In this exciting competition, undergraduate and graduate students are invited to create a multi-disciplinary team to build a planetary rover prototype and demonstrate its capabilities to perform a series of competitive tasks in field tests at the NASA Johnson Space Centers Rock Yard in June 2013.
We were fortunate to be given the opportunity to show off some of the leading entries into the RASC-AL Exploration Robo-Ops Competition. Here are 5 of the design reports and some follup interviews with the team members:
West Virginia University - Interview
University of Nebraska-Lincoln - Interview
University of Utah - Interview
FAMU/FSU College of Engineering - Interview
Worcester Polytechnic Institute - Interview
Now at the midway point for the Robo-Ops competition how is your project coming along?
We had some initial delays in the availability of our funding, which caused us to delay the purchasing of the more costly components, specifically the mechanical parts of the rover. We made the best from the unexpected delay though and used the extra time to ensure that our mechanical design was as sound as possible. All mechanical and machined parts have been ordered and will arrive in the next couple of weeks. We have been making progress on the software and are excited for the rover to be assembled so we can test on the actual platform instead of just a simulator.
What adjustments or changes have you made from the original plan you submitted back in December?
The biggest change we have made is adding a 3-DOF wrist to our robotic arm, making it a 6-DOF arm. This will give us additional dexterity and increased manipulability. Our team has also grown in size since the proposal and now includes four additional undergraduate mechanical engineering students, Allison Miller, Effie Greene, Alex Adams, and Lukas Renker. In total we have four graduate and six undergraduate students on the team.
What were some of the challenges you have come across on the build thus far and how have you overcome them.?
One of the biggest challenges we have encountered has involved the wheels of the rover. The wheels are a very critical aspect of the rover. They are responsible for moving the rover from place to place and have several responsibilities they must fulfill. First, the wheel motors must be able to move and hold the weight of the rover without being overloaded and breaking. Second, the wheels must be able to maintain traction on the surface they are traveling over. Lastly, they must not add too much weight to the rover. We addressed the first aspect of holding the weight of the rover by correctly distributing the load of the rover off of the wheel motors and onto an aluminum tube through two ball bearings. The design we used will ensure that the motors can power the wheels of the rover without applying any axial or bending loads to the motor. For the traction aspect, we have built multiple wheel prototypes to test different tread methods and have tested them on different surfaces including sand, rocks, and compact ground. To keep the weight minimal, we have used light materials, and strategically removed material around the hubs of the wheels.
Cross section view of the ROCbot drive system.
How many man hours do you estimate your team has invested in the project so far?
I estimate over 1500 hours among the 10 team members since we started working on the initial design proposal in September.
What are some of major tasks still yet to come over the next couple months?
In the next couple of months we have to assemble our rover and performing testing and more software development. The user interface for our rover is incomplete at this time, and needs more work before it will be ready for the competition.
Can you tell us a bit about your team, how you recruited, how you organized and how you are working together?
Our team consists of graduate and undergraduate students in mechanical engineering. Although we are all mechanical engineers, we all work together in a interdisciplinary research lab where we develop miniature robots for minimally invasive surgery. This research has provided us with experience in electronics, software, and mechanical design that we are utilizing to develop our rover. Our team is organized in to four main areas: Rover Chassis, Robotic Arm, Cameras/Sensors, and Control Software. The four graduate students on our team take the lead in these areas and undergraduates work on specific tasks in these areas under the graduate student's leadership.
What facilities and equipment do you have at your disposal for the project?
We have access to a 3D printer and laser cutter that we are utilizing to make prototypes that help us iterate through design changes quickly. We also have access to a miniature mill and lathe that we can use to make small non-critical parts for our rover. The College of Engineering also has a staffed machine shop that student organizations can have parts machined for the cost of the material.
Do you have any advice for future contenders in this type of competition?
I advise future contenders to start early. There are many different aspects to this project that all take a considerable amount of time to do correctly.
The content & opinions in this article are the author’s and do not necessarily represent the views of RoboticsTomorrow
Comments (0)
This post does not have any comments. Be the first to leave a comment below.
Featured Product
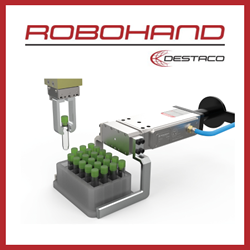