These drones are solely surveyors. They must be well equipped to notice when something is out of place or detect potential threats and weapons and alert park rangers immediately.
Alyssa Parkinson | Solid Concepts
What technological obstacles or advancements do these drones look to overcome?
One of the biggest obstacles is software and flight time. These drones are solely surveyors. They must be well equipped to notice when something is out of place or detect potential threats and weapons and alert park rangers immediately. Poaching is a real time issue and we need immediate, real time responses. All data analysis must happen onboard the drone without any live streaming. The second desired advancement is in air time itself. We need these drones to fly for upwards of say ten hours, or during the night when poaching is typically heaviest, and to run on energy resources other than gas. Fuel is not readily available in these areas and isn’t cheap; the UAVs will be out in rough terrain. These drones must find a way to run for long hours and be easily assembled and maneuvered by anyone as the end hope is to provide advanced UAVs that might be adopted in some form by the park rangers.
What will their agency be in the parks, or the hoped for agency?
The hope is that UAVs will be trustworthy park surveyors in the near future and that this challenge will boost the speed at which affordable, intelligent drones become available to rangers. What these parks need is a map of the territory documenting animal behaviors and poaching patterns to help best predict where rangers need to be when in order to best prevent animal poaching. Above all, raising awareness and rallying people to do something about the problem is a huge factor in this challenge.
How will 3D Printing be incorporated into the building of these drones?
The challenge is really reaching out to hobbyists and engineering students and asking them to use anything at their disposal to create something new and open source to aid in the protection of a very fragile ecosystem. 3D Printing is already a huge player in the realm of open source activity. Our hope at Solid Concepts is to educate the challengers in what 3D Printing is capable of (particularly industrial strength 3D Printers), show teams the ways 3D Printing has been used in many UAV applications already, and provide a manufacturing technology that can be used for one-offs without breaking the bank. Our aerospace customers repeat time and again how 3D Printing really helped simplify what would’ve been a costly and complicated component to machine. Solid Concepts has also donated funds towards the final winning prize money; we’re very serious about raising awareness and solutions.
Why 3D printing rather than more conventional manufacturing methods?
Of course teams are encouraged to use any method of manufacturing, but the fastest and most cost effective way to produce prototypes and working models is with 3D Printing. 3D Printing allows for one-offs, no overhead tooling costs and no cost for complexity. 3D Printing is a cost effective way to product molds, ailerons, electronics sleds, avionics housings and is very durable and – most importantly – light. The complexity 3D Printing affords includes consolidating numerous parts, thereby eliminating attachment features and fixtures that add weight and bulk. Weight is always a concern with things that fly!
What software will these drones incorporate to best survey the parks?
This is the fun part: The teams are being encouraged to develop their own software and programming for these drones. How will drones respond to the environment, how will they identify foreign objects, how will they steer themselves? The teams must answer these questions and develop ways for the drone to essentially operate on its own – that’s the hope at least. There’s definitely control systems already out there and available; this is about leaving an open door to creativity.
What sparked the involvement of this group to stop animal poaching?
Solid Concepts was approached at an UAV conference by Princess Aliyah Pandolfi in the early summer, 2013. We were showcasing an underwater remotely operated vehicle that uses a missile control system to steer itself. When we heard Aliyah’s vision we were very excited: Here was a chance for us to participate in something bigger than us, something that just doesn’t get the attention it deserves even though for decades now warnings about the extinction of rhinos have been prevalent. Rhino horns are composed of keratin, which is found in human fingernails and hair, and yet in certain cultures the horn is believed to withhold some magical healing power. Perhaps the most important step is educating these cultures in the truth about rhino horn composition; however, there’s no one answer to the problem, and surveillance to help prevention is definitely key.
What communities or industries has this challenge reached out to?
Princess Aliyah Pandolfi has reached out to scientists, mathematicians, hobbyists in the Maker community, private wildlife parks and more and we are thrilled to see the response and collaboration between so many diverse groups with each a unique set of skills and expertise.
Do you see any other similar applications for drones arising in the near future?
Drones kind of have bad reputations, probably from the odd science fiction movie depicting them as world dominators. Using them in a fashion like this, to map territories and draw important patterns to develop strategies for prevention and protection, can fall into all kinds of fields and do really wonderful things. Discovering and mapping ecosystems to document the changes from people or other factors; in times of disaster, mapping out where need is heaviest or finding resources; the possibilities and infinite.
Please tell us a bit about Solid Concepts and the 3D printing industry. Who are you, what do you do and where is the industry headed in the future?
Solid Concepts was founded in 1991. We began as a rapid prototyping service provider with a few Stereolithography (SLA) 3D Printing and CNC machining systems. We’ve expanded into seven facilities and now house over 130 3D Printing, machining, injection molding and cast urethane systems as well as auto rated paint booths. We now provide prototyping and production solutions to the aerospace, medical, entertainment industries and more. 3D Printing was a huge part of our founding and remains a staple in our manufacturing options. We’ve watched the industry grow and have attributed advancements and new developments ourselves, such as ID-Light which is a process that 3D Prints incredibly light parts with beautiful surfaces. One of the biggest attributes that we’re excited about is the complexity 3D Printing offers and the inherent customization without additional costs. This technology produces some very beautiful and also practical products, and has allowed us to help our customers achieve success.
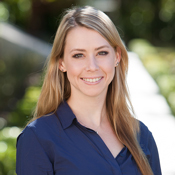
About Alyssa Parkinson
Alyssa Parkinson is a technical writer and technology journalist for Solid Concepts and runs the company blog. She covers shifts in the custom manufacturing industry, relays Solid Concepts’ solutions to the public, and is published in multiple engineering, manufacturing, design and science publications. Specialty areas include aerospace and the unmanned systems industries.
About Solid Concepts Inc.
Solid Concepts’ custom manufacturing solutions accelerate product development and production efforts for aerospace, medical, industrial design, business consumer industries and more. Since 1991, Solid Concepts has grown to a 7 facility company employing over 400 people nationwide. Solid Concepts employees enjoy a full range of benefits while working in clean, safe and friendly facilities. Solid Concepts manufacturing technologies include PolyJet, 3D Color Prints, Stereolithography (SLA), Selective and Direct Metal Laser Sintering (SLS, DMLS), Fused Deposition Modeling (FDM), CNC Machining, Advanced Cast Urethanes, Tooling and Injection Molding as well as a professional finishing department.
The content & opinions in this article are the author’s and do not necessarily represent the views of RoboticsTomorrow
Comments (0)
This post does not have any comments. Be the first to leave a comment below.
Featured Product
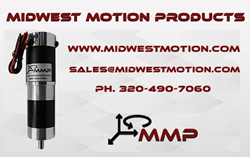
Midwest Motion Products is a leading provider of robust and reliable Motion Control Products.
MMP specializes in supplying high-quality Brushed & Brushless DC Motors & Gearmotors for Robotics and Automation Equipment with a wide range of motor windings and gear ratios. With an impressive track record of more than 8,000 released DC Gearmotors designs and over 2,000,000 individual part numbers, we are renowned for our ability to handle large-scale orders. Due to our huge on-hand inventory, we are also well known for lightning-fast delivery of our standard products. We take pride in our dedicated customer service and our team of knowledgeable sales and engineering experts who are ready to assist you with custom design solutions tailored to your specific application. Additionally, we also offer a wide range of complimentary products, such as DC Motor Controls, DC Linear Actuators, AC-DC power Supplies, and DC Servo Amplifiers and others.