The Internet of Robotic Things (IoRT) is a rapidly evolving technology. In just a few decades, industrial robots have become commonplace in factory settings across the world, and they only continue to gain popularity for their productivity and profitability.
The Internet of Robotic Things: How IoT and Robotics are Evolving to Benefit the Supply Chain
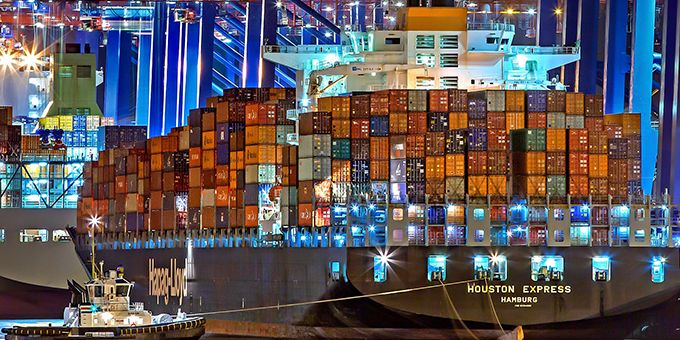
Stefan Spendrup, Vice President of Sales Northern and Western Europe | SOTI
Robotics have created a revolution in manufacturing. The cooperation between robots and IoT technology have enhanced supply chain operations, reducing the challenges of rising e-commerce demands and warehouse worker shortages, and streamlining industry processes in a more efficient and cost-effective way.
Robotics have long been successful in several structured industrial applications, due to their high level of accuracy, precision, endurance and speed. And while robotics have largely become more affordable in recent years, during the early stages of implementation in the supply chain, there was a high cost factor, which meant robotics needed to be evaluated and integrated correctly to avoid jeopardising their value.
In order to achieve the best possible return on investment (ROI), at the fastest rate, businesses must have a strategy to integrate any new robotics technology with all other IoT endpoints to ensure the entire supply chain is secure and operating seamlessly, to avoid system interruptions or loss of revenue, and gain valuable data insights.
The proliferating trend of automation sweeping across the globe has meant that from 2020 to 2022, almost two million new units of industrial robots are expected to be installed in factories around the world. In fact, Europe has the highest robot density globally, with an average value of 114 units per 10,000 employees in the manufacturing industry alone.[1]
The supply chain IoRT revolution
IoRT is a concept in which intelligent technology can monitor and manipulate the events happening around them by fusing their sensor data and making use of local conditions to decide on a particular course of action of how to behave or control objects in the physical world.
Manufacturing and transportation and logistics companies have been pioneers of today’s IoRT revolution, leading the way to connect and automate industry operations. Given the complex nature of the supply chain, the use of robotics helps to streamline operations by developing process-driven automated functions, simplifying processes and working at a tireless pace to meet ever-increasing demands. What’s more, they are not restricted by the weight capacity of humans, nor do they have a limit to their energy levels. With today’s trend of fast delivery services and an influx of increasing e-commerce traffic, robotics is a smart way for businesses to keep up with current consumer demands and expectations.
Today, most tasks that are crucial to the supply chain, including the movement of products from within a warehouse or distribution centre, rely heavily on robotic technology to achieve the maximum level of efficiency and accuracy needed to meet demands. An example of this would be Automated Guided Vehicles (AGVs), which are quickly becoming a staple in supply chain warehouses. Portable, automated and sensor driven machines, AGVs work to navigate the warehouse floor at a faster rate than any human worker, and they can work around the clock, seven days a week. By speeding up operations and removing the chance of human error, the integration of robotic technologies like AGVs is fast becoming the key to increased supply chain productivity.
Implementing robotics for a ROI
Supply chain businesses have been implementing and actively exploring IoRT transformation initiatives for some time, and research shows this uptake will only continue to grow in the future.
In the supply chain, the deployment of robotics focuses mainly on increasing productivity and lowering operational costs. However, in order to gain the highest value, supply chains must optimise their robotic systems as part of an all-encompassing supply chain strategy, not just in silos.
IoRT operations become most powerful when they are seamlessly connected to a centralised supply chain management system that connects the responsibilities of employees; aligning both managers and the IT departments to manage and optimise the use of all supply chain technologies and systems, including robotics.
When properly integrated, all supply chain business teams have access to real-time visibility of all connected endpoints and a wealth of data insights from the entire supply chain, including the performance and accuracy of the IoRT. This helps to enhance the use of robotics alongside other technologies and to rapidly uncover any robotics technical issues or inefficiencies. It allows technical support staff to act at the earliest possible opportunity, and in turn minimise the impact of costly slowed productivity or complete outages. Real-time insights provided by an integrated mobility and IoT management platform can help reduce the overhead costs of tasks, such as maintenance and program updates, by identifying system problems before they happen.
By enabling predictive maintenance for IoRT technology, it also becomes possible to make an evaluation on whether they are effectively achieving a decent ROI for the business.
There is no doubt that the use of robotic automation in the supply chain can boost both productivity and revenue. However, to guarantee the highest value from robotics investments, businesses must effectively converge business-critical IoRT and other IoT endpoints into a holistic and secure supply chain management ecosystem.
The content & opinions in this article are the author’s and do not necessarily represent the views of RoboticsTomorrow
Comments (0)
This post does not have any comments. Be the first to leave a comment below.
Featured Product
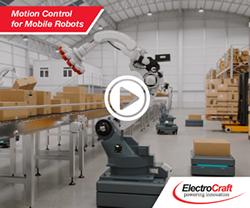