This article originated as a profile of one company as they began to robotically augment distribution centers. But, as I gathered information, the story has morphed into a review of why Kiva Systems' innovative methods - the goods-to-man methodology - is far superior to other older styles of fulfillment.
Frank Tobe | The Robot Report
Distribution centers (DCs) are massive warehouses that receive, inspect and store goods for later picking, packing and shipping to end-users, re-distributors or retail outlets. Products can be everything from books, pharmacy goods, clothing, office goods, food, drinks, shoes, produce, household items and pet supplies to diapers. And quantities can be one or two individual units to 20-100+ cases.
Driving the expansion and change in DCs are (1) online sales and consumer expectations of speedy delivery, (2) enhanced data manipulation capabilities, multidimensional processing and integration of new-tech mobile robotics into material handling, (3) proof that goods-to-man methods saves money, reduces labor and increases productivity, and (4) a current need to develop more cost-efficient centers (caused by delays and skittishness to make capital investments during the economic crisis). E-commerce sales are growing at an annual compounded growth rate of 8.5% - double that of supercenters, club and dollar stores. Supermarkets and convenience stores are growing as well. The quantity of materials that are moved daily through DCs is staggering as are the streams of data and algorithm considerations. [Source: Nielsen TDLinx & Nielsen Analytics]
The immensity and complexity of the supply process can be seen in this video showing how a Giant Eagle supermarket is resupplied from its regional distribution center:
Kiva Systems disrupted those metrics and increased worker productivity by reversing the man-to-goods process. This method brings the goods to the packer (goods-to-man). As Kiva's success became proven in the field, Amazon acquired Kiva for $775 million and is beginning to install Kiva systems in their new warehouses. It is estimated that the new Kiva metric for Amazon consumer goods is 600 items per hour.
These metrics translate into fewer employees and lower warehouse costs, which include not only the structure but the inside storage and material handling equipment as well. Steve Banker, a consultant at ARC Advisory Group, recently wrote in Logistics Viewpoints:
If you conduct a Google search on “Amazon distribution center,” you come across announcements over the past year for DCs in Virginia, New Jersey, and South Carolina. According to these articles, warehouses costing roughly $50-65 million will employ 1,500 to 2,000 workers.
But then I came across an article about a new Indiana DC. This DC is costing $150 million and the company is only promising 1,000 new workers. Could this be one of the new warehouses that will be using Kiva? The employment numbers seem to add up. This DC will employ at least one third fewer workers.
European DCs tend to be smaller than those in the US where massive centers for Wallmart and Amazon often exceed 1 million sq ft. Amazon has said that it will be filling its new 1 million sq ft distribution centers with Kiva robots. According to their financial reports, they are opening 12 new Kiva-equipped centers in 2012 with more planned for 2013. That is a lot of Kiva mobile robots, and this demand will surely keep them busy building and integrating those devices and their related software systems into Amazon's distribution scheme. In fact, Kiva has already laid off most of their sales and marketing staff but has increased their support staff to assist their new owner (and biggest client). As Amazon leads the consumer products industry to same day delivery, Kiva robots help give them that flexibility. [One-day turnaround isn't unique to Amazon; it is often a necessity. Think produce: vegetables, fruits, baked goods. These goods regularly move in and out of DCs within 24 hours.]
Kiva's acquisition by Amazon has created a void in innovative material handling technology just at the time when companies that had put off building or improving their DCs because of the economic crisis are now ready to invest again. Kiva's low cost for warehouse shelving and speed of installation in bare-boned facilities are far cheaper and faster than any other method offered.
However, Kiva-equipped distribution centers aren't the only methods available for handling robotic-assisted fulfillment. There are many new technologies as well as older-style methods now augmented with various robotics to handle the myriad types of warehoused goods. Amazon, Zappos and other consumer sales companies warehouse and ship small-quantity consumer items. Food distribution and intra-company distribution centers process on the case level. One east coast DC for a chain of groceries regularly processes 20 million cases per week. DCs not only focus on getting their goods in and out of the system but also concentrate on maximizing productivity and keeping their labor costs as low as possible.
Handling, distribution, transport and delivery - and the amortization of DC setup charges - often represent more cost than raw materials and manufacturing combined. Consequently, warehousing and material handling are a big business for hundreds of different types of companies: conveyors, rollers, racks, vision systems, hoists, shelving, electric motors, slides, barcode readers, printers, ladders, gantries, tugs, forklifts, autonomous lifts and tugs, skids, totes, carts, and software systems of all types, to name just a few. Big players in the field include Intelligrated, Egemin Automation, Fromm, Daifuku Webb, Adept, Frog AGV Systems, Seegrid, Fuji, Edict, Omega Lift, Nordock, Interlake Mecalux, Automated Packaging, Itoh Denki, etc. Most of these vendors augment the man-to-goods model.
There are three companies transitioning to offer goods-to-man functionality: Symbotic, Swisslog and Dematic. The latter two have been in the material handling business for quite some time and have introduced many new robotic solutions. Swisslog is publicly-traded (SLOG:SW); the other two are privately held. All three of these vendors emphasize maximizing warehouse density which can be seen by level upon level (multiple vertical rows) of floor to ceiling racks.
Symbotic
![]() |
Symbotic's Matrix Rover travels along shelf rows picking and restocking as required but can also operate autonomously on warehouse floors. |
Swisslog
Left to right: Swisslog's AutoStore drop-down rovers, Tornado lifts and SmartCarriers.
Swisslog builds modularized conveyors, stacker cranes, row rovers (called carriers) and autonomous tugs as well as their new AutoStore robots. Swisslog can handle open-case light goods and pallet/case systems. Swisslog provides European style material handling often characterized by high capital and operating costs and lots of mechanical devices. They enjoy very high productivity and space utilization in return.
Swisslog's new AutoStore rovers race along the top of modular aluminum storage racks which are located just below ceiling level. The rovers reach down to get bins of targeted goods which are vertically stacked on top of each other. Then they race to a lift/crane which drops the goods down and conveys them to pick and pack stations and/or pallets for shipment. Once the bins have been picked, they are returned to the stack in the same manner.
Swisslog, as its name implies, is European and as such, must always be able to handle unique existing space considerations, often having to adapt to some very unique building configurations. Swisslog claims that their methods maximizes both vertical and horizontal space enabling them to process up to 1,000 picks per hour.
Dematic
![]() |
Dematic goods-to-person shuttles are located at every level in all aisles and are serviced by high-speed elevators where material is lowered down to processing stations. |
Dematic, headquartered in Luxembourg, is an established European style provider and integrator of logistics and material handling solutions. They offer almost every type of storage solution imaginable and provide distribution and handling for B2B and B2C as well as grocery, apparel, food and beverage and general merchandise.
Software
As is the case in most robotics, smart software is critical to its success. Imagine the algorithms involved in resource allocation to determine which product goes in which bin; which order gets assigned to which station; which pod comes to which station; which robot should get which pod. Then compound that with the problems of integrating that solution into a SAP, IBM, Oracle, Manhattan Associates, or Red Prairie fulfillment system. Then add customized delivery optimization solutions (such as sequencing skids in a truck to delivery routes and sequencing the contents of skids to how they are offloaded in the store) to the mix and you have some really complex software packages.
All of the companies mentioned in this article (Amazon, Kiva, Symbotic, C&S, Dematic and Swisslog) blend techniques from AI, controls systems, machine learning, operations research and other software and engineering disciplines into their mobile robotic platform. All are focused on transforming fulfillment to the goods-to-man methodology because of the increased productivity gains and all are pioneering as they go because goods-to-man is new territory, software-wise.
Summary
This article originated as a profile of one company as they began to robotically augment distribution centers. But, as I gathered information, the story has morphed into a review of why Kiva Systems' innovative methods - the goods-to-man methodology - is far superior to other older styles of fulfillment. These older style man-to-goods methods are characterized by serious labor costs, heavy turnover, high cost shelving, conveyors, lifts, and transport and other systems to get targeted materials to a picker/packer or palletizing operation. Robotics, if used at all, is used to augment the worker's reach, mobility and lifting. The new-tech companies profiled above (Swisslog, Symbotic and Dematic) have begun to implement goods-to-man systems incorporating old and new style racks and shelving and all seem to be doing the same thing: building multi-layer shelving upon which rovers troll the levels and aisles picking their stuff and shuttling it off to an elevator which sends it via conveyors or otherwise to pick/pack or palletizing stations, all controlled by colossally-complex proprietary software.
Reprinted with permission from Everything Robotic.com
The content & opinions in this article are the author’s and do not necessarily represent the views of RoboticsTomorrow
Comments (0)
This post does not have any comments. Be the first to leave a comment below.
Featured Product
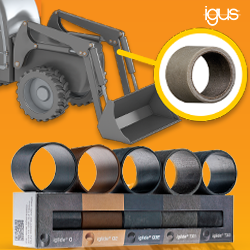