The Top 5 Things Every Manufacturing CIO Should Know
Responsible for numerous high level company decisions, the CIO’s direction has major impacts felt throughout an entire organization. To excel as a manufacturing CIO, one must clearly identify the company’s goals and always facilitate a deep understanding of how to streamline success.
Here are the top five things every manufacturing CIO should know.
1.Digital Transformation is Mandatory
There are constant disruptions in the manufacturing process. Whether it is delays in receiving components or a shift in customer needs, it’s the CIO’s job to have the foresight to manage and solve problems as they arise. To help combat frequent pain points, digital transformation strategies provide several benefits to organizations looking to bring their operations in line with the digital age.
Digital transformation helps increase operational speed and agility in the product development process. As market conditions evolve at breakneck speeds, CIO’s must remain flexible as workplaces and product strategies change. As an example, digital prototyping allows for 360-degree views of the factory like never before. This means maintenance issues can be addressed frequently, updates can be delivered to senior management in real-time, and tracking the product lifecycle becomes easier. This innovation is just one of the many areas manufacturing CIOs are investing in as they shift to digital first solutions. Long-established practices meant errors were prevalent in the product production process and infrequent check-ins resulted in a major loss of time and resources. Digital transformation increases efficiency and promotes better performance, allowing an organization to reach their goals in an accelerated way.
2.Eliminate Data Silos
During the manufacturing process, it’s important that all teams remain connected throughout the production chain. To ensure efficiency is top of mind, teams need to constantly communicate on product status, development, and hiccups so they can prepare for what’s next. Data silos emerge as a common problem in manufacturing communication which leads to limiting feedback and creating blind spots throughout different departments.
Oftentimes, data silos lead to missed opportunities that could hurt innovation and a company’s product roadmap. The sales team can tease new products to potential prospects by knowing what projects the product team is working on and the product team can benefit from the feedback the sales team is receiving from those using the product. With a single source of truth, the whole organization can communicate as updates come in to help each unit make more informed decisions. CIOs can use transformative tech focused on communication to help increase cross collaboration and speed up feedback.
3.The Importance of Ongoing Education
When making the shift to digital transformation, teams must have a full understanding of new technologies. This education does not end after simple training, as updates to software are constantly occurring. CIOs must ensure that team members are educated on new technologies on a constant basis by taking the time to connect with teams, facilitate ongoing forums, and be readily available whenever questions arise.
4.Connecting Hardware and Software Teams is Critical
In manufacturing, hardware and software teams work on different projects in the product lifecycle. For the final product to be optimal, both hardware and software teams must remain intertwined throughout the entire production process. If the hardware team makes a shift, the software team must know about it and remain agile, or risk not meeting deadlines and losing market share.
To bring the best product possible to market, hardware and software teams need a deep understanding of each other. Software shifts happen daily, meaning hardware may need to adapt at a moment's notice. As a CIO, it's imperative there exist ways to create open lines of communication between the two teams and that all updates are reported in real time.
5.Ensure the Organization Is Constantly Evolving
Part of a CIOs responsibility is to not only educate employees, but also take on the task of constantly educating oneself. Technology is rapidly evolving and updating as new solutions hit the market. It is important to be aware of these changes as they may provide even better offerings and solutions to organizations. To remain up to date, CIOs must garner a deep understanding of the industry, keep an eye on new features, and network with other professionals to see what they are taking on.
Keeping up with competitors is incredibly important. Knowing what is making other businesses thrive and others fail will help direct decision making and lead to more well thought out choices company wide.
Maziar Adl is the cofounder and CTO of Gocious, a cloud-based SaaS solution for strategic product planning.
Comments (0)
This post does not have any comments. Be the first to leave a comment below.
Featured Product
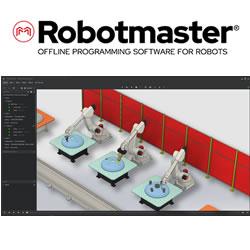