The Warehouse Group took to the Robotic Industrial Truck right away when they saw how it helped with their workload. On the manufacturing side, an unexpected secondary benefit is that we removed clutter and unsightly pallets from the work areas so the trucks can maneuver, providing a cleaner, safer work environment.
Contributed by | Seegrid
Case Study: YUSA Corporation
Washington Court House, OH
Customer Goals:
- Improve flow of raw material to assembly line
- Improve flow from assembly to warehouse
- Maintain service levels for customer shipments
Industry:
- Manufacturing (Automotive)
Key Activity:
- Finished goods delivery
Results:
- Reduced labor costs and immediate employee acceptance
- Safer work environment
- Re-assignment of employees to valueadded activities
- Reduced downtime, less maintenance and cost savings
The Challenge
YUSA Corporation maintains a highly focused effort to grow and satisfy their customer base. In this situation, they were looking for ways to gain efficiencies when moving raw materials to production and finished goods to the warehouse. By accomplishing these objectives, YUSA would improve service levels for customer shipments and increase customer satisfaction.
The Solution
YUSA Corporation was able to deploy the Seegrid ® Robotic Industrial Trucks with the following benefits:
- Ease-of-use, avoidance of training and costly maintenance practices
- Flexibility of route selection, familiarity with existing equipment types (forklifts and pallet jacks)
- Workforce acceptance, labor savings and general comfort working along manned equipment
The Results
Seegrid’s Robotic Industrial Trucks proved to be a perfect fit for YUSA and yielded substantial and immediate benefits, including:
- Reduced Labor Cost: Full-time employees were reassigned to value- added work activities
- Reduced Maintenance Costs: Employees can perform routine maintenance and trouble shooting
- No Facility Adaptation: The Robotic Industrial Trucks required no facility change and were set up in less than one hour
- Health & Safety: Less manual labor, controlled travel speeds and a system driven workflow that promotes consistent safe behavior
“The Warehouse Group took to the Robotic Industrial Truck right away when they saw how it helped with their workload. On the manufacturing side, an unexpected secondary benefit is that we removed clutter and unsightly pallets from the work areas so the trucks can maneuver, providing a cleaner, safer work environment. Additionally, two full-time material handling associates have been reassigned to areas where they can provide a greater impact to our manufacturing efforts.” - John Welling, Plant Manager, YUSA Corporation
The content & opinions in this article are the author’s and do not necessarily represent the views of RoboticsTomorrow
Comments (0)
This post does not have any comments. Be the first to leave a comment below.
Featured Product
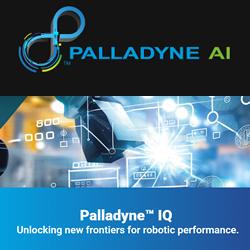