This is an example of high speed milling of a soft foam statue into a sculpture using Robotmaster and a KUKA Robot. The 7-axis robot allows accurate cutting from all angles.
Video - Milling a Statue out of Soft Foam
Contributed by | Robotmaster
For more information, please visit: http://www.robotmaster.com
The content & opinions in this article are the author’s and do not necessarily represent the views of RoboticsTomorrow
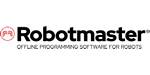
Robotmaster
Robotmaster, a Hypertherm Associates brand, is an offline, is an offline robot programming software that helps manufacturers maximize their robot's productivity with easy and efficient robot programming for a variety of applications such as cutting, trimming, milling, welding, spraying, polishing, sanding, grinding, deburring, and more. Robotmaster uses integrated CAD/CAM functionality to make robotic programming easy and intuitive for everyone, even first-time users.
Other Articles
Have You Looked at Automating Fabrication Tasks in the Past? Why Didn’t You?
Trane® Saves Over 80 Hours of Robot Programming Time
3 Benefits of Working With a Robotic Integrator
More about Robotmaster
Comments (0)
This post does not have any comments. Be the first to leave a comment below.
Featured Product
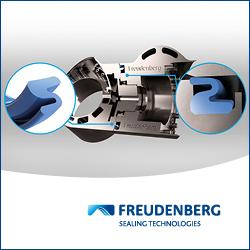