The main feature that I like is just that it has kept the precision and repeatability over the last 5 years and we havent had to worry, we havent had to replace any parts. We have done virtually no maintenance what-so-ever.
Case Study: Epson Robots at Taylor Guitars
Contributed by | Epson Industrial Robots
Taylor started in 1974 by Bob Taylor and Kurt Listig, they were the first 2 owners of the company and they're still here today.
When I tell people I work at Taylor they think one of two thoughts, either there is a craftsman behind a bench with an apron whittling away with a chisel or its a production line like a car assembly.
And when they actually come and see, they see its really a marriage of the two, where you have folks doing a lot of hand-work alongside with machines.
We had been talking about getting into robotics, the Epson robot was brought in primarily to make our acoustic pick-ups. And I was making them by hand, I could make ten or twenty a day, at first we needed a hundred a day, and then we've ramped up to close to six hundred a day. So we wouldn’t have been able to do it without automation.
Taylor has always been about innovation, not only in the guitar itself but also in the process. It's really important that we keep craftsmanship in everything we do, and as part of that with our engineers, with the folks who are responsible for the robotics, we want to make sure that they understand what it is to be a craftsman. To work with our craftsmen that are on the production line and they get to see with their own eyes what it takes to make something by hand. And then from that point, and only at that point, we would then try to automate it.
We really like the Epson G3 because when you tell it to do something it does that exactly the same every time.
The main feature that I like is just that it has kept the precision and repeatability over the last 5 years and we haven’t had to worry, we haven’t had to replace any parts. We have done virtually no maintenance what-so-ever.
The content & opinions in this article are the author’s and do not necessarily represent the views of RoboticsTomorrow
Comments (0)
This post does not have any comments. Be the first to leave a comment below.
Featured Product
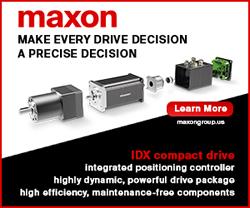