What Are the Benefits of Robotic Vision Systems?
Robotic vision systems allow robots to “see.” With a camera and an AI algorithm, robots can dynamically interpret their environment and interact with it.
In practice, the technology allows robots to interpret and respond to visual information relevant to their surroundings in near-real-time. The technology is essential for various modern manufacturing and warehousing automation applications.
These are some of the key benefits of robotic vision systems and how businesses are already using robotic vision systems.
AI and Machine Vision for Dynamic Navigation
Autonomous mobile robots (AMRs) are light industrial robots that use machine vision to pilot themselves and perform basic warehousing tasks.
Object classification algorithms help the AMRs identify navigable space and obstacles, identify human workers, and determine safe working distances.
As a result, the AMR can effectively steer itself around a warehouse without the need for specialized guidance infrastructure or predefined paths – a significant improvement over more rudimentary robots, like autonomous guided vehicles (AGVs).
These robots were also capable of navigating with little to no human oversight but required guidance infrastructure that was often costly to engineer, maintain, and adapt as warehouse needs changed.
By virtue of not being bound to preset aisles, lanes, or paths, AMRs can help automate warehouse tasks without sacrificing warehouse flexibility.
AGV infrastructure required careful engineering and then reconfiguration whenever the needs of the warehouse changed significantly. AMRs, in contrast, can use machine vision and additional data – like GPS tracking information – to navigate a site dynamically.
Designing and implementing these systems is often a major undertaking. Even the equipment used in testing each robot’s electro-optical systems needs to be carefully considered. Once implemented, however, the AMR can boost productivity and may require minimal human oversight during normal operations.
The robot may be able to steer around site debris – like pallets, packaging, and other items – as well as identify human workers. Using the same visual processing algorithm, the robot can also determine how much distance it needs to give obstacles and workers to avoid a struck-by incident or similar issue.
The same classification algorithms that can help an AMR navigate the site may also be used for basic warehousing tasks. With machine vision, robot designers can make mobile robots both more autonomous and better at navigating dynamic, changing environments without the need for human oversight.
AMRs, along with other trending warehouse automation technologies, are most useful in factories and warehouses where warehouse needs are frequently changing.
In these facilities, there isn’t always labor available for essential tasks that require sorting and moving goods – like picking, packing, inventorying, and similar work – and automated solutions can help relieve the pressure on human workers.
Improving Automation and Quality Control With Machine Vision
Industrial quality control is an essential process, and improving quality control can typically help a business reduce waste and improve productivity.
Expanding quality control is often a labor-intensive process and difficult to automate. While adding additional quality checks throughout a manufacturing process is usually desirable, it’s not always practical to dedicate labor to these checks.
Human workers also make mistakes, especially when work is tedious or repetitious. Some types of visual inspection that are essential for quality control – like ensuring each bottle in the production line is filled to a certain point – can be extremely difficult for a human worker to perform over and over again with accuracy.
Robotic vision systems enable a new kind of automated visual inspection system that can dynamically interpret the characteristics of raw materials, components, and finished goods without interrupting manufacturing workflows.
These systems are capable of incredible feats of efficiency. For example, Heineken has begun using robotic vision for quality control at a beer-bottling facility in France, where the system “inspects 80,000 bottles per hour and practically achieves a 0% failure rate.”
While a human quality control inspector may grow tired or inconsistent over the course of their shift, a machine vision quality control system is remarkably consistent, allowing businesses to further cut down on error and maximize return on investment for quality control.
In the same way an AMR uses AI to identify obstacles and workers, the visual inspection system uses AI algorithms to identify different objects and their material characteristics. Defective parts or raw materials can be automatically removed from the production line or flagged for review, signaling to management that something has gone wrong.
While still experimental, machine vision is increasingly common in various manufacturing sectors – particularly food and beverage manufacturing, where the technology helps ensure both product quality and regulatory compliance.
How Robotic Vision Can Help Improve Cobot Function and Safety
New collaborative robots (or cobots) are built to work in close proximity to human workers. For these robots, robot vision systems are often an essential tool that helps extend bot functionality.
These robots are built for flexibility. Cobots are typically easy to program and light enough to move from workstation to workstation. Machine vision makes them even more flexible, enabling a range of vision-guided robot (VGR) applications, including pick-and-place, machine tending, and assembly.
Some advanced systems can even use machine vision to perform complex bin-picking tasks. These tasks have traditionally been difficult to automate. Machine vision makes it possible for the cobot to work alongside a human worker, providing support without disrupting existing workflows. As a result, the cobot can free up human labor for more important tasks and aid workers as needed.
Robotic vision can also play an important role in robot safety. In the same way an AMR can use machine vision to dynamically interpret its surroundings, cobots use machine vision to calculate safe motions that enable complex tasks without threatening human safety.
For example, a cobot could use machine vision to analyze the location, in real-time, of human workers, components, and other machines.
As a human worker performs tasks, a cobot may dynamically reposition its equipment, like a robotic arm, while still performing its own work, ensuring safe operation without slowing production.
Robotic Vision Is Key to Cutting-Edge Automation Applications
Robotic vision systems are an increasingly important technology in a range of industries – particularly warehousing and manufacturing.
The technology, by allowing robots to dynamically interpret and respond to visual stimuli, enables a range of new types of automation, including quality control systems, cobots, and autonomous warehouse robotics.
Comments (0)
This post does not have any comments. Be the first to leave a comment below.
Featured Product
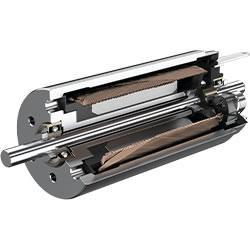