The goal is to completely automate the brake press to bend a variety of different parts.
Contributed by | Midwest Engineering Systems Inc.
Midwest Engineering Systems Inc. (MWES) provided a Robotic Brake Press Tending System to automate the metal part bending process of a Bystronics Brake Press for a metal fabricator. The goal is to completely automate the brake press to bend a variety of different parts.
The Challenge:
-
Must be capable of handling as many different parts as possible.
-
Some parts need to be bent in more than one location.
-
Ability to automatically change tooling.
-
Part weights were upwards of 500+ lbs.
-
Our customer provides product to the automotive and military industries and must maintain high quality standards on shipped finished goods as well as throughout the manufacturing process.
During the proposal stage, MWES performed a thorough evaluation of the current situation to provide a solution option. In order to achieve all of the project’s goals, multiple solution options were analyzed before a final path was chosen.
The Solution:
After a review of existing specifications, process data, programs, and interviews with the engineering team, production managers and machine operations, MWES was able to execute a successful solution to our customer. The comprehensive solution included:
-
ABB Robot System
-
Three Robot EOAT’s with Tool Change
-
Capable to handling many parts
-
Automatic tool changer/swivel unit
-
Vacuum/Magnetic Gripers to handle parts
-
-
BendWare Robot programming software
-
Part squaring table to justify the sheet metal blanks to be formed
-
Part re-grip station
-
Used to re-grip parts between bending cycles
-
Vacuum or magnetic grippers
-
Part present sensors
-
In feed and out feed station including guides and sensors
-
Implemented robot safety equipment, which meets ANSI/RIA standards for robot cell safety.
-
Allows communication with brake press system
-
Discreet electrical interface connected to robot via Ethernet
-
Electrical Enclosure with electrical panels and brake press control interface
-
Electrical & Mechanical Installation and on-site operator training at customer facility.
-
On-site operator training at customer facility
Impact To the Customer:
The final solution added new features and capabilities to the press brake process. Some key enhancements are:
-
Increased productivity. Machine can run 24/7
-
Improved worker safety by taking operators out of extremely heavy lifting situations
-
Improved quality variance of finished parts
-
Easy to operate user interface
About Midwest Engineering Systems Inc.
Midwest Engineering Systems Inc., an innovator and leader in complex systems integration, has been providing custom design and automation solutions for over 20 years. A company dedicated to customer satisfaction and successful solutions, MWES continues to expand its capabilities and has become a valued supplier to many loyal customers. MWES technical expertise includes a vast knowledge base serving customers in many industries including:
Engine and Transmission Assembly, Heavy Equipment Machining & Assembly, Robotic Integration, Consumer Goods, Medical Products, Web Handling Systems, Custom Coordinated Drive Systems
The content & opinions in this article are the author’s and do not necessarily represent the views of RoboticsTomorrow
Comments (0)
This post does not have any comments. Be the first to leave a comment below.
Featured Product
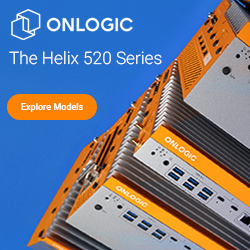