Before selecting a picking technique for your operation, evaluate your current inventory situation, workforce, technology, infrastructure and warehouse layout. Once you assess all of these factors, you can confidently determine a picking methodology
Zone Picking vs. Wave Picking: Which Method is Best?
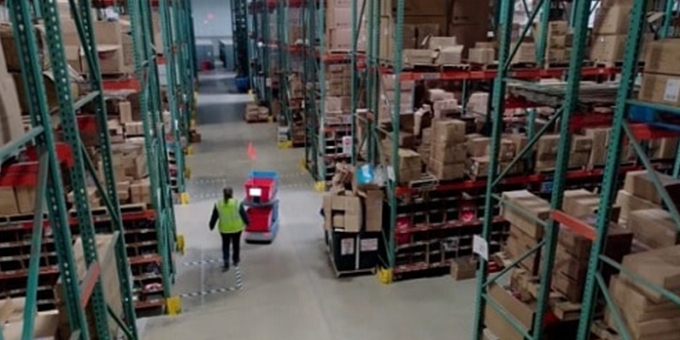
Will Allen | 6 River Systems, Inc.
While warehouse technologies are advancing rapidly these days, even the world’s biggest warehouses continue to rely on fundamental practices that have been around for decades. Take warehouse order picking practices, for instance. While most order picking techniques can be augmented and/or streamlined with the help of collaborative technologies, such as collaborative mobile robots, the basic principles aren’t new — they’re just made more efficient with the help of technology.
Let’s take a look at the ins and outs, pros and cons and best practices for two common order picking methods: zone picking and wave picking.
How zone picking works
In zone picking, which is also known as “pick and pass” methodology, pickers are assigned to a specific physical zone. Once there, the associate picks all SKUs in that zone for each and every order that comes in. For orders with SKUs in multiple zones, orders are filled by passing through the required zones, often following a strategic series of movements across the warehouse floor.
Advantages and disadvantages of zone picking
Zone picking comes with a range of advantages and disadvantages, which often depend on the size, scope and organizational style of the operation.
Advantages: One of the biggest plus sides of zone picking is that it allows zones to be configured based on different criteria, such as fast-moving and slow-moving SKUs or a zone dedicated to high-security SKUs. Zone picking is particularly useful in large warehouses that deal with a high number of SKUs. Because each picker is assigned to a designated area, it allows pickers to gain deep familiarity with their assigned zones and the SKUs stored there, which can increase picking speed and reduce errors.
Disadvantages: The most glaring disadvantage of zone picking is that the methodology only allows for one scheduling period per shift, meaning there’s a hard cutoff point for orders to be queued. Any orders entered after that cutoff point won’t be filled until the following shift. Additionally, load balancing zones for labor management can pose challenges.
How wave picking works
Another commonly-used picking technique that is used in today’s warehouses is wave picking. This method is similar to discrete picking in the sense that pickers pick one order and one SKU at a time. What sets wave picking apart from discrete picking, though, is a scheduling window. It can be organized around factors such as common stock-keeping units (SKUs), commonality in the SKU location, shipping deadlines, common carriers and common sorting or kiting processes used in the warehouse.
Advantages and disadvantages of wave picking
Depending on the specifics of the operation, wave picking comes with a host of advantages and disadvantages.
Advantages: Generally, wave picking is considered more efficient than strict order line picking, and it offers reduced travel time for order pickers. Orders can be scheduled to be picked at specific times throughout the day, which can be used to optimize picking and shipping operations.
Wave picking can also be coupled with an active replenishment strategy to limit how much inventory is required to be on shelves. Sometimes this is referred to as “only stock what you need”.
Disadvantages: One of the main disadvantages of wave picking is that items are processed in a serial manner, as they are in discrete picking. This means that workers and equipment must wait until one wave is complete before moving onto the next wave. It’s difficult to process more than one wave simultaneously, primarily due to the availability of equipment, sortation or processing areas, making it challenging to accommodate high-priority picks and tasks. Another common issue with wave picking is that some processes may be completed before others, leading to idle time while some workers wait for others to complete their work before the next wave can begin (which can impact warehouse efficiency). Wave picking also lacks flexibility. For example, it’s not easy to add similar work or additional tasks to a wave that’s already in progress.
Which method is best?
While zone picking and wave picking each have advantages and disadvantages, it’s important to remember that no picking method is a one-size-fits-all solution. In fact, some warehouses use a combination of picking methods to suit different needs.
Before selecting a picking technique for your operation, evaluate your current inventory situation, workforce, technology, infrastructure and warehouse layout. Once you assess all of these factors, you can confidently determine a picking methodology (or combination of methodologies) that are best-suited to meet your warehouse’s needs.
This article originally appeared on 6river.com
The content & opinions in this article are the author’s and do not necessarily represent the views of RoboticsTomorrow
Comments (0)
This post does not have any comments. Be the first to leave a comment below.
Featured Product
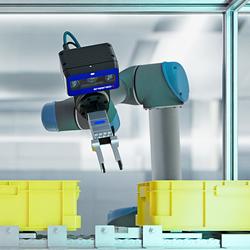