KEBAs latest product innovation is the worldwide unique control element KeWheel. KeWheel is an universal rotary pushbutton with adjustable haptic feedback which offers a completely new operating experience.
Talking PACK EXPO with KEBA Corp.
Contributed by | KEBA Corp.
Your company will be exhibiting at PACK Expo, what is it that makes this an important event for your company?
KeMotion Packaging is KEBA’s intelligent industry-optimized system solution specifically designed for machine builders in the packaging industry. The PACK Expo is a unique possibility to present our KeMotion Packaging solutions to an international audience and to get in contact with new machine builders that are looking for intelligent robotic solutions.
What can a visitor to your booth expect to see this year?
KeMotion Packaging built-in functions facilitate 25% speed boost through clock-synchronous movements of conveyer and robots. Just one single central controller is required to benefit from this speed increase.
Smart system features like the intelligent “look-ahead” robot movement control further magnify production performance while maintaining smooth and precise robotic motions.
Any new products you will be introducing?
KEBA’s latest product innovation is the worldwide unique control element KeWheel. KeWheel is an universal rotary pushbutton with adjustable haptic feedback which offers a completely new operating experience.
It transforms operation of your packaging machine into an experience that you can actually feel.
When you get a chance to walk the exhibit hall floor yourself, what is it you will be most interested to see?
The packaging industry is known to be a very innovative branch. Walking through the exhibit halls make visible which innovations are introduced and which packaging trends becomes reality.
PACK Expo has many educational sessions & Demo’s, is your company involved in any of them this year?
KEBA isn’t involved in this year’s educational sessions & DEMO’s.
When you book a booth for a tradeshow like this what are your expectations and what does your company hope to accomplish at the event?
A central position to reach a high visitor frequency rate of machine builders looking for new robotic solution suppliers.
The content & opinions in this article are the author’s and do not necessarily represent the views of RoboticsTomorrow
Comments (0)
This post does not have any comments. Be the first to leave a comment below.
Featured Product
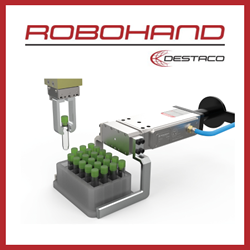