Is the Built Industry Ready to Embrace Robotics in 2023?
2023 is a pivotal year for the construction industry in many ways. Building professionals face an uphill battle to complete projects on time without delays, as the less-than-ideal economy has put a strain on their budgets, materials and other crucial resources. Advancements in robotics could help to mitigate these problems, but the industry as a whole must be ready to adopt new technology without further disruption.
Why the Construction Industry Needs Robotics
First, it’s essential to establish the proper sense of urgency around the construction industry’s problems. Aggravated by the COVID-19 pandemic, these three significant challenges pose the greatest threats:
- Housing crisis: The United States is short an estimated five million homes as of 2022. A mile-long backlog of residential projects needs completing, but builders don’t have the time or resources to finish them.
- Supply shortages: Global supply chain issues have left builders without essential materials such as lumber and steel. Prices are also sky-high due to inflation, which puts the limited available supplies out of reach for many contractors.
- The Great Resignation: Millions of construction workers left their jobs in recent years due to a multitude of factors, including low pay, poor working conditions and limited upward mobility. Retirement has also contributed in considerable numbers to The Great Resignation, leaving the industry with a need for more skilled laborers.
Needless to say, the stakes are incredibly high. Transitioning to new robotics would help building professionals address all three problems, but surveys have shown many companies aren’t ready to adopt new technology because they want to focus on rebuilding their workforces. They’re also worried about the implementation costs, which is understandable.
So, although many new resources in robotics are available, they’re either too expensive or too difficult to adopt for most contractors. The economy and labor force need to restabilize before independent contractors, small businesses and other local operations can adopt these technologies.
Despite what these surveys say, contractors will have to transition eventually. Industry leaders can’t afford to wait much longer as economic conditions continue to decline. For that reason, it’s still worth looking at recent advancements and exploring their benefits. These eight noteworthy technologies could revolutionize the construction industry if adopted on a wide scale.
1.3D Printing
Although it’s not technically a robot, 3D printing is the technology with the greatest potential to shake up construction. Builders can print homes from scratch for as low as $4,000 while also consuming far less time, energy and resources than traditional construction practices. The finished products are as durable and stylish as standard homes.
3D printing also plays a key role in the advancement of green building. It allows for the seamless mass production of sustainable homes, as the owners can choose to include solar shingles, draft-proof windows and other eco-friendly features in the design plan.
Government programs, 3D printing companies and non-profit organizations have already built entire neighborhoods thanks to this new technology. It could be critical in solving the housing crisis, conserving materials and compensating for the lack of skilled labor.
On a smaller scale, 3D printing allows companies to replace parts for damaged equipment without missing a beat, consolidating repair costs and keeping projects on schedule. If something breaks, a printer can produce the necessary pieces. This benefit will help contractors overcome supply shortages and delayed deliveries.
2.Autonomous Robots
Automated robots are other innovative gadgets that have improved the safety and efficiency of construction sites. Also powered by AI, they perform specific building tasks such as drilling, welding, digging and painting. Although construction employees are some of the hardest workers around, they can’t compete against the speed and precision of robotics.
Some notable examples of these autonomous robots include rebar-tying bots, self-driving heavy equipment, a bricklaying bot and a plastering machine that operates along with construction workers. They take care of much of the strenuous labor around the site and create a more optimal finished product. With fewer opportunities for human error, project quality can drastically improve.
These robots also benefit the environment because they contribute to more energy-efficient construction, generate less waste and use minimal materials. An innovative construction project is an eco-friendly construction project.
Drones have evolved into valuable construction tools. They play the same role as human inspectors, flying around the site and capturing any safety or security threats that get past the manager. They might have started as fun toys, but drones are quickly becoming one of the construction industry’s most important tools.
3.On-Site Wearables
Wearable robotics are rapidly becoming commonplace on construction sites. Traditional equipment like hard hats and reflective vests have gotten some much-needed upgrades. Built-in artificial intelligence monitoring systems can track an employee’s activity levels, heart rate, air quality, hazardous materials and other relevant metrics that might impact their job performance or safety.
Wearables do much of the micromanaging around the site, ensuring the project stays on schedule with no injuries or equipment malfunctions that might cause a setback. Plus, they’re cheap. Contractors struggling with understaffing can improve their job site safety and equip their workers with this new gear. Over time, it can play a crucial role in attracting people to the building profession in greater numbers.
Along with AI, the Internet of Things is the glue that connects all wearables. It enables site managers to create a network of all the site’s electronics, collecting real-time information about each machine’s location and operation. This new level of supervision ensures each task completes on time and according to safety protocols.
4.Modular Building
Modular building is the foundation of an emerging trend called prefabricated construction. Instead of building everything on-site, contractors can utilize tools like the aforementioned construction software, wearables and robots to work on their projects in a controlled warehouse environment. It has become popular for several important reasons:
- Accessibility: Large projects such as apartments and commercial buildings are easier to complete with modular construction, giving people more housing and job opportunities.
- Safety: Working in the same indoor environment is much safer for the average laborer than working in different outdoor settings with many variables. This factor could get more people interested in working in construction again.
- Sustainability: Modular building requires less time, labor and resources to complete. It also helps reduce construction waste, as contractors can estimate how much material they need and avoid runoff more accurately.
At its best, modular building has proved to be up to 50% faster than current residential construction methods. Robotics play a key role in its success, allowing for the completion of essential tasks in settings that were previously unavailable to contractors.
5.Data Analytics
Data management was always a weak point for the construction industry until now. Instead of piling up dozens of documents from each project, contractors can now transition to centralized digital platforms and collect information much more efficiently. When your information is organized and accessible, you can get more relevant insights and make better-informed decisions.
Thorough data analytics also makes it possible to predict future events based on probability, job site conditions, weather forecasts, delivery delays and other important factors. Construction projects have many independent variables, so site managers must have the information to anticipate what might be around the corner.
Artificial intelligence plays a role in data analytics. Humans can only extrapolate so much information from a set of documents, but AI gets maximum value. It tirelessly sorts through pages and pages and never stops learning. The more data it receives, the more insights it can provide.
6.Virtual Reality
Virtual reality (VR) technology started as a fun gaming tool, but now building professionals are using it for training and upskilling. It allows new hires to practice their skills in simulated projects, providing an unmatched immersion level. They get exposed to realistic scenarios — including replicas of past situations — you could never recreate in real life.
For example, companies can create VR simulations for heavy equipment training and dangerous tasks like drilling. Rather than having new employees study safety protocols, building professionals can take an interactive approach and guarantee that their workers prepare for the real thing.
7.Augmented Reality
Augmented reality — the advanced version of virtual reality — is the ideal tool for simulating construction projects and training new employees. It can put the wearer into a digital environment of the project’s design, allowing them to experiment with architectural features and practice challenging tasks.
In other words, you can virtually walk through the entire project before breaking ground. Augmented reality could be the technology that solves the skilled labor shortage, bringing inexperienced hires up to speed more quickly than ever before.
8.Construction Management Software
Worksite communication was also a weakness in construction for a long time. Walkie-talkies were the primary devices, but now construction management software helps contractors and business owners keep track of everything on the site. It gives them another communication platform and makes it much easier for small tasks like payroll and schedule organization.
The Building Industry Needs Robotics
Adopting these technologies won’t be optional for much longer — building professionals need the help of robotics to address the industry's three main issues. The contractors who refuse to adapt will get left behind. Although many small businesses don’t feel ready to implement 3D printers, new software and other devices, they will need to take a calculated risk sometime soon.
Comments (0)
This post does not have any comments. Be the first to leave a comment below.
Featured Product
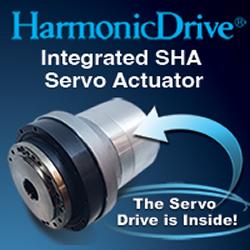