Cobots and mobile robots are both new technologies that are still being developed and industry is just now learning how to implement them. Further, these examples represent new applications that use robotics in applications where they have never been used before.
Disruptive Changes from Robotics Driving the Industrial Internet of Things (IIoT)
Mike Nager for | CMTS
Reprinted with permission from the CMTS blog:
In the world of automotive manufacturing, there are few technologies that promise to be as disruptive as robotics. Sound familiar?
While it’s true that automation and mechanization have been prevalent in the production of automobiles for nearly a century, industrial robots were introduced to assembly lines in the 1970s.
Nearly fifty years later, robots occupy enclosed spaces that are surrounded by steel fences with locked gates to keep them a safe distance from human contact. Characterized as dangerous — because of their fast-moving components — most industrial robots are equipped with sensors designed to stop all movement when their enclosures are opened.
The next wave of robots, however, are designed to co-operate with people, providing support alongside humans. Collaborative robots — also known as “cobots” — are safer, smaller and easier to program.
Unlike any robots that we have seen before, cobots are designed to work alongside a person — putting parts into boxes, flipping burgers or performing dangerous and/or repetitive tasks that can be automated. Cobots open new opportunities for employees with physical limitations or disabilities that prevent them from lifting heavy items or completing repetitive tasks that might lead to injury when completed by a human. Not only can cobots improve operational efficiency, but they can also improve the quality of products and the quality of life for workers in the manufacturing sector.
Another disruptive trend in robotics are mobile robots. For 20 years, or more, manufacturers have been talking about “connecting islands of automation”. For example, you might have a 200-foot long transmission production line. When the completed transmission comes off the line, someone needs to pick it up, transport it to another location and install it in the engine of a car. There are dozens of examples like this in the automotive manufacturing industry and mobile robots now can move these parts between assembly lines that might be separated by substantial distances.
Automated Guided Vehicles (AGVs) have been used in the past to move parts, but required metallic tape or other types of markers on the floor to navigate in a fixed path. Instead, mobile robots use laser scanners and other advanced technologies that allow them to determine their own path, avoid obstacles and be reprogrammed quickly.
Speaking of programming robots, disruptive changes are happening here, too, as artificial intelligence, machine learning and object-oriented programming languages are being applied to robots. The Robot Operating System (ROS), for example, is an open source operating system that is available for anyone to download, modify and implement. Some companies are also building simplified, non-proprietary programming languages that allow you to “teach” robots a desired motion or task simply by moving a small robotic arm, for example, in the desired motion. The robot “learns” the motion instantly, without the need to enter thousands of lines of code into a computer. Programming robots is becoming so simple that even children can do it.
At the same time, challenges remain; namely around implementation, awareness and the lack of qualified workers. Cobots and mobile robots are both new technologies that are still being developed and industry is just now learning how to implement them. Further, these examples represent new applications that use robotics in applications where they have never been used before. In some ways, it’s a paradigm shift. Certain tasks have always been manual, so these are big changes. Finally, there is a lack of skilled technicians and engineers, which are required to maintain this new technology.
At the end of the day, these advances in robotics are part of the industrial internet of things (IIoT), which promises to deliver significant benefits for manufacturers of all types.
Mike Nager, Business Development Manager, Festo, will present “The Challenges and Opportunities in IIoT” at CMTS on Tuesday, September 26 at 4:00 p.m where he will focus on the skills gap and how industry and education are working together to build the workforce of the future.
For more information, and to register, visit cmts.ca. Enter promo code BLOG at registration to save 30% off the conference list price or receive a free exhibit hall pass.
The content & opinions in this article are the author’s and do not necessarily represent the views of RoboticsTomorrow
Comments (0)
This post does not have any comments. Be the first to leave a comment below.
Featured Product
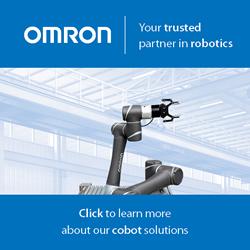