The challenges around outdoor snow removal are two-fold. First, businesses and commercial sites must keep walkways and pathways clear for safety reasons and they face a labor shortage of those willing and able to do such incremental work.
Swift Navigation Case Study: Left Hand Robotics
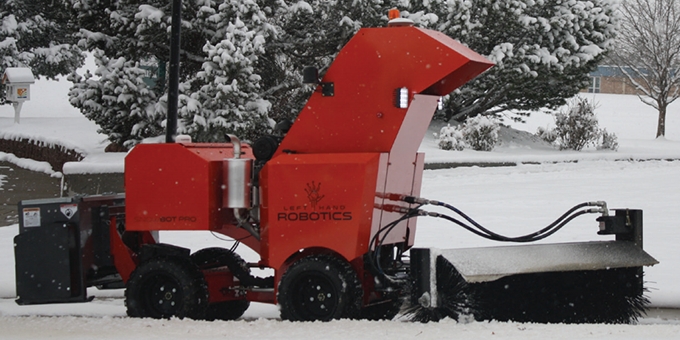
Contributed by | Swift Navigation
Left Hand Robotics was founded with the mission to produce safe, reliable autonomous robots designed to perform physically demanding outdoor tasks. Based in Longmont, Colorado, Left Hand Robotics’ innovative automation and advanced technology solutions for outdoor operations allow businesses to reduce labor costs. The Left Hand Robotics founding team brings over five decades of experience in software and robotics to address difficult problems such as snow removal.
Challenge
The challenges around outdoor snow removal are two-fold. First, businesses and commercial sites must keep walkways and pathways clear for safety reasons and they face a labor shortage of those willing and able to do such incremental work. This challenge is addressed by looking at autonomous solutions that do not require physical labor to complete snow removal tasks. Second, creating an autonomous robotic solution that can perform the task has limited margins for navigation error. Often, sidewalks and walkways have landscaping, walls, curbs and other obstacles that would be damaged were a robot to run over or into it. GNSS technology with centimeter-level accuracy is required to ensure a robot avoids obstacles and stays on its designated route.
Solution
Left Hand Robotics found real-time kinematics (RTK) GNSS to be the solution to its centimeter-level accuracy needs. This level of accuracy keeps the robot in its designated path and allows its base robot platform to navigate in a variety of environments—whether in lines (e.g., sidewalks, bike paths) or large open areas (e.g., fields, parks). Finding a reliable RTK GNSS solution was critical given that many sidewalks are near buildings and underneath trees.
Swift Navigation’s Piksi Multi is the solution to Left Hand Robotics’ navigation needs and allows it to achieve the desired accuracy and retain a GNSS-fix in challenging conditions and environments. Initially Left Hand Robotics tested a competitive product, but it did not meet performance requirements. After continued evaluation, Left Hand Robotics selected Piksi Multi as its GNSS solution due to both its performance and affordable price. Once Swift’s ruggedized Duro receiver was launched—and could be used by customers as a base station that was required for RTK—Left Hand Robotics had a complete offering for customers. Piksi Multi is installed in each SnowBot Pro and its Path Collection Tools (the tool their customers use to collect the initial path data that the robot will follow) and Duro is used as the base station controlling the SnowBot Pro robot.
Results
SnowBot Pro became available in Winter 2018-2019 and is the only commercialgrade, robotically-driven product for snow removal on the market. Its autonomous capabilities allow SnowBot Pro to clear snow from walkways with a 56” wide rotating brush, reducing the number of hand shovelers or snow blower operators needed by up to 80%. Its different attachments for both the front and the rear of the robots allow for a multitude of tasks—snow removal in the front and deicing in the rear. The SnowBot is programmed and then controlled remotely from the cloud via an online dashboard or mobile app and follows its programmed path using GPS, accelerometer and gyroscope technologies for navigation. Sensors detect any obstacles and can instruct the robot to stop to avoid collisions and send instructions about how to bypass obstacles. Location, weather and robot status data is recorded in real time, including before and after photos. This detailed recording helps to minimize insurance and risk management costs that snow removal companies face from potentially costly Slip & Fall insurance claims, while at the same time providing customers with proof of work.
The content & opinions in this article are the author’s and do not necessarily represent the views of RoboticsTomorrow
Comments (0)
This post does not have any comments. Be the first to leave a comment below.
Featured Product
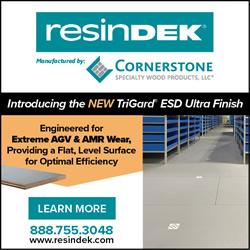