Space: the final frontier. These are the voyages of the starship "Enterprise". Its five-year mission: to explore strange new worlds, to seek out new life and new civilizations, to boldly go where no man has gone before. Do these words sound familiar? Well, today man has gone where no man has gone before. On the star ship Enterprise, there is a device known as a “replicator.” The concept was to have a 23rd century technology that could replicate anything by reconstituting raw material into the object desired.
Len Calderone
To science fiction writers this was just a dream, but if we look at most of our technology today, we first learned about these wondrous ideas from science fiction writers, such as Jules Verne. I remember reading about moving sidewalks and doors that automatically opened as you approached them when I was growing up. Today, we take this technology for granted.
Additive manufacturing takes virtual designs from CAD drawings or modeling software and transforms them into thin, virtual horizontal cross-sections and creates successive layers until the object is completed. In this process, the virtual object and the original item are almost identical.
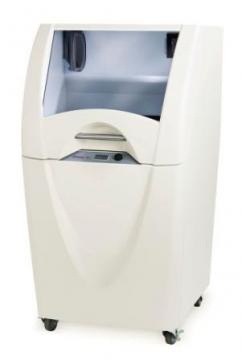
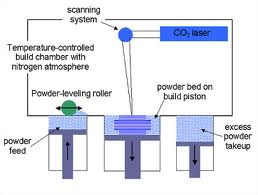
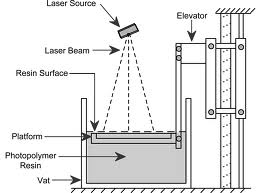
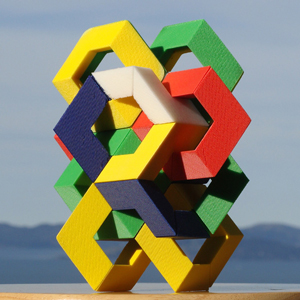
3D Systems’ products and services are utilized by a wide variety of industries; from automotive, aerospace and defense to Consumer Goods, architecture, medical and dental devices, plus numerous other industries for fast, precise design communication and prototyping as well as for the production of functional end-use parts.
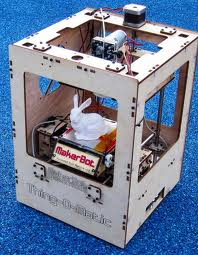
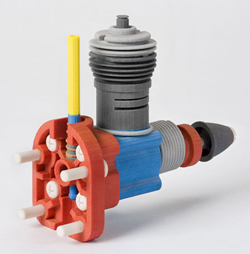
Because of 3D printing technology, we could see a return of overseas manufacturing to the U.S. Manufacturing will become incredibly cheap. In the future, we will see the manufacture of human replacement organs, glassware, toys and even house parts. Anything that can be conceived and converted by scanning or CAD drawings can be made.
The content & opinions in this article are the author’s and do not necessarily represent the views of RoboticsTomorrow
Comments (0)
This post does not have any comments. Be the first to leave a comment below.
Featured Product
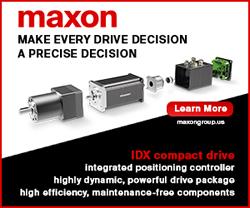