Booth #5014 - The next generation of AquaGard 7350 Conveyors feature an improved frame design, nose bar transfer options and the industry’s safest and most robust curve modular chain.
Contributed by | Dorner Mfg. Corp.
Tell us about your company.
At Dorner our mission is to Transform Conveyor Automation by providing cutting edge solutions with best-in-class support. It’s that commitment and history of proven excellence that has made the Dorner Brand a recognized leader in conveyor systems for over 50 years. With our complete line of customizable stainless steel and aluminum conveyor automation systems, Dorner can provide solutions for almost any conveyor need.
Dorner’s conveyors are designed to move product to the exact location, at the exact time and in the exact position it needs to be for the next phase of the production line. With benefits such as industry best product transfers and in-house belting capabilities, Dorner is leading the market in precision conveyance. This extremely accurate product control allows Dorner conveyors to easily integrate with robots, workers and equipment.
Your company will be exhibiting at ATX & Design & Manufacturing West, what is it that makes this an important event for your company?
WestPack is the best packaging trade show on the West Coast and we look forward to exhibiting every year. We find the show always brings quality attendees and attracts a broad range of consumers.
West Pack attendees come to the show with current projects and applications and we find it to be an important show for us every year.
Highlight a 2 or 3 products you will be showcasing at the event?
One conveyor we will be showcasing is our new redesigned AquaGard 7350 Series. The next generation of AquaGard 7350 Conveyors feature an improved frame design, nose bar transfer options and the industry’s safest and most robust curve modular chain. The modular belt curve conveyor has no openings greater than the international standard of 4mm, even within the curves, which increases safety by eliminating pinch points for operators.
We’ll also be featuring our FlexMove Helix Conveyor. The Helix Conveyor features a compact, flexible design and small footprint that maximizes valuable floor space while providing customers with flexibility in layout. The custom infeed and outfeed lengths allow the conveyor to extend beyond the spiral, reducing the number of conveyors required. The Helix Conveyor is ideal for applications including accumulation, buffering, cooling between processes or machines.
When you get a chance to walk the exhibit hall floor yourself, what is it you will be most interested to see? Any educational sessions, pavilions etc. you plan on attending?
WestPack always has so many interesting events and educational sessions and we’re excited to see what they have to offer this year. We plan to catch some of the presentations at Center Stage to learn about the newest trends in the packaging industry.
The factory floor is undertaking rapid advancements, be it automation, robotics, machine vision or data. The Automation Technology is a huge part for many manufacturers, give us an idea on how your company and product is being utilized now in the smart factory.
Often times the significance of the conveyor in the packaging line can be underestimated. A packaging line can only go as fast as your conveyor. The entire line is limited by the slowest machine on the line. With our conveyors, we put a big focus on precision and product orientation so when it gets to that next piece of equipment, it’s ready and it won’t be the bottleneck. So often, the simplicity of conveyors is overlooked.
Give us your thoughts on what the future holds for manufacturers and automation technology.
Automation really demands efficiency. Integrating robots with precision conveyor systems is one way to enhance the productivity of a processing line. Robotic applications often require a product to be in an exact spot on the conveyor at the right time. But to do that successfully requires a conveyor system that’s efficient, reliable and engineered to work in conjunction with robotics. Conveyor design is certainly being affected by the continuing trend of flexible assembly lines. When customer demands change and product cycles end, assembly lines need to be flexible to accommodate different applications
The content & opinions in this article are the author’s and do not necessarily represent the views of RoboticsTomorrow
Comments (0)
This post does not have any comments. Be the first to leave a comment below.
Featured Product
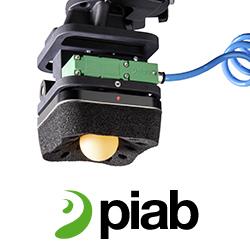