Stairs are still unsurmountable obstacles for many robots. Yet a young team at ETH Zurich is building a vehicle designed to negotiate steps with ease – by hopping.
Adrian Venetz | maxon motor
Reprinted with permission from the maxon motor drive.tech:
Stairs are still unsurmountable obstacles for many robots. Yet a young team at ETH Zurich is building a vehicle designed to negotiate steps with ease – by hopping.
"Ascento" is the name given to the sophisticated device by its creators, a team of eight students majoring in mechanical engineering and one in electrical engineering. The robot is quite special: It moves and balances on two wheels. From an engineering standpoint, this is significantly more difficult than building a device on four wheels. However, a bipedal robot provides much better mobility and adaptability to different terrain types.
That's not all: The main goal of the nine up-and-coming engineers is to make the robot leap. They want it to be able to jump high, like a kangaroo, and land again safely on its two wheels. “This would enable the robot to master stairs and other obstacles,” student Florian Weber explains. The Ascento team originated from a focus project. In this type of project, undergraduate students of various disciplines have a chance to apply their knowledge to a concrete project – from the initial idea to a functioning prototype.
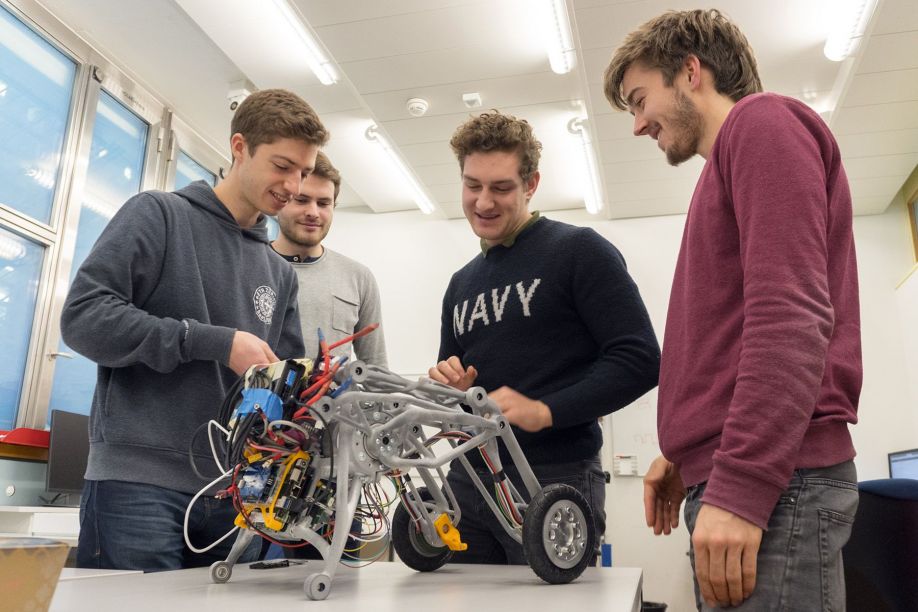
The special feature of the Ascento is that it is designed as an inverted pendulum: The center of gravity is above the axis. As a result, the Ascento is able to stand and move only as long as it is powered and actively maintaining balance on its wheels – similar to a standing human, who continuously has to expend energy to maintain balance. This makes the Ascento comparable to a Segway, which is also driven by two wheels that are on the same axis and requires a controlled drive to maintain balance.
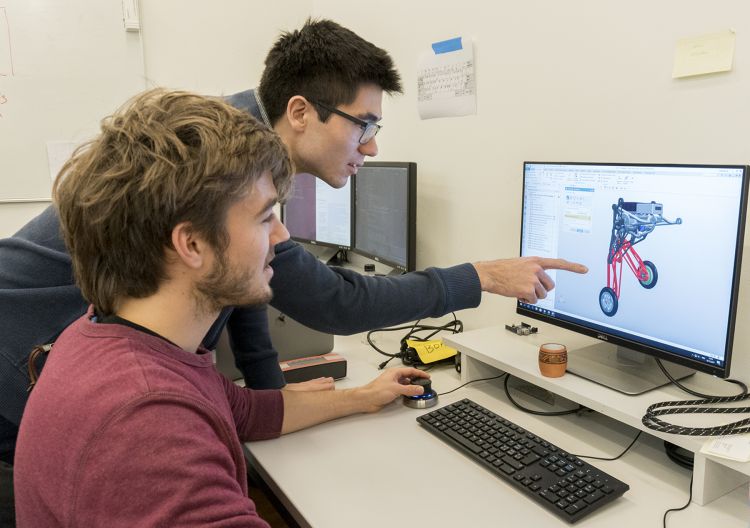
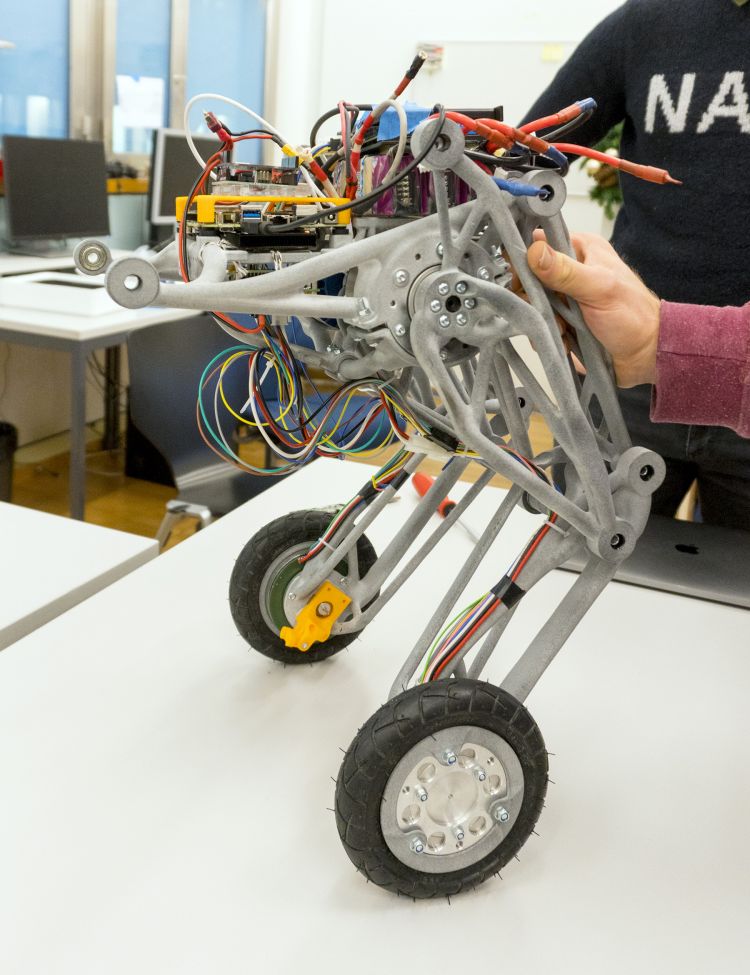
The content & opinions in this article are the author’s and do not necessarily represent the views of RoboticsTomorrow
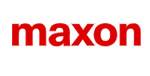
maxon group
maxon is a leading supplier of high-precision DC brush and brushless servo motors and drives. These motors range in size from 4 - 90 mm and are available up to 500 watts. We combine electric motors, gears and DC motor controls into high-precision, intelligent drive systems that can be custom-made to fit the specific needs of customer applications.
Other Articles
Multi-axis motion control drives pipe-based robots
Automate 2025 Q&A with maxon group
Understanding Torque and Speed in Electric Motors
More about maxon group
Comments (0)
This post does not have any comments. Be the first to leave a comment below.
Featured Product
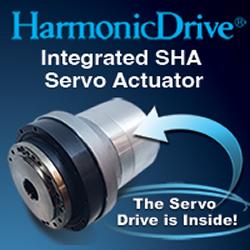