It seems likely robots will continue to be instrumental in helping companies cope with the persistent welding skills shortage. This is a strong example of how technology can assist with overcoming factors that cant always be easy to control or solve.
Kayla Matthews | Productivity Bytes
Welding involves using heat and pressure to join two materials. It plays a crucial role in the manufacturing industry, and companies are consistently looking for ways to achieve productivity goals without sacrificing quality.
The welding industry is dealing with a severe shortage that may cause 290,000 unfilled welder positions by 2020, according to the American Welding Society. To compensate, some companies are using robots to fill the void.
What Are the Reasons Behind the Shortage?
Data from the Bureau of Labor Statistics indicates the job growth outlook for welders is 6 percent, which is about as fast as average compared to all other positions. Plus, the median annual wage for welders in 2016 was $39,390. So, it doesn’t seem lack of growth or low pay are substantial contributors to the shortage.
Industry analysts say interest in welding is growing. However, there are also statistics revealing the average welding operator is nearing retirement age. When experienced welders leave the workforce, they possess knowledge gained by countless hours on the job. Apprenticeships help new welders gain ground, but still, it takes time for them to get up to speed.
Robots Help Make up the Difference
As a result of the welding shortage, some companies are figuring out what to do until new welders acquire more skills. Some are transitioning into simpler processes, but others are installing robots at their facilities. Welding robots are not new — in fact, General Motors used the first programmable model to perform spot welding in 1954.
There are several components of a robotic welder, also known as a robot welding cell. They work together to either perform the welding functions or apply safety features to ensure the technology works as it should.
The Investment Pays for Itself
Before a company makes the decision to start using robots to handle some welding tasks, it must secure the necessary funding and make in-depth plans to determine how a robot would fit into a facility’s existing processes and whether the current layout of a workspace allows for adding new equipment.
Despite these preliminary measures and the monetary and labor force-related investments needed to execute them, companies can typically recoup the costs associated with installing robotic welding equipment in improved productivity, reduced waste and higher quality.
For example, humans typically become more fatigued as their time at work rises. In contrast, robots do not need rest breaks, and their outputs do not go down as operating time increases.
Also, the parts of many robotic welders are designed for long-term usage, so they work for longer periods of time before requiring replacement, unlike the materials used for some manually operated welding equipment.
Besides saving money through fewer purchases of new parts, robotic welders are highly efficient and automated. Therefore, the probability of error decreases, resulting in fewer scrap pieces.
Trained Operators Are Required
Even though the functions of welding robots are largely automated, that doesn’t mean companies can run them unattended. A trained operator with experience in the robotic welding sector must oversee operations as they progress.
If robotic welding continues to play a significant role in the industry, some workers may find it is in their best interests to get trained as operators. Experts say it’s easier to train a person to run a robot than to teach him or her how to weld.
However, that individual must understand how to read statistics that indicate a robot may require better programming to perform at its best. Robotic welding equipment is consistent, which is a good thing when it’s programmed correctly. However, problems can result if a robot that needs fine tuning runs too long without intervention from humans.
Based on the information above, it seems likely robots will continue to be instrumental in helping companies cope with the persistent welding skills shortage. This is a strong example of how technology can assist with overcoming factors that can’t always be easy to control or solve — such as members of the workforce getting close to retirement age or new welders who find they still have a lot to learn through on-the-job training.
The content & opinions in this article are the author’s and do not necessarily represent the views of RoboticsTomorrow
Comments (0)
This post does not have any comments. Be the first to leave a comment below.
Featured Product
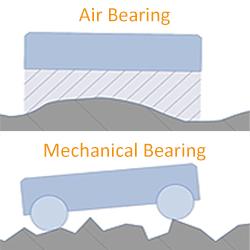