As a human, you have an intuition about how a good movement looks. Transferring that intuition to the robot happens more naturally through guiding than through writing a sequence of motor control commands.
Using AI to Train Robots
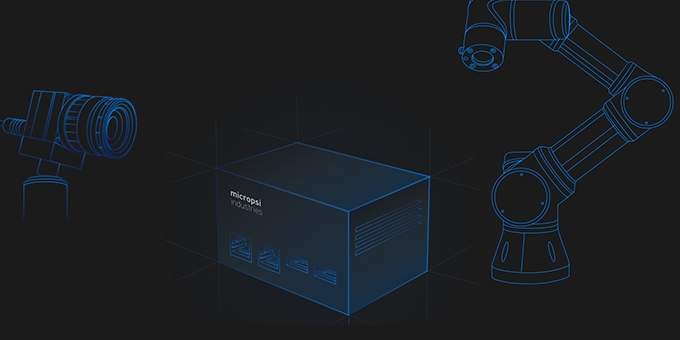
Ronnie Vuine | Micropsi Industries
What is the future of industrial robotics?
In any plausible future of industrial robotics, robots will do a lot more than they do today. Smaller and safer machines are already conquering new fields today. Combine that with a software layer that can actually deal with variance, as perceived by sensors, numerous tasks that are currently manual, can be automated.
Can you give me an example of how complicated tasks of tomorrow can be done by robots vs. the simple tasks they do today?
Robots actually do solve complex tasks today — but these always have a specific property. They're deterministic, which means that, at any point in time, you know in advance where your robot needs to be, because you know where the workpiece is. For instance, when welding a car in a manufacturing plant, you know where the car is, it's harnessed, moving through the factory at a defined speed, so all you need to do is position the robot at a pre-planned place, and you're done.
Now, imagine you're dealing with tasks that don't have that property. Famously, Tesla just tried to automate such tasks. They attempted to plug in cables with robots. Now cables are challenging because they're soft and move about in an unpredictable fashion. So to handle them, you need sensors — cameras, in this case -- that look at the cables and decide how to react to their movements, quickly and frequently: “OK, this looks slightly out of place to the left, I'll make a corrective movement with my robot hand and approach the plug from a slightly different angle.”
There are many tasks like this – those that aren't automated today because not just the end points of the relevant movements matter, but the way the movements itself are executed.
We hear a lot about cobots. Why are cobots trending? How will they change what people think about robotics?
Collaborative robots or Cobots are robots that are supposed to work together with humans. I like to be a heretic in this matter and claim that most people in production don't care much for that working together aspect: It's too hard to pull off, and it requires factories to keep all the infrastructure for humans in place. Humans take a lot of space, they need light, bathrooms, pleasant ventilation, and escape routes and all that. Robots alone require less space and don’t have these same requirements. So, laying out a new factory for both humans and robots doesn't make much sense. You may as well automate it all, if you happen to have the software and the actuators to do so.
So they're not trending for being actually collaborative. I believe they're trending because they're not dangerous — lighter, slower, smaller than the old machines — and that means they're much easier to program. Humans can be close to them during setup, and show them where to go, or how to make a movement that works.
Getting the programming user experience right is an important factor for the spectacular success of these machines -- with a projected CAGR of 55 percent for the whole market and some companies outperforming even that number significantly.
Another reason cobots are doing so well is that some companies who make them understand that they're offering platforms. So, there are now reasonable APIs and technologies that IT people have heard of, and the robot makers actively support developers working with these interfaces.
What role would software play in industrial automation as things get more complex?
Historically, three things have held back robotic automation -- cheap labor abroad, lack of suitable end-effectors for many tasks, and a lack of good sensor-evaluating software. Now, the era of cheap labor is drawing to an end, there are many exciting new end-effector technologies, and we can finally bring machine learning to the table on the software side. We can learn movements now, we can use a wide array of sensors, we can deal with unpredictability.
Tell us about your company.
Micropsi Industries is a VC-backed robotics software company, founded in 2014 in Berlin, Germany. We make AI applicable to industrial use cases. We are a team of 15 people – with expertise in artificial intelligence, robotics, automation and entrepreneurship.
What's your product and how does it work?
Our product is an artificial intelligence system (software, controller, camera), including our unique software called Mirai – which means “The Future” in Japanese. The software enables robots to learn skills that would be hard or impossible to hand-engineer, as they require proper hand-eye-coordination. Think of our product as the brain that operates industrial robot arms.
Simple tasks take just two afternoons of demonstrations. So after two days, your robot can look at a workspace, recognize what is expected of it, and perform the movement.
As these movements are learned from humans — generalized over the demonstrations given — they look completely unlike traditional industrial robot movements by the way, much more organic and friendly. The eerie quality of a large and powerful piece of industrial kit making sub-millimeter-precise, linear movements is gone.
What's the difference between programming and training robots?
Programming is the equivalent of telling someone who wants to play tennis to throw the ball up in the air, hit it hard with the racket, and miss the net, then giving a list of very detailed verbal instructions about where the racket needs to be.
Training is the equivalent of taking someone’s wrist and showing how it's done, and then correct the player during rehearsals.
With Mirai you're doing the latter, at least for the tricky movements, where it would be extremely hard to come up with a set of verbal rules of how to interpret the pixels coming in from a camera and how to move six electric motors to get the movement you want. Instead, users make the movement, together with the robot. After some time, it attempts to make the movement on its own, and you just correct it (again, by touching its wrist) until it's there.
You talk about being able to train robots. Why is that a better approach than reprograming? How can robots learn a new skill?
To begin with, it's much easier. As a human, you have an intuition about how a good movement looks. Transferring that intuition to the robot happens more naturally through guiding than through writing a sequence of motor control commands.
And if you want a movement to be real-time and fully camera-driven, you'd be out of your depths very quickly, even if you're a high-end engineer. Such things are extremely hard to hand-engineer.
Who is your primary customer and how do they benefit from your technology?
We're just beginning to see what people can do with the technology, but assembly tasks are our main are of interest. Putting together plastic parts, plugging in cables, placing gears in gear boxes and more.
We like to look at industries that aren't automated as much as automotive is, like electronics manufacturing or food. For many of these customers, robotic automation is completely new, and we're typically deploying our technology into automation projects that strive to replace unpleasant and repetitive work.
About Ronnie Vuine
Ronnie Vuine is co-founder and CEO of Micropsi Industries, a robotics software company headquartered in Berlin, Germany -- recognized by Smart Industry as one of 10 startups whose “technology will shape our future.”
A philosopher and computer scientist by training, he has a long-standing passion for artificial intelligence and enabling technical systems to inter-act autonomously with the real world. With the Micropsi Industries team, he set out to transform the industrial robotics market by applying the flexibility made possible by machine learning to manufacturing. He regularly speaks at tech conferences and writes about the future of artificial intelligence, robotics, and manufacturing automation.
The content & opinions in this article are the author’s and do not necessarily represent the views of RoboticsTomorrow
Comments (0)
This post does not have any comments. Be the first to leave a comment below.
Featured Product
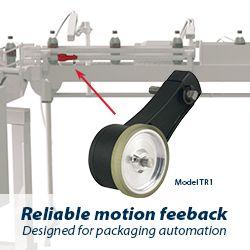