“High levels of up-front expenditure, both in development and hardware, characterise the space, typically demanding large scale pain points before investment begins.”
How the Combination of Robotics and AI Can Transform Industries
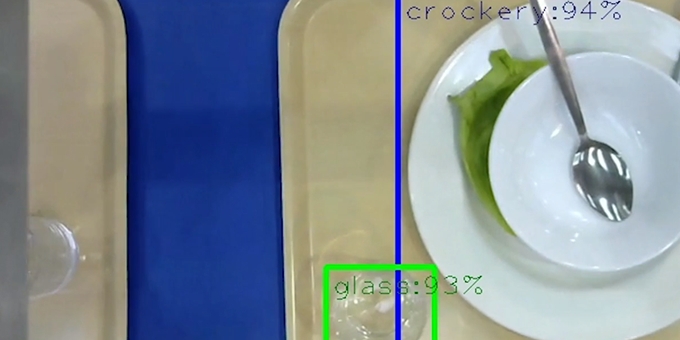
Henry Fletcher, Principal Engineer, Cambridge Consultants | Cambridge Consultants
In my role as a technical lead at Cambridge Consultants I work on a variety of projects for clients across a broad range of industries. Empowered by continuously improving machine intelligence and capability an increasing number of these projects sit at the intersection of robotics and AI. The two terms are so broadly used that it will be helpful for us to create shared and simple definitions for the purposes of this article.
In general parlance, the term “AI” is used to refer to machines that can solve tasks considered difficult for machines at that point in time. Due to technological advances the complexity and capabilities of systems considered to be AI by this definition therefore increases as time passes.
Rather than defining the derivative term "robotics" we should instead describe what a robot is. I’ll adapt a definition given by MIT Media Lab Roboticist Kate Darling: “A robot is a physical machine that can execute tasks autonomously.”
A Kuka 6 degree of freedom arm, rigidly following a simple set of pre-programmed rules to weld a car chassis, with no regular human input, would be considered a robot. But to consider this an AI system in 2019 there would also need to be a deeper layer of capability, such as sensing the material ahead of the melt zone, or analysing the quality of the completed weld and modifying the approach to improve the results.
If we were to ask where the combination of robotics and AI can provide industrial transformation, the immediate view in many people’s minds is the direct replacement of human workers, for example in picking strawberries. This is only a part of the picture, significant gains are also enabled by replacing or upgrading existing machines (see our welding example above), by augmenting human capabilities (such as by presetting no-go zones in robotic surgery) and by opening completely new options that previously were not possible (for example micro surgery robots may need to make their own decisions due to difficulty in communicating with them inside the body).
The successful combination of robotics and AI results in systems that perform complex and often high energy tasks quickly and with exceptional consistency. In many cases, trying to design a system that mimics how a human would solve the task will result in failure. This was clearly illustrated during the first phases of a project named Turbo Clean where I led part of the technical work. Turbo Clean is a system designed for the food service industry that clears crockery, glassware and cutlery from a canteen tray. Initially we attempted to fully recreate the real objects to be handled in a virtual 3D environment, and then plot the route for grasping and removal with a pincer-like gripper. The computational requirements and precision required were simply not economically feasible. I redirected effort towards a substantially different approach, relying on rapid but less precise and lower confidence identification. For object identification optimised for real time applications we selected a YOLOv2 neural net architecture, ported the implementation to Tensorflow, trained it on our own dataset, and paired it with a gripper and mechanical gantry that could tolerate this lower positioning accuracy and could generate the required forces for much faster motion of the items. The enabling additional subsystem was a secondary and tightly coordinated stage that empties debris from the items after singulation by the gripper. It’s an exciting example of what is possible when we play to the strengths of an AI and robotics combination - Check it out.
Industrial applications lag a fair way behind the state of the art, for straight forward economic reasons. It’s largely possible for a sophisticated robot to fold mixed laundry but you will not find the UC Berkeley PR2 in your local laundrette, because the system is prohibitively expensive. High levels of up-front expenditure, both in development and hardware, characterise the space, typically demanding large scale pain points before investment begins.
The growth and profitability of many industries is already substantially dependent on AI and robotics solutions, for example, the automation in large scale logistics warehouses. I have been working with a client recently that specialises in providing combined robotic and AI systems that perform some of the most computationally difficult and tedious tasks, where individual items (that may never have been seen before) are picked up, scanned and placed in collated orders. This is a level of sophistication built on top of automatic pallet stackers, warehouse flow optimisation, and mobile robotic automated storage and retrieval systems. Together, these fundamentally empower the low click-to-ship time and the very low error rate, at a cost that makes the service accessible to everyone in the developed world.
In my experience, a technically successful automation solution may be rejected by the end-users of that solution, so it’s vital that key assumptions are tested with those end users. We experienced this in a recent client project, which led to us recommending a bold new option. This new option would be powered by AI learning techniques. It would help predict user consumption and recommend adjustments to production lines, it would also add further robotic elements so that variations could be made to each line item. In common with many automation challenges, this is not a simple economic case, but it is a challenge which many major players in that industry will be considering taking to maintain their market dominance.
It’s not uncommon for the timescale to implement AI and robotics systems to be underestimated. Last year, as the heavily automated Tesla production lines struggled to reach their output targets (and a small army of early adopters waited for their Model 3…), Elon Musk admitted that "Yes, excessive automation at Tesla was a mistake. To be precise, my mistake. Humans are underrated".
It’s often necessary to take small steps to building confidence in a technical solution and its economic case. But the net effect of these many small steps can be substantial industry transformation over a period of say five to ten years.
The most exciting transformations from combining AI and robotics extend beyond industry and into every person's life. Macro social and economic changes that will range from the secondary impacts of self-driving cars (think about how real estate value could be redistributed) through to a new era of personalised, even faster convenience food which is autonomously prepared. Imagine a health revolution driven by greatly improved accessibility to nutritious, freshly prepared, delicious meals.
Combined AI and robotics projects should always start by understanding their resultant economic and social impact. Just because we could automate something, should we automate it? The answer to that question will largely determine whether a project will be accepted and ultimately if it will succeed.
The content & opinions in this article are the author’s and do not necessarily represent the views of RoboticsTomorrow
Comments (0)
This post does not have any comments. Be the first to leave a comment below.
Featured Product
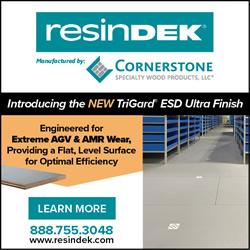