The HV-100s are equipped with several options to re-space a field depending upon a growers needs.
Contributed by | Harvest Automation
In the US Nursery and Greenhouse industry, the onset of warmer weather marks the beginning of the big sales season, which typically peaks at Mother's day and begins a slow decline throughout the summer months and into fall. Depending upon the latitude some growers will begin shipping product in mid- to late-March, for others shipping won't start until April. Nonetheless once shipping begins, pickers are trained to pick the best plants from a field and the result invariably is a field with a large percentage of plants gone. The remaining plants will still need water, but now half the water is simply going into the ground rather than the pot. The space that those plants occupy could be put to more efficient use.
On a traditional Nursery a grower would have to pay workers an hourly wage to re-space plants to one end of a field. Pulling workers from valuable shipping operations to re-space a field during the busiest time of the year is typically a non-starter. With robots however the equation changes. The Harvest Automation HV-100 is a grower's dedicated plant moving workforce. No longer do growers have to sacrifice the opportunity to free up valuable space to get an order out the door on time. Robots make available the option to do both. The HV-100s are equipped with several options to re-space a field depending upon a growers needs.
Standard Consolidation:
The standard Consolidation mode will simply allow a grower to re-space plants from one end to the other into a consistent consolidated block. This mode gives a grower the capability to completely clear one end of a field to make space for new plants.
Gaps Mode:
Gaps mode allows the robot to re-space plants into discrete blocks distributed along the field. This mode enables greater plant moving throughput than the standard mode. A grower can then insert new plants into the spaces between plant blocks or can selectively turn off every other sprinkler to conserve water.
Collection with Gaps Mode:
Using the Collection with Gaps mode the robot can collect a sparsely populated field to can-tight loads separated by gaps that can then be moved (with bedding forks) and re-spaced into a new field. This workflow allows several picked over fields to be consolidated into a single field, leaving one or more fields completely empty and ready for new plants.
Pots Across Mode:
In Pots Across mode the HV-100 will move pots scattered over a wide bed up to the edge of the bed, while also maintaining a high throughput. It will do this by varying the number of pots across the bed, so that there are no gaps along the edge. The value of Pots Across mode is that plants on one edge of the bed are easy to access by the plant pickers, saving walking time for pickers and enabling a better assessment of readiness for sale.
With a consolidated field pickers have easier and better access to mature plants for shipping and growers have fields open and ready for new plants. More work is completed, more fields are opened up for new plants and fewer resources are consumed - More for Less. For operations large and small the HV-100 makes sense for any Nursery and Greenhouse. Getting quality work done when it's needed most.
Try the HV-100 for free! Harvest Automation will bring robots to your operation and for multiple days to move plants. Seeing is believing. Click here to sign up!
The content & opinions in this article are the author’s and do not necessarily represent the views of RoboticsTomorrow
Comments (0)
This post does not have any comments. Be the first to leave a comment below.
Featured Product
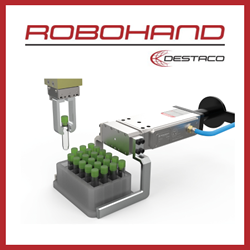