The design and construction of the RobLog Industrial Demonstrator was made under the requirements for such a machine to be robust yet have a streamlined design, flexible enough to fit into different space confinements, such as loading docks or warehouses.
Teresa Rittel | RobLog
An automated unloading solution for heavy sack-shaped goods debuted in Hannover, Germany at the 2014 CeMAT trade show with the unveiling of the RobLog Industrial Demonstrator. RobLog, a combination for Robotic Logistics, is an EU-funded project that is developing two autonomous demonstrators: an industrial one (capable of automating the unloading of heavy sack-shaped goods from containers), and an advanced one developed for further research. The onsite presence of the Industrial Demonstrator at the trade show attracted a lot of attention from visitors seeking unloading solutions for an array of heavy sack-shaped goods. Principals of companies exploring options for an automated method for unloading of such goods were quick to see the RobLog Industrial Demonstrator‘s potential unloading implementation. The onsite demonstration featured full coffee sacks; however the design of the demonstrator could also be used to resolve current manual unloading issues for: soil, sand, flour, sugar, and rice.
The design and construction of the RobLog Industrial Demonstrator was made under the requirements for such a machine to be robust yet have a streamlined design, flexible enough to fit into different space confinements, such as loading docks or warehouses. Flexibility being a goal, the head of the unit was designed with the ability to independently move up and down and also rotate 30 degrees in either direction from the main body via the rotating axis. This feature enables more dexterity of the machine, again making it suitable to operate in constricted places. The tilting hydraulic body was reinforced with a 50mm parallel rod, enabling the head to support up to 70kg. At the end of the head, is the patented and affixed gripping system, the Needle Chain, which features a constant contact unit comprised of six (6) chains with 15mm needles attached to every 4th chain link. The use of chains instead of a roller in front of the gripper and a transition conveyor offers continuous flow of the unloading material and assures that the needles stay in contact with the sack during the whole grasping process. This design eliminates any transition that may compromise the grasping of the sack.
The efficiency of the RobLog Industrial Demonstrator is being tested and compiled with real cycle times and will be published once aggregated. These cycle times will be used to estimate the implementation of such a machine to perform automated unloading activities. Further efficiencies offered by the machine are those that relate to preventative measures, such as reduced onsite employee injuries.
For more information, please contact Teresa.Rittel@reutlingen-university.de
About RobLog
RobLog is funded from the European Union‘s Seventh Framework Programme for research, technological development and demonstration under grand agreement no. 270350. It is an Integrated Project (IP) in the area ‘‘Cognitive Systems and Robotics.‘‘ The project duration is four years, begining in January of 2011 and will end in January of 2015. The total budget is 7.6 million Euro with a funding of 5.59 million Euro.
The content & opinions in this article are the author’s and do not necessarily represent the views of RoboticsTomorrow
Comments (0)
This post does not have any comments. Be the first to leave a comment below.
Featured Product
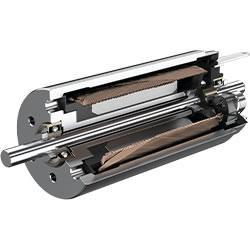