Rapid innovations in smart robotics providing high potential and different features are proving to be useful in decreasing human efforts and improving productivity.
Advanced Smart Robots: the Key to Ease Human Efforts & Boost Productivity
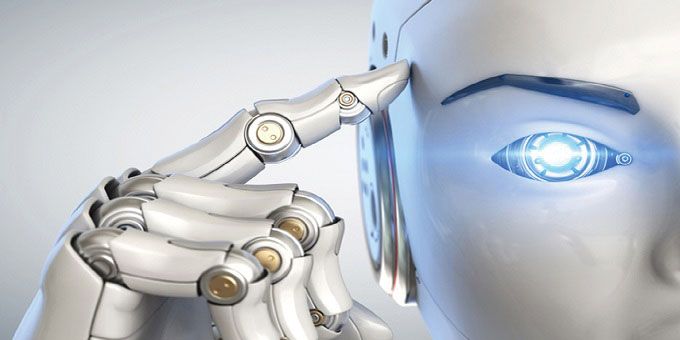
Research from | Allied Market Research
Rapid innovations in smart robotics providing high potential and different features are proving to be useful in decreasing human efforts and improving productivity. Artificial Intelligence (AI) system used in smart robots has helped the robots to learn from its environment and its experience. In the future, the collaboration of robots and humans could be helpful for major developments.
Recently, a prototype of a robotic ant was launched by the Swiss research institute in collaboration with the University of Japan. Moreover, a research team from the University of Cambridge has developed a robot to harvest iceberg lettuce that will be helpful for rectifying problems such as agricultural labor shortage and food wastage. An assistant professor in IIT Indore has introduced a polymer-based noiseless robotic jellyfish. Such rapid launches of novel robots are expected to boost the growth of the global smart robot market. According to a report by Allied Research Market, the global smart robot market is expected to value at $4.06 billion in 2017 and is estimated to reach $17.56 billion by 2025, registering a CAGR of 19.6% from 2018 to 2025.
Tribot: A high potential robotic ant.
EPFL, a Swiss research institute and Osaka University in Japan have united to create a robotic ant called Tribot. The trap-jaw modeled Tribot weighs around 10 grams, with features such as communicating with each other with the help of the infrared and proximity sensors. Moreover, the robots assign roles to themselves as leader and worker and complete tasks together as the ants do in their colonies. They are made of foldable thin material and are easy to manufacture. Additionally, the robots can navigate uneven surfaces as they can jump and crawl, and can lift comparatively heavy objects. Tribot has a good power in acceptance that can be useful for various purposes, including emergency relief situations and investigation missions. Besides, Tribots can be replaced among themselves if one in the group breaks down or malfunctions.
As per the researchers, every Tribot has an in-built battery and sensors that inform them about the obstacles in their way. This helps the leader ant to let the other ants know about the obstacle before moving ahead. However, Tribot exists only as a prototype.
Vegebot: A machine-learning navigated the robot
A research team at the University of Cambridge has developed and examined a machine-learning navigated robot named Vegebot to acknowledge and harvest iceberg lettuce. Since lettuce is easily susceptible to external damages and grows leveled to the ground, it creates a challenge for robotic harvesters.
The Vegebot is composed of two elements: a computer vision system and a cutting system, each integrated with a camera. The upper-head camera in the robot captures images of lettuce field and then one-by-one examines whether the crop is ready to harvest. The team has trained the machine by learning algorithms by providing images of different stages of lettuces as examples. The second camera stays near the cutting blades to have a smooth cut. While, cutting the lettuce, the force of the grip by the robots can also be adjusted accordingly. Furthermore, the robot has been tested successfully in different fields with different weather conditions, cooperated with G’s Growers, local fruit and vegetable co-operative. With this novel robot, the researchers aim to help in agriculture with labor shortages and for reducing food wastage.
Shape Memory Alloys (SMA) polymer-based and noiseless robotic jellyfish:
An important role is played by Bio-Inspired robots in invigilating different bio-diversities including marine life. However, due to its complicated mechanism, it faces certain limitations, for instance, the use of noisy motors that disturbs the marine life. To solve such issues, DR. IA Palani, the head of the Mechatronics and Instrumentation Laboratory and assistant professor of the Mechanical engineer at IIT Indore has introduced an (SMA) polymer-based and noiseless robotic jellyfish.
According to Dr. Palani, the soft robotics is a rising area in the field of robotics that challenges engineering thinking. He added that SMA can be a good alternative for flexible actuators technology to imitate same gesture as of the living organisms. It is a smart machine that can induce distort and revert to its memorized shape on heating. The robot has been tested in the laboratory environment with an achieved motion of 1 cm/s. The machine uses an SMA spring-based mechanism for moving. Soft robots allow noiseless activation and its simple design requires less time for its fiction. Moreover, the continuous heating and cooling of the polymer help contraction and expansion of its body with tentacles, that pushes the robot to move under the water. The researchers are working further to develop the SMA actuated autonomous bio-inspired soft jellyfish, to be used for transfer and rescue operations during floods. The robot will be useful for studying the behavior of marine species, spying unwanted threats via water resources, and to know the behavior of coral reefs, added the founder.
Such new inventions providing novel ways to lessen human efforts are helpful in every aspect, including industrial, agricultural, and educational fields. These technologies will provide a good increase in productivity. The manufacturing cost limits the market growth, whereas the rise in developments of different fields, provides ease to human efforts and labor-ships. This proves to be helpful and leads towards growth in opportunities for the market.
The content & opinions in this article are the author’s and do not necessarily represent the views of RoboticsTomorrow
Comments (0)
This post does not have any comments. Be the first to leave a comment below.
Featured Product
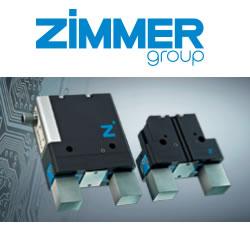