Robotic sight and machine vision systems can help our automata pick up on visual cues that we humans would probably miss or ignore, and they can deliver considerable value to companies that adopt them. Here’s a look at where the technology has been and where it’s headed.
The Evolution of Robotic Sight and Machine Vision Systems
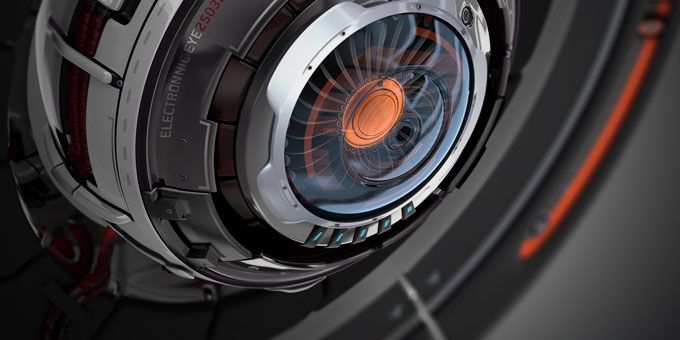
Kayla Matthews | Productivity Bytes
Some of the robots in our science fiction can hear x-rays and smell gamma radiation. Others look like they have standard incandescent light bulbs for eyes.
Today’s reality sits somewhere in the middle. We don’t have truly humanlike machines yet, but we do have machines that are better than humans in some key ways.
Machine vision technology has come a long way over the last few years, and it remains a gatekeeper to even more advanced robotics in the future.
Robotic sight and machine vision systems can help our automata pick up on visual cues that we humans would probably miss or ignore, and they can deliver considerable value to companies that adopt them.
Here’s a look at where the technology has been and where it’s headed.
How Robots ‘Evolved’ Better Sight
First thing’s first: What’s machine vision? Machine vision systems, also called “robotic sight” systems, provide the means to automate the detection of defects and automatically verify that proper assembly and tracking protocols have been observed within a manufacturing environment.
A concept known as “3D vision” is perhaps the most important breakthrough that made this quality possible. 3D vision gives robots a more complete understanding of their environments thanks to combinations of sensors, cameras and pathfinding software.
It also lets robots take unexpected variables “in stride” better, helps machines work more safely alongside humans and enables these machines to perform new tasks on the fly without constant reprogramming. Machine vision isn’t just about “seeing” — it’s about total spatial awareness.
It’s also about the fine details. Whereas human inspectors once had to touch and individually verify each workpiece as it came off the line, automated inspection stations have changed everything about the process. Now, products can automatically flow directly from assembly to inspection, where cameras and other imaging technologies view each side of the product and pinpoint flaws incredibly accurately.
This technology has had to tackle several specific challenges over the years, many of which had to do with unpredictable or unideal work environments that impacted the accuracy of the instruments. These issues typically included lighting conditions, product surfaces without discernible textures and products that may not be 100% stationary due to vibrations or other activities. Lighting is an especially important variable and must be precisely maintained if you want consistent inspection results in machine vision.
Previous incarnations of robotic sight and machine vision were also limited by onboard data processing capabilities. Robotic inspection stations may detect what they perceive to be a manufacturing flaw in an outgoing workpiece, but knowing for sure requires edge computing capabilities.
Sending inspection data for each workpiece to a server or service would slow the inspection process to a crawl. Instead, robotic vision systems have become a part of the Industrial Internet of Things, carrying out analyses on product data as close to the source of that data as possible. This change takes care of the latency and bandwidth problems that have held back robotic inspection technologies until fairly recently.
Where Is Robotic Sight Today?
The questions now are, “Where are robotic sight and machine vision today?” and “Why is this so important?” Let’s answer the second question first.
Robotic sight and machine vision are important for the same reason general computing is important: because computers simply perform some tasks more completely and accurately than humans.
And in a world where we must mind our resources more conscientiously than ever, that level of accuracy is non-negotiable when it comes to cutting down on wasted materials and efforts. In other words, robots are the better choice for carrying out inspections because they’ll miss fewer defects than human eyes.
Robotic sight and automated inspections can improve results throughout an entire enterprise too, and not just within a single facility. Although edge computing enables local data analysis and preserves bandwidth, joining machine vision inspection with cloud-based enterprise planning can help multiple facility locations compare data in real-time and improve their inspection processes.
We’ve focused so far on the role of machine vision in product inspection, but this technology also has implications for keeping our other machines in good repair and working efficiently.
One German company called PSI Technics developed a machine vision system that automatically conducts inspections, gathers benchmarks and studies and records damage aboard trains. When human workers perform these duties, it means making observations and taking recordings along, in some cases, several hundred meters of train cars.
Projects like these carry implications that will be felt throughout each of our industries. Machines that can proactively monitor themselves for maintenance issues and potential failures will keep our manufacturing and distribution processes humming along with limited downtime. And when we can eliminate human fallibility from important processes, defect rates will drop, and profitability will soar.
Realizing the Benefits of Robotic Sight
The concept of the “cost of quality” is an important one. Whether a defect has left you with a failed product and an incensed customer or you want to make sure your critical assembly equipment is never offline when you need it, robotics can keep their eyes on the most important parts of your business.
Machine vision isn’t free, but you can expect over time that this technology will lower your cost of quality and remove some of the burden of keeping your customers and clients happy.
The content & opinions in this article are the author’s and do not necessarily represent the views of RoboticsTomorrow
Comments (0)
This post does not have any comments. Be the first to leave a comment below.
Featured Product
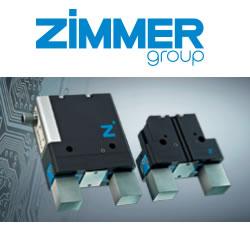