Running on fumes? AI isn't possible without proper data management
Since the release of ChatGPT-3 in November 2022, AI has dominated headlines worldwide. In manufacturing, interest in AI isn’t new—it certainly predates ChatGPT—but it has reached something of a fever pitch lately.
Of course, this is understandable. Any technology that promises to revolutionize how we work demands some attention. And if early indicators are correct, it seems that recent developments in AI fall into the rare category of making revolutionary claims and actually being revolutionary.
However, many manufacturers are in danger of putting the cart before the horse. Board members and C-suite executives are asking when AI pilot projects can begin, with a preference for a start date of yesterday.
Meanwhile, the plant floor reality is nowhere near ready for AI. In many cases, the data that is available for collection is incomplete or inaccurate. Their data collection is a mix of manual and messy, with data stuck siloed in systems that haven’t been updated in a decade. The worst part: with bad data, AI gives the illusion that it's working and may provide results and predictions that won't match the real world.
Generative AI in manufacturing
Recent developments in AI have primarily been in the field of generative AI, which refers to deep learning models that can produce outputs in a variety of formats such as text, imagery, and audio, based on the data it was trained on. Its most famous form is natural language processing, wherein models like ChatGPT are trained on text data and produce human-like responses to text queries.
However, that’s just scratching the surface. In manufacturing, one exciting use case of generative AI is that it creates opportunities to have conversations with your data. This will make data analysis far easier and allow for data-driven decision-making at scale. Furthermore, generative AI unlocks doorways to predictive maintenance, process optimization, and even developing new products. And we’re still in the early days.
Whether your use cases are for generative AI or other common AI use cases such as predictive maintenance, demand forecasting, or pricing, there are a few common steps needed for any AI project.
Laying the foundation for AI
Data is the fuel for AI. Enterprises worldwide are now realizing that the economic winners in the age of AI will be those with the best data. That’s why we’ve seen companies like Zoom trying to harvest data from video calls to train Large Language Models (LLMs). The more data a company has, the better positioned it will be to fine-tune AI models for their benefit.
In a similar way, manufacturers must realize that they fundamentally produce two things. On the one hand, they produce products—this is old news. On the other hand, they also produce data. And here’s the important point: the two are equally valuable.
However, to date, most manufacturers spend lots of time worrying about the quality of their traditional products and very little time worrying about the quality of their data. If they’re going to make the transition to the age of AI, they will need to get serious about their data.
This involves two primary areas: data collection and data management.
Data collection for AI
For the past decade, manufacturers have been bombarded with messages about the importance of data. And the good news is it’s now easier than ever to collect data. Most modern manufacturing equipment already captures data and makes it available via the network. For other data collection, the price of IIoT sensors has dropped dramatically, allowing even small to mid-size manufacturers that were previously priced out of such technology to begin collecting massive amounts of data.
While all data is not equally valuable, for manufacturers looking to pilot AI projects, the general rule of thumb is the more data you have, the better. That is, as long as you can manage it well.
Data management for AI
The next roadblock that many manufacturers hit after collecting data is failing to centralize this data. For instance, they may have loads of data in their historian, ERP, and MES, but as long as these systems are separated from one another, they’ll miss out on the full potential of the data. It’s a bit like having all the necessary ingredients for a soup but lacking a pot or any other way to combine the ingredients. So, rather than making a delicious meal, the unused ingredients grow moldy on the counter.
To solve this problem, manufacturers need to invest in modern data architecture. They’ll need to integrate disconnected data stacks and then store the data in a central repository, such as a data lake. By pulling all the data into a central location, manufacturers can ensure there is a target for their AI activities and not just a series of disconnected silos.
Before this data is ready to fuel AI programs, there’s another vital step to take: you must cleanse the data. As long as you have incomplete, duplicate, or incorrect data flowing through your systems, you won’t be able to take full advantage of AI. As the old saying goes: garbage in, garbage out. This is another area where the right data architecture is critical. A data lake that just stores all their raw data isn’t enough. Data needs to be processed and contextualized to make it useful for AI. An AI ready data architecture will include custom processing to cleanse and contextualize the data so your AI gets the right answers.
Preparing for a new future of manufacturing
We live in an exciting time for manufacturing. New technologies, like generative AI, are opening doors that many would have never previously imagined. Yet, much work still needs to be done to move these developments from the realm of keynote speeches to the factory floor. And to do that, manufacturers have to start with the vital work of getting data management right. Once they do that, they can begin to turn their attention to reimagining what’s possible with AI.
Comments (0)
This post does not have any comments. Be the first to leave a comment below.
Featured Product
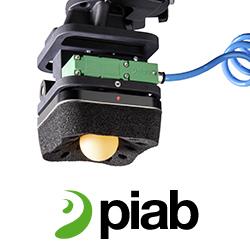