Manufacturers looking to enter or expand their electrification business often find themselves balancing key production requirements with the unpredictability of an emerging market where best-practice standards are still evolving.
Innovative Manufacturing Approach Reduces Costs and Optimizes Electrification Time to Market
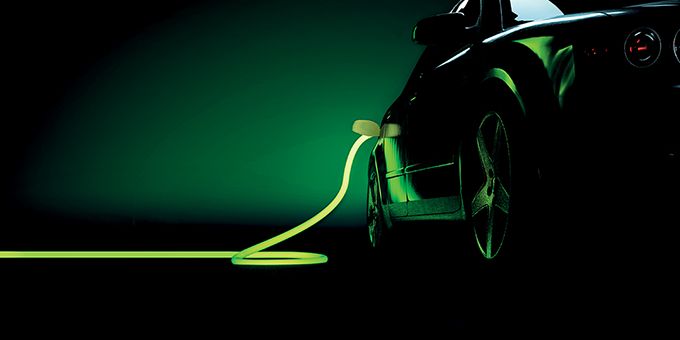
Ermanno Faccin, Head of Powertrain & Electrical Drive Unit - Assembly & Test | Comau
To meet these challenges, Comau is rethinking electrical motor and transmission assembly by fully integrating design validation, resin verification, rotor preparation/winding, and multi-model manufacturing flexibility as part of a functional, efficient and versatile operational philosophy. Backed by pioneering competencies in electrification and a 360° understanding of automotive manufacturing, the Italian automation leader has developed a strategic and straightforward approach to rotor and stator assembly that optimizes cycle times, eliminates resin compatibility issues, and can be easily integrated within pre-existing production lines.
The method starts with a fully integrated design phase. Often done in simultaneous engineering with the client, the team looks at the performance and product considerations before identifying the optimal combination of processes and technologies for the specific nature of the project. Looking at the electrical motor architecture evolution, many automakers in recent years have been investing in permanent magnet rotors and hairpin stators. At the same time, wound rotors continue to command an important share of the market both due to their performance and because the cost of retooling an existing line is often significantly less than investing in a new line. Another advantage of the wound rotor is its efficiency. Wound rotors enable better energy management due to the fact the magnetic field can be modulated by electronics management, whereas the permanent magnet rotor (PM/IPM) has a fixed magnetic field.
When building a slip-ring rotor there are several process considerations that must be evaluated carefully based on factors such as the motor design and projected production volumes. One of the key decision points involves the electric winding and impregnation phases, which directly affect the performance and life cycle of the assembled e-motor. Here, the choice of spindle, needle or flyer winding depends largely on comparing the wire management process, winding quality and the height and width of the rotor teeth. The first difference lies in the wire management process. With spindle winding the wire passes straight through a guide tube into the winding chamber and onto the outer flanges, which protect the wire from the side teeth, before reaching the layering flanges. The direct nature of this process means that the wire tensioner can manage up to 90% of the wire tension. Needle winding, on the other hand, requires that the wire first pass through the needle head, where it is bent 90°. It then enters the wire guide tube where after another 90° bend it passes into the winding chamber. Because the tension control is offset by the needle head, the tensioner only manages about 60% of the final wire tension.
Indeed, the wire tension, wire angle and ratio between the height and width of the teeth are three factors that can determine the uniformity of each coil layer. When comparing winding technologies, spindle winding tends to produce a more even wire distribution than needle winding due to its straight-line feed process. This is further aided by the good tension management and high reactivity of the tensioner. As the needle wound wire comes out of the wire guide at 90° and is already subject to stress, there is a greater possibility for the winding to become concave. At the same time, the tensioner is not fully able to control the final wire tension and there is a limited possibility to quickly pull the wire back during the different winding phases. These factors contribute to the risk of convex winding. Increasing the wire tension can reduce the distortion but will also increase the final Ohmic value.
Another consideration is the rotor’s mechanical design. Spindle and needle technologies require slightly different spacing parameters, which in some cases may favor or eliminate one of the two options. In spindle winding, the space between the teeth needs to accommodate both the layering flange and the wire itself (approximately 2.5 mm). The space required for needle winding is determined by the thickness of the wire guide tube. Generally speaking, this means there will be between 1.4 mm up to 3.6 mm of space between the teeth.
Comau’s experience in electrification gives us a unique ability to design efficient, high-volume, automated assembly lines for the entire e-motor assembly process. We do this by comparing different techniques, analyzing performance requirements and integrating different proprietary technology platforms within a fully automated manufacturing process. Furthermore, as a single-source provider, we harmonize the collaboration between specialists, technology companies and systems integrators to optimize the entire program rollout. The end result of our turn-key engineering offer is the assurance that production can be done in the most effective way possible, with reduced costs, maximum productivity and faster time to market.
About Ermanno Faccin
Ermanno Faccin leads the proposal team to support Comau customer’s needs by providing efficient manufacturing solutions in traditional and innovative industrial sectors as Head of Powertrain & Electrical Drive Unit - Assembly & Test. After graduating with a degree in Mechanical Engineering at Turin Polytechnic in 1995, with a specialization in industrial automation and innovative manufacturing systems, he interned with Comau in a European program dedicated to high-speed machining process optimization in the automotive industry.
The content & opinions in this article are the author’s and do not necessarily represent the views of RoboticsTomorrow
Comments (0)
This post does not have any comments. Be the first to leave a comment below.
Featured Product
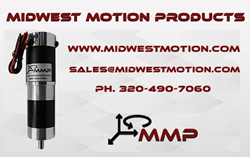