Multi-axis, three-dimensional cable carriers for palletizing.
Joseph Ciringione | igus
Cable management is a crucial part of any robotic system, but the truth is that the methods used to attach and guide cables has not changed much in the past 50-plus years. In fact, it is often overlooked altogether. While managing cables and hoses may seem simple, most experts agree one of the biggest oversights designers make is underestimating cable-management issues. Many robot manufacturers are now choosing multi-axis, three-dimensional cable management systems specially designed for complex moving applications in order to minimize downtime and extend the service life of cables and hoses.
Trans Nova RUF offers services from planning and design, to manufacturing, installation and commissioning solutions for the packaging and palletizing industries. The product range includes compact machines for top- and side-loading, picker systems for fast pick-and-place applications and robotic systems for picking, palletizing and de-palletizing tasks.
"We are able to handle any type of primary packaging," explained Michael Ruf, manager and deputy general manager, Trans Nova RUF. "Whether food / non-food areas, medical or pharmaceutical engineering, [we] offer flexible packaging solutions for any industry. The company is growing in double digits every year."
The turnkey palletizing robot comes mounted with a compact, universal Triflex RS module. It is mounted on existing mounting points on the robot and consists of a multi-axis energy supply, integrated spring bars as well as a cover for extra protection.
To increase the performance of its robots and continue to grow their customer base, Trans Nova RUF needed to improve the cable management system used on its robots. The system needed to perform for the life of the machine, while at the same time moving easily around multiple axis and operating safely even in tight, limited spaces. The corrugated tubing the company was using to protect the cables and hoses could not withstand the rotational movements performed by the robots and as a result was failing and causing expensive downtime.
The robot’s power supply lines can be easily replaced.
Trans Nova RUF now uses Triflex® RS from igus®, a compact, ready-to-install assembly that is mounted to installation points available on the robot. The module is ideal for the company's turnkey film-packaging robot because of the extremely low installation space and the integrated fiber rods. The fiber rods enable safe implementation of the cable carrier system on the robot's wrist without cable stress. Customers of Trans Nova RUF benefit from the increased durability and safety the assembly provides.
The Triflex RS system is mounted to several points on the robot. It uses E-Z Triflex, a cable carrier that features multi-dimensional movement and easy cable installation from the top or bottom through an opening along the length of the cable carrier. There are also built-in spring bars for safe cable and hose guidance and a specialized cover system to maintain the power supply when the robot operates vertically or upside down.
The additional stop provides even more stability. The bending radius and exposure is increased four times using igus’ Triflex RS module.
Picture perfect packaging for every roll of film
The film packaging plant is more than 65 yards long and houses a total of nine Trans Nova RUF robots. Each roll of film is made to custom order and can vary in length and / or thickness, which can create a number of packaging challenges. Also, the film material used is not always the same. Different types of film run simultaneously into the packaging system and must be handled appropriately according to the production orders. These factors make the application ideal for robot technology, according to Ruf.
The packaging process involves the following steps: after preparation, rolls of film and cardboard are placed into the unit and stored in a buffer / sorting station before they are inserted into a film tube for protection. The tubular bag supernatant is injected into the core using compressed air. Then the roll of film is placed into a final container and packaged individually into a cardboard box, labeled and sealed. Finally, the boxes are palletized by a separate robot onto two different pallets where a head-stretch coil secures the two respective pallet containers.
"The packaging plant [operates] around the clock, seven days a week," explained Ruf. "The respective package weight is between four and 132 pounds and the conveyor speed is 131 feet per minute. Twenty rolls can be packaged per minute."
Components for multi-dimensional portable power supply.
Cable carriers replace corrugated tubing
Trans Nova RUF chose the Triflex RS system for its longevity and high mechanical capacity for protecting cables. Specifically in axes three through six of the robot there is an extremely strong rotating motion. The corrugated tubing formerly being used could not rotate around its own axis and with the added torsion, there was a danger the tubing would tear and breakdown into the components of the robot. This would potentially cause the entire system to stop and permanently damage the line.
The high-performance, multi-axis Triflex RS system is an ideal replacement because it is capable of torsional movement and high flexibility. The cable carrier can achieve a rotation of approximately plus or minus 10 degrees for each chain link in the longitudinal axis. Unlike the corrugated tubing it also has a fixed bending radius, which prevents damage to the cables and hoses. It also features a two-chamber interior to ensure a clean layout where the bus and compressed-air lines can be installed separately.
The benefits go even further. The energy supply system consists of single-piece, interlinked units. The one-piece links are connected to each other with a "ball/cup" connection also known as the "trailer-hitch principle". This principle combines the ability to absorb high tensile strengths with the option to shorten or lengthen the cable carrier at any point. This is a huge benefit when compared to other cable management systems available on the market, which traditionally feature individual elements connected by wire that cannot be easily altered. In addition, the unique one-piece design provides excellent protection for the cables against impacts and abrasion on the robotic arm and is also resistant against dirt, hot chips and various liquids.
"Our experience [with igus] has been positive. They were able to convince us that the plastic chain remains dimensionally stable under all circumstances," explained Ruf. "That way we can ensure a high level of functionality and because the requirements are constantly increasing, a long-term cooperation [between Trans Nova RUF and igus] is possible."
igus® develops products based on a belief in making functionally advanced, yet affordable plastic components and assemblies, including Energy Chain ® cable carriers, Chainflex ® continuous flex cables, and Triflex ® robotic cable carrier systems. No maintenance, lower costs, longer life cycles – these key principles apply to all igus ® products, systems and services. Tried and tested in terms of durability, friction properties and stability, igus ® plastics are the technological core of the company’s range.
The content & opinions in this article are the author’s and do not necessarily represent the views of RoboticsTomorrow
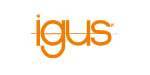
igus
The mission of igus® is to use its innovative polymer materials to develop products that provide creative solutions and exceed our customers' expectations while delivering fast, accurate service.
Other Articles
Automate 2025 Q&A with igus
Low-Cost Robotics Elevate Industrial Inspection Processes
7 Cable Management Mistakes to Avoid
More about igus
Comments (0)
This post does not have any comments. Be the first to leave a comment below.
Featured Product
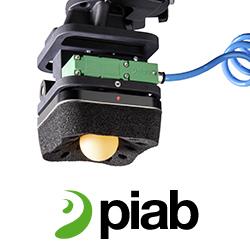