The Zimmer Group development team also faced a tremendous challenge in developing special gripper fingers, which were intended to handle any potential type of bottle from 0.33 l up to 0.75 l by gripping the neck and body of the bottle.
Robofill 4.0 – Robot and Gripper-assisted Filling Concept for Customized Bottle Supply
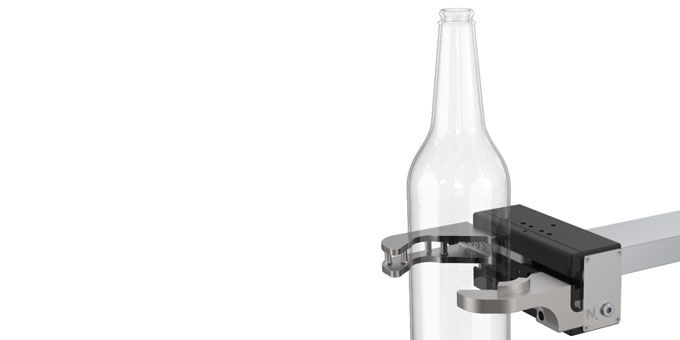
Case Study from | Zimmer-Group USA
Trending toward customization
The trend toward customization and personalization of mass products is showing no signs of slowing down. In addition to the automotive and pharmaceutical industries, this trend is gaining traction in food production. In the course of this mass customization, one of the primary challenges of this development with respect to personalized production currently lies in the fact that the consumer world is so closely connected to the world of production. At this point in time, general production has yet to be designed so that it can ensure the requested flexibility in volume and format in a way that is economical and sustainable. Of course, there are already some personalized foods (e.g. from Coca-Cola, Kinderschokolade etc.) on the market. However, primarily in the beverage industry, the production and process control structures that companies have been using are rapidly exhausting their potential.
RoboFill 4.0 – Completely new, flexible concept for filling and beverage technology
Wide-ranging possibilities are emerging as part of Industrie 4.0 for producing individualized mass products in the future that are both highly customizable while remaining profitable. This problem brought together professors of brewing and beverage technology as well as those of food packaging technology at the Technical University of Munich with Fraunhofer IGCV and the industry partners Krones, Beckhoff, ProLeiT, Siemens, Dekron, Yaskawa Europe, the State Brewery Weihenstephan and infoteam Software. All parties worked alongside each other to come up with an innovative automation concept. RoboFill 4.0, as the project has been dubbed, is a concept for filling and beverage technology that is completely innovative, versatile and makes it easy to add more production modules. The purpose of this concept is the industrial supply of customized beverage bottles or packages. The focus is on having lot sizes in small batches down to even single units. According to project specifications, all plant components were to be configured as cyber-physical system components. This is a core principle of Industrie 4.0. The idea is that the components use network and cloud technologies to communicate continuously with each other and with higher-level systems. This makes it possible to achieve autonomous production control, while also laying the foundation for using numerous optimization processes in production technology (e.g. predictive maintenance).
Zimmer provides sealed special servo grippers for bottle handling
When the gripper specialists from Zimmer Group were asked to take part in this exciting project of the Bavarian Research Foundation, the answer was an easy "yes". The Rheinau-based company – known for its trailblazing spirit and inborn ingenuity – made a very conclusive decision to take on this unique challenge. However, everyone involved realized quite early on that the project would not be a walk in the park. The list of impending challenges kept getting longer and longer as the problems were delved into. And throughout the first year of the project, the project partners kept adding more requirements to the list.
Developing the right gripper for handling various glass bottles and with robots turned out to be highly complex and costly. Putting everything into practice meant that concepts from different areas were interconnected and all had to be taken into account, including force-controlled gripping, sealed components, using exclusively food-safe materials and lubricants (NSF-H1) and making the grippers communicate with the robot control system. Furthermore, it had to be ensured that handling the glasses would not result in any of them being broken in case the plant underwent an emergency stop or power outage. The Zimmer Group development team also faced a tremendous challenge in developing special gripper fingers, which were intended to handle any potential type of bottle from 0.33 l up to 0.75 l by gripping the neck and body of the bottle.
Fig. 1: Sealed servo grippers with specially developed gripper fingers for handling bottles
It soon became clear that there was only one electrical gripper from the latest generation of the Zimmer Group (GEH6000 series with servo drive) that was suitable for this application. The problem was that this gripper was only available as a prototype at the time and it had not been designed for many of the requirements previously mentioned. It is enormously complex to seal such a compactly designed electrical long stroke gripper in such a way that it can be cleaned with a spray of soapy water, or to make sure that a bottle bursting will not lead to a system failure due to a short circuit. Several development loops had to be carried out. In these loops, we took the knowledge gained in elaborate tests and applied it to the component geometry and the process for coating the components, as well as to the materials used for the various installed seals and wipers.
Developing a special gripper-controller interface (HMI)
This solution can be described as a groundbreaking innovation that eliminates communication problems with the robot control system. Unlike the conventional solutions, this solution does not feature a second control system operating in parallel for the grippers operating with IO-Link. Instead, an in-house gripper-controller interface (HMI) was developed and integrated into the robot control system. "At this point, we wish to extend our sincere thanks once again to Yaskawa for their excellent collaboration on this project. By implementing the Zimmer HMI into the robot control system, many industrial robots now feature the option to control as many as four electrically or pneumatically driven Zimmer grippers," says Erik Bauhaus, Project Coordinator and Developer M-TB at Zimmer Group, of the successful collaboration with the robot manufacturer.
Fig. 2: A look at the control panel of the robot (Zimmer HMI)
To keep development time and costs for the gripper fingers as low as possible, they were designed in advance using FE analyses and then additively manufactured in a 3D-printing process.
Fig. 3: Visualizing an FE results analysis for the gripper fingers
A similar approach was taken in developing the bottle carrier for the Beckhoff XTS system. Here, the many years of experience and thorough customer care and support offered by the Zimmer Group paid dividends – particularly in developing special customer-specific solutions. For instance, this made it possible for employees to draw upon their extensive experience with using food-grade lubricants. The in-house prototype creation and the option to start carrying out complex tests as early as the R&D stages were both significant factors in making sure this project succeeded.
The test system was commissioned at the end of the project at the State Brewery Weihenstephan and is being tested extensively over the next few years for market-readiness and suitability for everyday use. These efforts might even one day make it possible to sell the complete system. Inquiries on this have already been voiced in the past.
The content & opinions in this article are the author’s and do not necessarily represent the views of RoboticsTomorrow
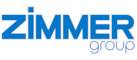
Zimmer Group US, Inc.
Are you interested in premium products in the fields of mechanical and plant engineering? Do you want to learn more about our solutions in the fields of automation, damping, linear, processing, tooling, and machine tooling technology?
Other Articles
Automate 2025 Q&A with Zimmer Group
Converting Passenger Aircraft to Freight Aircraft - the Zimmer Group Is on Board!
Automated Loading and Unloading of CNC Machines
More about Zimmer Group US, Inc.
Comments (0)
This post does not have any comments. Be the first to leave a comment below.
Featured Product
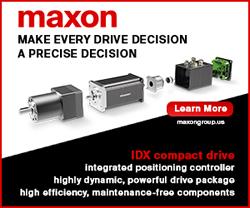