By continuing to add more computing capabilities for AI on edge devices with NVIDIA Jetson, and more tools and platforms to accelerate robotics development, like Isaac and the Jetson robotics reference platforms, we can help researchers and companies build robots that are more capable, less expensive, and safer to deploy.
Nvidia's Robotic Platform
Jesse Clayton | Nvidia
What is NVIDIA Isaac?
AI is disrupting many industries. Using powerful AI platforms such as NVIDIA Jetson, it’s now possible to deploy advanced AI to edge devices like robots. But one challenge that still remains is how to train them.
It turns out that AI-powered robots can learn in a similar way to humans. You give them a task and the provide them a sort of digital reinforcement (positive or negative) when they do the right or wrong things. While that’s effective, it’s extremely inefficient and even dangerous to let a real robot spend weeks attempting to lift a glass or move an engine block.
NVIDIA Isaac is a robot simulator for training AI-powered robots in a virtual environment. It includes high fidelity graphics and physics engines that can accurately replicate real scenarios, and simulated sensors and affecters that model the capabilities of the robot being trained. Because it’s virtual, the training can be accelerated and parallelized, and it mitigates the safety concerns of training on physical robots. Once the training is complete the learned behavior can then be deployed to the real-world robots.
What are the benefits of NVIDIA Isaac?
Isaac enables researchers to create visually detailed and physically accurate simulations to train robots, significantly reducing training and test time. For developing and deploying AI-powered robots, Isaac will reduce cost, accelerate training, and mitigate safety concerns compared to hardware-based development processes.
What are some of the challenges that NVIDIA Isaac overcomes?
Hardware prototypes are expensive to build. Physical test environments are expensive to build. And training robots in the real world is time consuming and in some cases dangerous. Isaac is an end-to-end system that uses physics simulation and advanced rendering to model robots, their sensors and rich, interactive environments. This enables researchers to reduce costs, accelerate training, and mitigate safety concerns. It will improve the process of designing and deploying AI-powered robots, compared to AI development using hardware alone.
Who are the potential customers for NVIDIA Isaac?
Isaac will initially be targeted at robotics researchers, but eventually we hope to make it available for anyone who is interested in robotics.
Can you run us through some scenarios where Isaac could be used for real world applications?
Today there are millions of industrial robots deployed around the world for tasks such as manufacturing, improving production efficiencies. However, most of these robots can only do simple tasks such as moving a widget from point A to point B. They don’t deal well with dynamic situations like changes in lighting and it can be very costly to reconfigure a robot to handle a new part in the manufacturing process.
Adding AI capabilities to these robots and training them quickly in complex simulated environments enables manufacturers to adopt automation in more diverse applications. Similar benefits can be applied to human service robots, cobots (collaborative robots), delivery robots and other use cases.
Tell me about Jetson reference platforms.
Many AI researchers would prefer to focus on the software, but they are limited by the lack of availability of hardware platforms.
To address this, NVIDIA partners are releasing open source Jetson reference platforms for specific form factors — including a service robot, UAV, USV, UGV, and other devices. These platforms provide building blocks for developers to quickly and easily create prototypes, helping reduce the time and money it takes to build robots from the ground up.
Which companies are releasing Jetson reference platforms?
The companies releasing Jetson reference platforms are:
-
Toyota for human support robots (HSRs)
-
Teal for consumer drones
-
Enroute for industrial drones and unmanned surface and ground vehicles
-
Universities and academia for scale model autonomous cars
Where do you see these technologies evolving over the next 5 to 10 years?
In the next 5 to 10 years we’re going to see a leap forward in the adoption of AI for robotics research and deployment. AI is a very promising technology that can address many robotics challenges that were previously unsolvable.
By continuing to add more computing capabilities for AI on edge devices with NVIDIA Jetson, and more tools and platforms to accelerate robotics development, like Isaac and the Jetson robotics reference platforms, we can help researchers and companies build robots that are more capable, less expensive, and safer to deploy.
About Jesse Clayton
Jesse Clayton is the senior manager of product management for intelligent machines at NVIDIA. He has more than 20 years of experience in technology, spanning software, GPU computing, embedded systems, and aeronautics. His current focus is bringing advanced computer vision and deep learning solutions to autonomous machines and intelligent devices. Prior to joining NVIDIA in 2005, he conducted NASA-funded research on aviation systems and algorithms. Clayton holds a Bachelor of Science degree in electrical and computer engineering from the University of Colorado, Boulder.
The content & opinions in this article are the author’s and do not necessarily represent the views of RoboticsTomorrow
Comments (0)
This post does not have any comments. Be the first to leave a comment below.
Featured Product
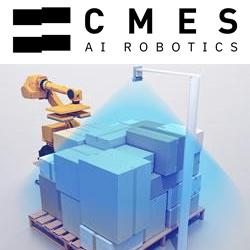