMR) market has been heavily driven by logistics customers. So much so that the image of an AMR gliding round a warehouse has become almost synonymous with e-commerce. In contrast to this, automated guided vehicles (AGVs) – the other type of vehicle within the wider mobile robot market – are primarily sold into manufacturing applications. The big difference between the two is that AMRs feature onboard navigation.
In 2022 logistics will overtake manufacturing as the largest user of mobile robots. But this disguises a key trend: AMRs are making major inroads into factories. And it is important that AMR vendors are conscious of the rapidly growing opportunities in manufacturing, because there are strong reasons why AMRs are well suited to modern factory environments. Right now, it is Chinese factories that are furthest ahead in recognizing the potential of AMRs. But this is a global trend and AMRs will soon be ubiquitous on factory floors around the world.
Sales of mobile robots are growing more rapidly in logistics- major opportunities in manufacturing
Manufacturing is unique
Manufacturing customers have unique operational needs. And, compared to logistics warehouses, these needs are complex. Logistics AMR applications are usually focused on goods-to-person (G2P), a relatively mature technology. G2P is a standardized application, making it relatively easy to deploy standardized AMR technology at large scales.
Things are trickier in manufacturing. There are far more people on production lines than there are in warehouses, and far more complex activities tend to take place. Using AMRs alongside production lines therefore requires the ability to interact with much more diverse equipment and machinery in multiple ways. And there tend to be many more instances of human-machine interaction than would be encountered in a warehouse too.
For AMRs to operate in factories they therefore must usually be highly customized, and they must meet much more stringent safety and accuracy requirements. Additionally, manufacturing operations have an increasing need for flexibility as factories respond to growing demands for mass customization (i.e. the production of custom-made products at low unit costs). Every manufacturing industry segment has its own specific requirements. And, even within segments, application scenarios often vary widely. Applying AMRs to the factory floor is therefore a tough challenge for AMR vendors.
The issue is that rolling out AMRs on production floors essentially becomes a system integration project – introducing layers of complexity at the deployment stage that are rarely encountered in logistics environments. But there is an upside for vendors too because this complexity provides major opportunities for specialization. AMR companies that target specific manufacturing segments or applications and become specialists in those areas will find strong opportunities for growth.
The challenge is knowing which industries to target, and which new technologies to deploy.
New technologies and industries – the China example
New technologies are making deployment of AMRs in manufacturing far simpler. Navigational technology is a particular challenge. One example that has been widely used at manufacturing sites in China is SLAM (simultaneous localization and mapping) navigation. SLAM is particularly heavily used in AMRs in 3C (computers, communications, and consumer electronics) manufacturing environments. Additionally automotive in China has historically always been the single largest user of mobile robots, and the sector is now becoming a front line in the competition between AGVs and AMRs. AGV’s are still in the lead, but we’ve seen some major recent customers such as Toyota making large deployments of QR code ‘bots’ on assembly lines.
When it comes to new industries in China, there has been explosive growth in advanced manufacturing sectors such as photovoltaics, batteries, and electronics – specifically 3C and semiconductor – manufacturing. All these sectors are also becoming major users of AMRs. For example, electronics manufacturers are rapidly adopting robotics in order to be able to manage ever-shortening lifecycles of consumer goods and an ever-increasing range of SKUs. We expect massive growth in AMRs sold to these customers in 2021. And, in China, 3C and semiconductor electronics manufacturers could well overtake automotive as the single biggest user of mobile robots in 2025.
Today China, tomorrow the world
Chinese manufacturing has benefitted massively from abundant cheap labor. This is changing. China is experiencing a labor shortage made worse by the fact that, as their economy booms, young people are spurning production line jobs. The labor problem is possibly the single most important driver of the adoption of AMRs in Chinese manufacturing. But labor shortages in general, and a disdain for production jobs in particular, is not unique to China. In fact, these trends are far more pronounced in the USA, Europe, Japan, and other advanced economies.
Additionally, re-shoring in manufacturing is becoming an important trend. This is being partly driven by the increased costs of Chinese labor and of international shipping. But it is also being driven by politics. In particular, governments in the EU and the US are increasingly focused on ensuring key strategic goods such as semiconductors are manufactured locally to guarantee security of supply. China is therefore just a test case for large-scale deployment of AMRs in manufacturing around the world, and our forecasts show that AMR revenues in manufacturing are set for strong growth globally.
Comments (0)
This post does not have any comments. Be the first to leave a comment below.
Featured Product
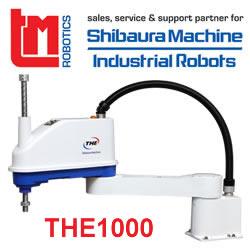