Concerns of robots maintaining tolerances and producing finish quality parts were put to rest by the live machining done at both booths.
Contributed by | RobotMaster
"Seeing is believing" was proven at Automatica 2012 in Munich at the Robotmaster booth and Kuka Robotics booth this year! Machining with robots is becoming a reality as visitors to the show were able to see 2 different types of live machining using robots with finish results that were eye openers! A wooden miniature Kuka robot model representative of the artistic and stone machining worlds was machined at the IPA/Fraunhofer booth and a bicycle component representative of the component manufacturing and growth market was machined at the Robotmaster booth!
Concerns of robots maintaining tolerances and producing finish quality parts were put to rest by the live machining done at both booths. Visitors were impressed by the results of both exhibits - achieving a high tolerance machined part and using a manufacturing robot cell to perform complex machining tasks in a single setup!
Kuka Robotics new control - the KRC4 with the KUKA.CNC motion planner allows an end-user from the CNC manufacturing world to transition from using regular CNC machines to using robots for machining by offering an easy to use interface while allowing them to visualize the machining code as NC/G-codes! The control processes the high speed machining data at the programmed speeds and machines the part similar to a CNC machine.
For the duration of the show, both booths (Robotmaster and IPA/Fraunhofer) had a steady stream of visitors stopping by, seeing how the robot was machining the part, checking the finished part and inquiring about the programming process. Those who had attempted to program robots before and understood the pains of attempting the same left the Robotmaster booth in amazement at the ease with which they could import or create a CAD model, generate the trajectories, resolve for common robotic issues, simulate the process and then generate the machining code using one integrated software solution - Robotmaster!
Visitors looking for low cost, high-end 5-axis (and more) machining solutions walked away convinced that they could now confidently invest in robots to achieve their machining tasks on their shop floors.
As Mr. Alexander Bay, responsible for Industrial Business Development for CNC / machining from Kuka Roboter GmbH put it, "What Robotmaster and KUKA mutually demonstrated at the Automatica fair is what many customers have been looking for a very long time!"
Unicam Software GmbH - a key reseller for Robotmaster who organized the booth was proud of the ultimate results produced by the show that every exhibitor strives for - "a thick binder full of quality leads!!!"
In addition to machining, Robotmaster easily supports path following robot applications such as trimming, welding, sanding, de-burring, painting/spraying, laser, plasma and water-jet cutting, grinding and part to tool applications. A 6-axis robot can easily be programmed using Robotmaster with support for external axes (up to 3 rails/tracks and 2 rotary axes) - all in simultaneous motion if desired!
Robotmaster is a product of Jabez Technologies based in Montreal, Canada. Intercam SA is the distributor of Robotmaster in Europe. For more information, email: info@robotmaster.com or visit our website: www.robotmaster.com
You can find the links of the videos of the robots milling at the Automatica 2012 event below:
The content & opinions in this article are the author’s and do not necessarily represent the views of RoboticsTomorrow
Comments (0)
This post does not have any comments. Be the first to leave a comment below.
Featured Product
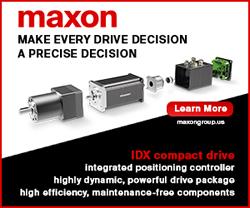