Today’s plant managers are faced with a dearth of automation technologies but it’s not always obvious what will work best. There is rarely, if ever, a one-size-fits-all approach.
Robots or Cobots: Which to Choose?
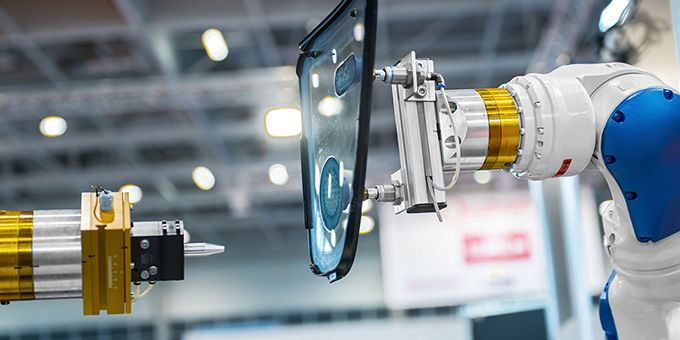
Jonathan Wilkins | EU Automation Inc.
If it wasn’t already clear to manufacturers that the adoption of robots is on the rise, the numbers leave little doubt. The International Federation of Robotics predicts that by 2020, over 1.7 million new industrial robots will be installed in factories worldwide.
Industrial robots have long been used to replace human workers in performing tasks that are dangerous, dirty or repetitive. These robots are often large and bulky, caged machines used to do the heavy lifting in applications such as packaging and palletizing.
Collaborative robots, otherwise known as cobots, have been designed to work safely alongside humans in a shared workspace. These robots, with their increased flexibility and dexterity, can complete more delicate tasks that conventional robots cannot, such as polishing fragile materials in the production process.
Cobots
Cobots were built to be smaller, lighter and safer than conventional industrial robots. Demand for this technology is on the rise, with the global cobot market expected to reach $9 billion by 2025.
Because of their flexibility, and relative ease of use compared to fully automatic robotic systems, cobots are generally considered to be an affordable and attractive choice for small and medium sized businesses. These manufacturers can benefit from the traditional value proposition of robots — namely that they can carry out repetitive or unsafe tasks, freeing up human workers to add value — but at a much lower cost of entry.
Before investing in cobots, it’s important that manufacturers carry out a complete and thorough risk assessment. Risk assessments could call for the addition of extra safety features, low operating speeds or even multiple stops for a cobot. Furthermore, these extra considerations aren’t free and add a significant amount to the integration costs.
In fact, according to TM Robotics’ Global Robotics Report 2018, 79 per cent of automation distributors don’t think that their customers fully understand the safety requirements of installing a cobot, and therefore are unlikely to budget for these additional safety features.
Editors Recommendation "Artificial Intelligence Drives Advances in Collaborative Mobile Robots"
Safety first
The ISO 10218 guidelines exist to set the safety requirements for industrialized robots. However, for cobots, which will see an increased number of interactions between human and robot, these guidelines alone don’t suffice.
First introduced in 2016, the ISO/TS 15066 guidelines supplement the ISO 10218 requirements and ensure that any machines classed as collaborative meet specific safety requirements. This also includes any tools that have been adapted onto the robotic arm to perform tasks as well as any objects handled by it. For the first time, ISO/TS 15066 outlines the maximum allowed power and speed limits for cobots. It also brings increased clarity on what is necessary when carrying out risk assessments on cobot applications.
The risk assessment must consider the entire collaborative workspace and look at how the operator will interact with the robot. Manufacturers must take the time to ensure they properly risk assess all foreseeable contact situations that could arise between the operator and cobot for any job that the robot is expected to complete.
Engineers need to carefully assess every task that the robot will complete in detail — an oversimplified assessment will not accurately represent how safe the robot will be. Here, manufacturers should consider the safety concept of ALARA (as low as reasonably achievable). Manufacturers must consider all the potential risks that could arise in a robot application, not just one or two of them.
Industrial robots
Manufacturers also need to consider the production speed and volume that they are looking to achieve when deciding between cobots and traditional industrial robots. To run efficiently, an assembly line comprised of both humans and cobots must run at the speed of human operators to avoid bottlenecks on the production line.
Manufacturers in sectors such as bottling or packaging, that need a much higher production speed or volume, can benefit from purchasing conventional robots. The logic is simple. Fewer human operators means there is less chance to slow the system down and production will increase. Multiple industrial robots can be integrated for a fully automated production line.
Industrial robots are automatically controlled and are programmable in three or more axes and they can automate an extremely broad range of processes unattended. Crucially, programming of these machines is easy, so operators don’t need to have advanced programming skills to use them. These robots can make use of AI software and machine learning to pickup processes and improve on them – self-coding their programmes when necessary.
Upgrading a factory to make use of cobots alongside existing legacy equipment and the human workforce is an attractive proposition for many businesses but it is one that requires selective investments and careful obsolescence management.
The widespread growth in the cobot market illustrates the fact that cobots are an ideal first step towards automated manufacturing processes. The initial investment is low in applications that don’t require guarding to be installed. However, for large, complex manufacturing setups, full size industrial robots may still offer better economies of scale.
EU Automation stocks and sells new, used, refurbished and obsolete industrial automation spares. Its global network of preferred partner warehouses, and wholly owned distribution centers, enables it to offer a unique service within the automation industry, spanning the entire globe. It provides worldwide express delivery on all products meaning it can supply any part, to any destination, at very short notice.
If you like this article you may like "Smart Gripper for Small Collaborative Robots"
The content & opinions in this article are the author’s and do not necessarily represent the views of RoboticsTomorrow
Comments (0)
This post does not have any comments. Be the first to leave a comment below.
Featured Product
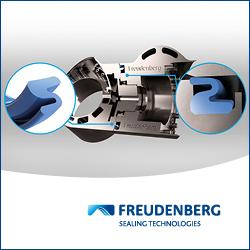