In this article, we will explore the basis and the future implications of this major transition. We will focus on two applications in particular: agriculture and last mile delivery.
Mobile Robotics: Thinking in Terms of Fleet Productivity Is Key to Success
Contributed by | IDTechEx
Autonomous mobile robots are causing a paradigm shift in the way we envisage commercial and industrial vehicles. In traditional thinking bigger is often better. This is because bigger vehicles are faster and are thus more productive. This thinking holds true so long as each vehicle requires a human driver. The rise of autonomous mobility is however upending this long-established notion: fleets of small slow robots will replace or complement large fast manned vehicles.
In this article, we will explore the basis and the future implications of this major transition. We will focus on two applications in particular: agriculture and last mile delivery. For both, we will demonstrate how autonomous mobile robots have already begun this transformation.
In this article we draw from two of our recent studies: Agricultural Robots and Drones 2017-2027: Technologies, Markets, Players; and Mobile Robots and Drones in Material Handling and Logistics 2017-2037. These detailed reports offer a comprehensive technology and market assessment, considering how robots and drones are penetrating into agriculture, logistics and material handling.
Last mile delivery vehicles: now and the future
Last mile delivery remains an expensive affair, often representing more than half of the total delivery cost. This is because it is inherently a low productivity process: small parcels must be delivered to custom destinations. This is in stark contrast to long haulage in which large loads are transported along fixed routes.
The current modes of last mile delivery all involve humans: a driver may drive a van along local routes, dropping parcels door by door; a person on a motorbike or cycle may carry one or few items to limited destinations per run; or both. These modes work and may be fast, but remain expensive despite employing many new business models and route-optimization algorithms.
Change is however underway, and we can already see the silhouette of the medium-term future: unmanned autonomous robots carrying small loads to pre-determined destinations. These robots may at first seem like strange creatures: they are smaller and slower than current modes of last mile delivery and can carry fewer items per trip, certainly making them less productive and thus less cost effective.
However, this is old thinking in which productivity is compared on a per unit basis. This is because autonomous mobility lends itself to fleet operation. In this model, one remote operator may monitor and control the work of many delivery robots. In this case, the wage and overhead of the person is spread over many robots. In essence, the fleet will magnify the productivity of the operator. Consequently, productivity must be compared at level of the fleet.Fleets of autonomous last mile delivery robots have the potential to ultimately boost the productivity in last mile delivery, thus reducing costs. Sources for robots: first row: Starship Technologies, Alibaba, and TwinWheel; second row: DJ, Dispatch, and Teleretail; and third row: SideWak,, Marathon Technologies, and Marble
In our report Mobile Robots and Drones in Material Handling and Logistics 2017-2037, we have built a model looking at the cost competitiveness of last mile delivery robots. We estimate the operator-to-fleet-size ratio at which mobile robots become more competitive than a man on a bike. This threshold is difficult to achieve given the current retail prices for early adopters of this robot technology.
Our roadmap suggests that this threshold become very achievable in the near future. This is because these mobile robots currently travel at low speeds along well-structured and uncrowded routes performing short delivery runs. In the future, as these robots learn more, they will become better adapt at navigating more complex environments at higher speeds with less supervision, thus boosting the productivity of individual units.
Furthermore, we expect the cost to fall dramatically in the near term. These robots do not require complex hardware. In fact, they are not too dissimilar to an electric scooter integrated with a mobile phone. Indeed, we expect the hardware platform to become commoditized in the future, and the primary value to shift towards fleet management and delivery services. This explains why some in this business are already self-positioning as providers of robots-as-a-service (RaaS).
The forecasts in our report Mobile Robots and Drones in Material Handling and Logistics 2017-2037 suggest that the sales of ground-based last mile delivery robots will be modest until 2021-23. In this early phase the industry is essentially in learning mode and the activity will be limited to trials or modest sales for use in sparse and highly-structured environments. The growth phase will then commence. In this phase, the robots will also become increasingly ready to handle more crowded environments and their speed of travel and navigational technology will significantly improve. The unit sales boom and the hardware product will become commoditized. This way we will witness the rise of fleets of small-sized last mile delivery robots.
For further information please refer to our report Mobile Robots and Drones in Material Handling and Logistics 2017-2037.This report provides a comprehensive assessment of robots and drones in material handling and logistics. It considers many uses cases beyond last mile delivery robots including automated guided vehicles/carts; autonomous industrial material handling vehicles, autonomous mobile carts, autonomous mobile picking robots, and autonomous trucks
Agricultural vehicles: now and the future
The traditional thinking is to develop larger, faster and more powerful agricultural vehicles like mammoth tractors to boost productivity. This has been sound thinking thus far: such vehicles amplify the productivity of the driver, enabling it to cover more ground per hour in a limited time window that the weather might permit.
As discussed in our report Agricultural Robots and Drones 2017-2027: Technologies, Markets, Players, agriculture is the leading adopter of autonomous mobile technology: we estimate that more 320,000 autosteer and auto-guidance tractors will be sold in 2018 (up to level 4 autonomy). The technology is already evolving towards full navigational autonomy (level 5). Indeed, as the numerous prototypes demonstrates the commercialization emphasis has shifted from addressing technical issues towards tackling commercial and behavioural challenges.
The rise of autonomous mobility may also enable another type of agricultural vehicle that might also at first seem like a strange creature: the small, slow and lightweight agricultural robot (agrobot). These robots are evidently less productive than a larger vehicle therefore you might wonder why are they being seriously considered by players large and small around the world?
The answer here, as was the case in last mile delivery robots, is in fleet operation. Autonomous mobility eliminates the need for a human driver per vehicle, enabling the cost of the remote operator to be spread across the fleet. This instantly lowers the operational cost per unmanned robot. As was the case with last mile delivery robots, here we also find that achievable operator-to-fleet-size ratios exist at which fleets of small agrobots become attractive.The seeds of a paradigm shift in the way we envisage agriculture machinery have been sown. In this shift few large, heavy, and fast vehicles are replaced with large fleets of small, slow and light weight agrobots. Images source for agrobots: first column: FENDT; Queensland University; Naio Technologies, Australia Centre of Field Robotics, and ecoRobotix; second column: Earthsense, Idaho, and Kongskilde; and third column: Rowbot, Ibex Automation, and Vinerobot
This alone however may not be compelling enough since large tractors will also become autonomous, lending themselves to fleet operation. Such fleets will reduce the headcount, cut down the wage bill incurred in farming and open the door to limited precision farming.
Fleets of small agrobots will go further in that they will enable site-specific or even plant-specific ultraprecision farming. These slow-moving robots will give each site the customized attention that it needs all the way from planting to harvesting. This would be akin to industrialized gardening. This will boost yields and will also significantly reduce chemical use. Furthermore, these light robots will cause no soil compaction and will drive down energy consumption, emitting no noise and CO2 since they are electrically powered.
Here too we are also at the beginning of the journey. We also see numerous such robots developed at start-ups and research entities. We are also witnessing more engagement from larger firms with some promising to take such robot swarms towards full production. This is why our report forecasts that autonomous small mobile robots will grow to more than $500M annual sales in 2028.
For further information please refer to our report Agricultural Robots and Drones 2017-2027: Technologies, Markets, Players. This report develops a detailed roadmap of how robotic technology will enter into different aspects of agriculture and how it will change the way farming is done. It will consider many applications and technologies including static milking robotics, mobile dairy farm robots, autosteer tractors, autonomous tractors, unmanned spraying drones, autonomous data mapping drones, robotic implements for de-weeding, autonomous de-weeding mobile robots, robotic fresh fruit harvesting, robotic strawberry harvesting, manned and unmanned robotic lettuce/vegetable thinning/harvesting and so on.
About IDTechEx
IDTechEx guides your strategic business decisions through its Research and Events services, helping you profit from emerging technologies. We provide independent research, business intelligence and advice to companies across the value chain based on research activities and methodologies which provide data sought by business leaders, strategists and technology scouts to aid their critical business decisions. To discuss your needs please contact us at research@IDTechEx.com or see www.IDTechEx.com.
The content & opinions in this article are the author’s and do not necessarily represent the views of RoboticsTomorrow
Comments (0)
This post does not have any comments. Be the first to leave a comment below.
Featured Product
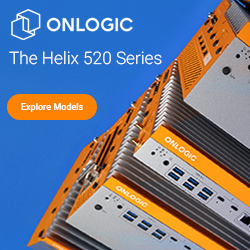