Ethernet cabling has been standardized. The cables for an Ethernet-enabled Auto ID reader are common with all standard Ethernet equipment.
Six Advantages of Ethernet for Auto ID Readers
Contributed by | Microscan Systems, Inc.
Connecting an Auto ID reader to a manufacturing system is a simple task but the options for connectivity are increasing all the time. The industrial standard is still the RS-232 serial connection, which dates back 50 years to the first computers. The first widely accepted version of Universal Serial Bus (USB) was introduced in 1998, yet was not generally adopted in industrial applications until very recently. The late 1990s also saw some of the first Ethernet networks deployed in manufacturing environments for connecting PCs, test systems, control systems, and other devices, and integrated into manufacturing execution systems (MES) and enterprise resource planning (ERP) systems.
Process engineers have many choices for automated data acquisition and data transmission technology − most commonly the three options mentioned above. Ethernet is not always the best choice, and the other technologies have their place – for example, the low cost and compatibility of adding serial Auto ID readers into an existing non-networked system. However, the list of advantages for deploying a network-based system is very compelling:
1. Unlimited number of connections to a host PC;
2. Unlimited distance to a host PC;
3. Standardized cables;
4. Faster data transmission speeds;
5. Easy integration into MES and ERP systems;
6. Remote device management.
Unlimited Connections to Host
An RS-232 serial interface is still a great way to connect a data capture device like a barcode reader to a local PC. While this connection is slow by current standards, the data content of a 1D barcode or even a 2D Data Matrix is fairly small and the transmission speed is more than sufficient, even for high-speed applications. However, as this serial interface is a declining technology, new computers rarely offer multiple or even single serial ports. Serial ports may be added, but systems become complicated and expensive as more and more ports are needed.
USB connectivity is much faster than serial, and most PCs have one or more USB ports. However, these ports are in high demand in industrial applications and running out of USB ports is a common problem.
Ethernet communication has developed into the most common method of data transmission technology. Every modern computer has a network interface card (NIC) and nearly every workplace has an Ethernet network. One NIC can connect to a nearly unlimited number of Ethernet devices. Unlike serial or USB, each connection is independently addressable to allow deployment specificity. Ethernet networks commonly use the TCP/IP protocol suite; EtherNet/IP is an industrial protocol that augments Ethernet networks for work with PLCs and industrial control systems.
By using network-based Ethernet communication, traceability data can be collected at more points throughout the manufacturing process, which allows more tasks to be performed in parallel and improves productivity, reduces cycle time, and ultimately minimizes manufacturing costs.
Unlimited Distance to Host
A standard RS-232 connection at low power and low data transmission rates (9.6 kb) can use a cable up to 50 feet long. Shorter cables must be used for higher data transmission rates. A full-speed 115 kb connection limits the cable to 10 feet. USB communication is limited to 15-foot cables.
An Ethernet interface can span a much longer distance at much higher data rates, if needed. Also, since it is network-based and not a point-to-point connection, the cable only needs to extend to the nearest Ethernet hub. From there the hub can communicate to any device on the network, and distance becomes irrelevant.
There is no longer any reason to have a PC on a manufacturing floor. If every input device communicating to a control system is on a network, computers can be removed from the floor and co-located with other systems in a controlled environment for improved reliability, maintenance access, and planning.
Common Cabling
Ethernet cabling has been standardized. The cables for an Ethernet-enabled Auto ID reader are common with all standard Ethernet equipment. For highly flexible manufacturing cells this capability means less time locating compatible cables and less money invested in stocks of proprietary accessories that work with only certain devices. Connections are also simplified, which reduces the need for expensive communication protocol conversion accessories.
Faster Data Connection
While the data content of a 1D barcode or 2D Data Matrix is minimal and easy to transmit over a slower connection such as RS- 232, more advanced barcode readers offer many more capabilities that require higher bandwidth than a serial connection can offer.
One common data-intensive task is the recording of no-read images. Barcode readers such as Microscan’s QX Hawk capture a high-resolution image of every item they read. Most are discarded as soon as the data is successfully read. When data cannot be extracted, users may wish to save the image file for offline diagnostics. This information can be valuable in developing process improvements such as identifying how codes are being damaged or misprinted, or finding the cause of product orientation deviations. In some cases, the images can also be used to recover costs from suppliers whose barcodes or marks are illegible. An Ethernet interface can easily transmit these images for storage over a high-speed connection without impacting the production process.
Compatible with MES and ERP Systems
Manufacturing execution systems (such as those from Agilent or Cogiscan) and ERP systems (such as SAP and Oracle) are network-based and communicate over Ethernet. They are designed to work with data sources of all types, and the integration of an Ethernet-enabled Auto ID reader is a simple matter that does not require a terminal or workstation at the collection point. Serial and USB devices may still be integrated into these systems but the extra steps, equipment, and costs required can be prohibitive.
Remote Device Management
Remote operation of data capture devices allows new ways to collect data and control manufacturing processes. Without the need for a PC operating in proximity to a data collection point, it becomes feasible and economical to collect data in new places. Work cells become much more agile and can be set up anywhere there is a network connection.
Remote access of Ethernet devices also allows process engineers to set up and troubleshoot their MES without leaving their offices. With such access to barcode reader settings and acquired images, problems can be diagnosed quickly in the office and communicated to the shop floor for correction by technicians. Rapid product changeovers are also easily accomplished, resulting in less downtime and greater flexibility.
Ethernet Solutions from Microscan
Microscan offers a variety of barcode readers with integrated Ethernet capability, including the MINI Hawk Xi and QX Hawk. The MINI Hawk Xi is the smallest Ethernet-ready barcode reader available, a powerful tool for reading 1D and 2D barcodes. It includes Microscan’s X-Mode decoding algorithms for direct part marks (DPM), and is available with a high-speed sensor and global shutter for packaging or other dynamic applications. High-density optics are available that can read Data Matrix symbols as small as 3.3 mil.
The QX Hawk, which features integrated liquid lens autofocus, is the first high-performance imager to have the full flexibility to read any mark at any distance, at any speed, and in any environment. In addition to X-Mode algorithms, the QX Hawk offers a high-resolution modular optical zoom system, eliminating the need for automation engineers to research multiple configuration options before deployment. Ethernet TCP/IP and EtherNet/IP protocols are both supported by the QX Hawk.
Both products are designed for rugged industrial environments, manufactured of tough alloy materials and sealed against dust and water ingress. Both products use Microscan’s ESP® software for easy setup and remote access of any reader on the network, and feature built-in illumination that eliminates the need for external lighting in most applications.
About Microscan
Microscan actively supports both technologies and strives to address customer applications appropriately and without bias. We continue to develop innovative solutions using both lasers and imaging for barcode applications as we expand our growing portfolio of machine vision systems, machine vision lighting, software, and hardware solutions.
The content & opinions in this article are the author’s and do not necessarily represent the views of RoboticsTomorrow
Comments (0)
This post does not have any comments. Be the first to leave a comment below.
Featured Product
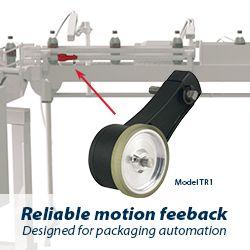