Either electric servo actuators or pneumatic cylinders can be used in robotic resistance spot welding; however, there are distinct advantages to going electric.
Lightweight Servo Actuators Lower Robotic RSW Costs
Bill Graber | Tolomatic
Buyers want sturdy, well-built cars, so the quality of welds that hold auto bodies together is crucial to vehicle manufacturers. Manufacturers want strong welds that are consistently and accurately placed so the finished car looks both durable and attractive.
Welding robots for resistance spot welding (RSW) have been a boon to auto manufacturers because they provide consistent weld placement. But all welding robots need actuators to carry and power the weld gun. Those actuators have a huge impact on the consistent quality of welds. They can also impact the cost of robotic resistance spot welding.
Either electric servo actuators or pneumatic cylinders can be used in robotic resistance spot welding; however, there are distinct advantages to going electric. For a thorough review of these advantages, see our white paper.
Electric beats pneumatic
Electric actuators outshine pneumatic systems when it comes to delivering strong welds consistently at a lower lifetime cost.
- Weld quality: Servo actuators apply the right amount of force for just long enough. Weld timing and pressure can be controlled nearly infinitely. Pneumatic cylinders, on the other hand, depend on compressed air systems that deliver fluctuating pressure levels which can mean inconsistent weld quality.
- Repeatability: Because electric actuators are programmable, weld quality is consistent and high. Speed, force, and other parameters can be locked in. Inconsistent weld quality is a given with pneumatic cylinders because inconsistent pressure is a fact of life with compressed air systems.
- Cost: Even though initially an electric servo actuator may cost more than a pneumatic cylinder, it will last longer (10-20 million welds versus 3 million). Also, electric linear actuators are more efficient, operating at 75-80% efficiency as compared to the 15-25% of pneumatic systems.
Finally, electric actuators can be re-programmed for product changeovers, avoiding the time and expense of making manual changes to pneumatic cylinders.
Lower the cost of robotic welding
Welding robots for RSW are expensive. Even the most efficient and effective electric linear actuator can’t get around the fact. However, if a smaller robot can be used, robotic resistance spot welding costs come down. A smaller RSW robot will need a lighter actuator.
Our new SWB and SWA servo actuators, part of our ServoWeld® product line, are lightweight, compact RSW actuators that can work with a smaller resistance spot welding robots. The ServoWeld Advanced (SWA) actuator incorporates our highest level of roller screw technology and delivers the maximum number of welds. The ServoWeld Base (SWB) actuator uses an alternate roller screw design to provide long life at a more economical price (better than other electric linear actuators with inverted roller screws or ball screws). The SWA and SWB can produce forces up to 4,000 lbf/17.8 kN, last 10-20+ million welds and hold +/- 3% force repeatability over the life of the actuator.
Find out more about the SWA and SWB by downloading our brochure.
The content & opinions in this article are the author’s and do not necessarily represent the views of RoboticsTomorrow
Comments (0)
This post does not have any comments. Be the first to leave a comment below.
Featured Product
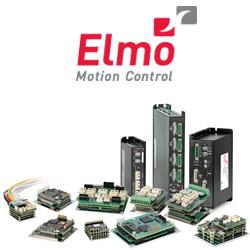