Air cargo facilities are undergoing rapid digital transformation via the adoption of automation technologies. - the most recent one being fully autonomous drones. At the leading edge of this innovation in inventory management is IAG Cargo.
British Airways Deploys Drones For Inventory Counts At Its Air Cargo Company
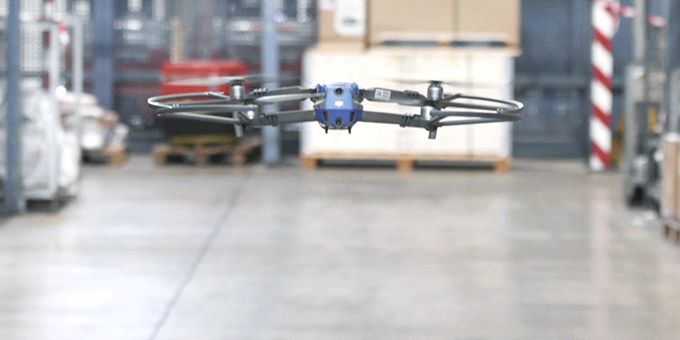
Case Study from | FlytWare
Air cargo facilities are undergoing rapid digital transformation via the adoption of automation technologies. - the most recent one being fully autonomous drones. At the leading edge of this innovation in inventory management is IAG Cargo, part of the same group that owns British Airways. With a vision to fully automate inventory counts at its air cargo facilities, IAG Cargo has been working closely with FlytBase on aerial inventory scans at its Madrid facility.
Inventory counting, while a critical business activity, consumes thousands of man-hours each year across IAG Cargo’s hubs in the UK, Spain, and Ireland. Increasing the frequency of such counts, a necessity in the age of global e-commerce and same-day delivery, is important - but impractical if done manually. Drones, however, can make this a reality - thanks to cost-effective hardware, intelligent automation software, and continuing advances in indoor autonomous navigation using machine vision and AI/ML techniques - all packaged in the form of FlytWare, an autonomous aerial inventory scanning solution from FlytBase.
FlytBase’s engagement with IAG Cargo involved stakeholders from innovation, continuous improvement, warehouse operations, inventory management, digital transformation, and business analysis. After prioritizing the key requirements for aerial inventory counts, FlytWare was trialed and tested carefully by running dozens and dozens of indoor drone flights - the barcodes thus scanned were automatically mapped to their locations; making available the ‘ground truth’ data that could then be filtered for empty slots, compared with WMS data and analyzed for location accuracy.
Having thus been tested at IAG Cargo via proof-of-concept trials, and further refined during the pilot project, FlytWare is now being readied for production deployments at multiple IAG Cargo facilities. The reality of inventory management is that each warehouse, distribution center, and air cargo facility is unique in terms of storage configurations, key operating metrics, cycle count frequency, etc. Scanning one-deep, front-facing bar codes on full pallets is obviously much simpler than counting case reserve in VNAs, scanning pallets stored in bulk areas or enabling automatic ‘first counts’ of multi-deep pallet/case reserve that are then followed by manual ‘second counts’.
Nitin Gupta, CEO, FlytBase, explained: “Flytware’s trials at IAG Cargo have been successful in uncovering the significant opportunities and key challenges of deploying fully autonomous drones for inventory counts in warehouse rack storage. Not only can aerial inventory scans provide cost-effective and high frequency cycle counts, but they can also measurably impact productivity and support regulatory audits. The availability of live video feeds and location-wise image data, coupled with capabilities such as precision landing and WMS integration make FlytWare a highly compelling alternative to not only manual counts, but also RFID, AGVs and other methods that remain expensive and difficult to scale. Needless to say, we look forward to deploying FlytWare across IAG Cargo, a leading advocate for aerial inventory counts.”
The trials of FlytWare at IAG Cargo’s Madrid warehouse have also reinforced the importance of user-friendly operator dashboards, auditable inventory data and live video feeds. These underpin the intangible benefits of drone-based barcode scans - in addition to the time, cost & safety benefits versus manual counts. In fact, from a safety perspective, the ability to detect and avoid obstacles during autonomous flights turned out to be a key success factor for adopting FlytWare - even though the SOPs may require that the aisles be closed off during drone flights.
In an age of high-velocity supply chains and consumer expectation w.r.t. instant delivery, automation is becoming the silver bullet for inventory stakeholders at air cargo facilities - with fully autonomous drones expected to play a central role.
If you like this article you may like "Is Software the Future of Robotics?"
The content & opinions in this article are the author’s and do not necessarily represent the views of RoboticsTomorrow
Comments (0)
This post does not have any comments. Be the first to leave a comment below.
Featured Product
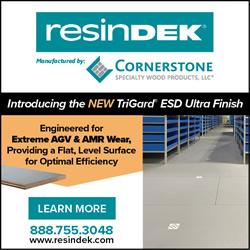