Mobile robots, in the form of AGVs, have been on the market for nearly two decades. But a topical innovation in the sector is creating power requirements that the battery market must respond to.
Battery Requirements for Next Gen Mobile Robots
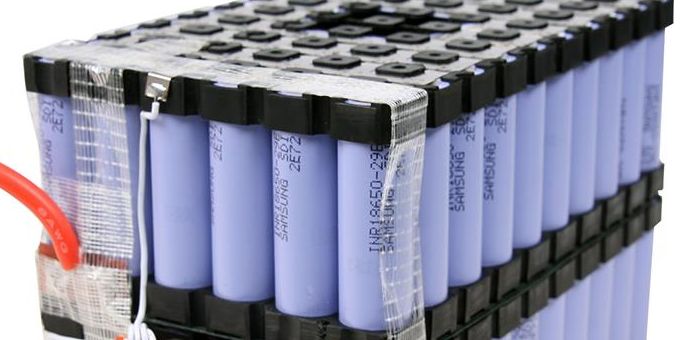
Michele Windsor | Ultralife Corporation
Once, mobile robots were limited to warehousing and logistics roles. But advances in the collaborative robot market have introduced production ready mobile robots with payloads of over 1000 lbs. This has been a game changer for companies like Kuka, Omron and Clearpath, who have already introduced very advanced systems, with installed applications across North America, Asia and Europe.
Robots such as Kuka's KMR iiwa and Clearpath's OTTO are best thought of as AGVs with autonomous navigation and a conventional six axis robot mounted on them, allowing the machine to be continually redeployed around the plant. Often fitted with crane-like feet, allowing the robot to fix in place, and provide the stable platform required for accuracy and respectability.
The autonomous nature of modern mobile robots is another game changer. Conventional AGVs follow tracks around the plant, which can be very old-fashioned tram-style magnetic lines or very advanced honeycomb-style high speed systems.
But autonomous robots can respond to their environments and make on the fly decisions about how they navigate a plant. The former are like buses, reliably following a single route, while the latter are more like Ubers — actively changing direction and purpose as required.
Allowing AGVs to be freed from mains supply are portable power solutions like batteries. Again, there are a couple of different options available for charging the batteries; opportunity charging or battery exchange strategy. Opportunity charging requires AGVs to work in shifts, returning to a charging station several times a day. Battery exchange on the other hand is ideal for getting an AGV back into action quickly, as the battery can be substituted with a fully charged one either manually or automatically.
Choosing the best option depends on the layout and requirements of the warehouse in which the robots will be used. As AGVs increasingly become tailored to their environments, it is no wonder that autonomous mobile robots were one of the key themes at 2019’s Automate trade show in Chicago. In fact, the trend was so significant that the next Automate show, due to be held in Detroit in 2021, is expected to be dominated by a new generation of mobile robots.
Yet as more co-bot mounted AGVs enter the market, it is important to remember that quantity does not always mean quality. Generally speaking, the AGV base and the industrial robot running on it use the same battery. As a result, an AGV that might have a run time of twelve hours can find that run time cut in half.
This shouldn't provide a health and safety issue, because the robots currently on the market freeze in place on interruption, rather than attempting to return to a specifically defined starting position.
However, this could present a problem as more robots are introduced to the market by start-up or less reliable manufacturers. The danger is that future iterations may not share that safety backup.
The rapidly changing world of robotics, where mounted mobile robots were a fiction just a few years ago, means that battery manufacturers have to develop just as rapidly and be as flexible as our robot OEM counterparts. We've achieved this at Ultralife Corporation with our custom design and manufacturing service, which allows us to work with mobile robot manufacturers to deliver exactly what they need, to suit their requirements — from footprint to volume power density.
About Michele Windsor
Michele Windsor has worked in the battery industry for nearly a decade and has produced countless white papers and guidance documents on the subject. To find out more about Ultralife's robot battery offering, download the company's robot battery guidance document here.
Editors Recommendation "Artificial Intelligence Drives Advances in Collaborative Mobile Robots"
The content & opinions in this article are the author’s and do not necessarily represent the views of RoboticsTomorrow
Comments (0)
This post does not have any comments. Be the first to leave a comment below.
Featured Product
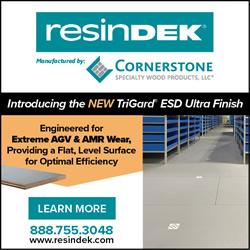