With the high number of SKUs, manual sorting capabilities had reached capacity, and Goodyear wanted to protect its workforce from the risk of injuries. It was also essential to have a Supply Chain Deployment strategy that offered real advantages to customers.
Bill Torrens | RMT Robotics
In manufacturing, the only thing as vital as the flow of product is the flow of information. Supply chain management is a critical component of doing business, and at The Goodyear Tire & Rubber Company, it's a priority. It's also one of the factors that made the company a global success story and North America's number one tire maker.
Paul Fledderjohann, Goodyear's Manager, Process Engineering, North America Tire (NAT) Supply Chain, is keenly aware of the distribution challenges. He is also well informed as to what tire manufacturing facilities are doing, not just to survive, but also to compete in an ever-evolving marketplace. It's a dilemma Goodyear faced in 2005 as it set its sights on improvements to the warehouse distribution system at the Goodyear facility in Fayetteville, North Carolina.
The Challenge
With a modernization project going on upstream from the warehouse, it was clear the Goodyear plant would require more than a retrofit for the current manual processes used for tire distribution. With the high number of SKUs, manual sorting capabilities had reached capacity, and Goodyear wanted to protect its workforce from the risk of injuries. It was also essential to have a Supply Chain Deployment strategy that offered real advantages to customers.
Since the expansion on the manufacturing side required half the existing warehouse space, Goodyear decided to build a new facility to handle tire storage and distribution. The challenge now was finding the right automation system, and the right provider to design and install it.
"It was a very strategic decision based on proposals received from the Bid Request and the supplier's past performance," said Fledderjohann. "We'd worked with RMT Robotics to build a fully-automated warehouse at the Goodyear plant in Lawton, Oklahoma, and we felt that solution would be a good system for Fayetteville."
In the last decade, Canada's RMT Robotics had established a solid track record with Goodyear, installing more than 30 robots at 6 of Goodyear's tire manufacturing facilities in North America. As the creator of large, high-velocity gantry robots and integrated systems, RMT understood the performance demands that Goodyear would require in Fayetteville.
The Concept
The challenge for Goodyear's NAT Supply Chain and RMT Robotics was to create a system for Fayetteville that could ship more tires directly to customers, and do it more accurately. As well, Goodyear wanted a system that could achieve payback very quickly.
The robotic distribution system that RMT proposed for the Goodyear plant featured 12 gantry robots working simultaneously to handle every aspect of warehouse distribution, from the time the product arrived from manufacturing, all the way through to sequential loading onto a trailer for customer delivery.
"The robotic gantry 'direct ship' solution is ideal in tire distribution," says Bill Torrens, Director Sales and Marketing at RMT Robotics. "In today's lean manufacturing and warehousing environment, it's a competitive advantage to have automation that can sort, temporarily stage, then ship tires directly to customers on demand. It not only reduces labor costs, it also keeps inventory levels low and customer response high."
RMT's 'direct ship' system was capable of managing the entire system inventory and had no difficulties coping with the demands of a high-SKU environment.
"There could be up to 1,000 different SKUs in one month," said Fledderjohann. “As well, the Fayetteville facility can produce 55,000 replacement tires per day. To stock, stage and ship them from a deployment standpoint is very, very difficult and manually intensive. Our new system does it all automatically, first by identifying each tire, and then remembering that identification as it stacks, sorts and deploys to customer requirements."
Torrens describes the 'direct ship' concept as palletizing avoidance. "Fed by final finish, the system maintains a large, dynamic picking inventory on the floor under the gantry, then ships it out in trailer loading sequence." He adds, "All of this without ever having seen a person, pallet or rack location. While the system is able to palletize to feed longer term storage, it's the high percentage that flows from final finish direct to trailer that makes the solution such a success."
In the fall of 2005, RMT Robotics was commissioned to begin the project. The work was completed in nine months, and after system optimization, Goodyear declared the installation phase completed in early May, 2006.
"It went even more smoothly than the Lawton installation," confirms Fledderjohann. "As a test, we processed about 30,000 tires per day for about a month and a half. When we finally went inside the gantry to do a physical count of the tires after processing 1.3 million tires, the discrepancy in inventory was basically nonexistent. That's very, very impressive."
The Future
Today, the robotic distribution system handles 100 percent of tire volume from the Fayetteville plant. The Goodyear Supply Chain Team confirms that, with a few modifications, the system is well suited to cope with any future production increases.
"I'm amazed at how well the technology is embraced," said Fledderjohann, referring to the pushback that sometimes occurs with the introduction of new technology. "This investment is good for the plant as well as for our customers."
Goodyear also recognizes the benefits to the supply chain that links customers with the Goodyear facility in Fayetteville. Now, with a fully-automated system that also offers timely, accurate information on every tire regardless of where it is in the warehouse and deployment cycle, it's a real competitive advantage.
Goodyear's NAT Supply Chain is confident the new Automated Warehouse Facility will make it more attractive for customers to receive tires from Goodyear. This technology allows Goodyear to fully integrate production related systems to supply chain systems. That means better customer fill rates, better deployment of product, and ultimately the ability to offer more attractive solutions.
It's the kind of payback that Goodyear is counting on, and it's also a ringing endorsement for RMT Robotics. "It's been a good company to work with," said Fledderjohann. "They've delivered on what they promised."
"From the beginning, Goodyear and RMT Robotics have shared a common vision for the future of tire distribution," says Douglas Pickard, President, RMT Robotics. "It has benefited both companies, and the pioneering spirit of the relationship has resulted in solutions that fundamentally re-define the tire distribution model."
For more information on Goodyear, visit www.goodyear.com. To learn more about RMT Robotics and its integrated solutions contact Bill Torrens, Director Sales & Marketing at billtorrens@rmtrobotics.com.
RMT Robotics
Founded in 1981 near Toronto, Canada, RMT Robotics has successfully designed and integrated over 200 systems in warehouses and distribution centres worldwide. Our specialty is the end-to-end integration of automated warehouse and distribution.
The content & opinions in this article are the author’s and do not necessarily represent the views of RoboticsTomorrow
Comments (0)
This post does not have any comments. Be the first to leave a comment below.
Featured Product
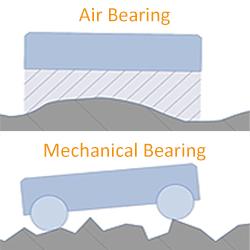