Many applications require drive solutions that have a central opening through which parts of the application can be guided. Examples of this can be found in optics and photonics for laser steering systems or in automation and robotics for semiconductor handling systems.
Triad of Torque, Speed and Precision. Applications? Step Into the Ring.
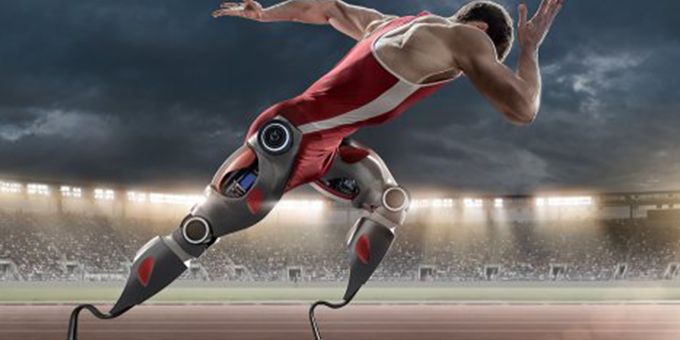
Article from | FAULHABER MICROMO
Until now, conventional systems always resulted in compromises here. The hollow shafts were often quite small, the drives slow, heavy or the mechanical integration required a great deal of work. A new direct drive now offers a promising alternative. Its large opening has a diameter of 40 mm and, thanks to stepper motor technology, achieves a balanced combination of speed and torque with low weight and volume.
There are many drive technologies and solutions available that are generally suitable in cases where a central opening is needed. In practical use, however, each has its own disadvantages. With hybrid stepper motors, for example, the diameter of the hollow shaft is usually limited to approximately 10 to 12 mm on account of the necessary copper filling factor or magnet yoke. Due to their multi-pole design, torque motors do permit larger openings, but cannot achieve high speeds due to their large moving mass. In addition, they are relatively expensive and often difficult to integrate. Many applications therefore use rotary tables with a central opening that are driven by a "normal" motor. Such solutions require transmission and complex mechanics, however. The resulting inevitable backlash needs to be compensated by means of elaborate measures before this type of motor can be used in high-precision applications. This complicates system integration considerably. Furthermore, numerous wear parts are involved, which leads to high maintenance requirements. Rotary tables actuated by a hybrid stepper motor, are likewise often the tool of choice, but have a large volume and are heavy when higher performance values are called for. Finding a practical solution when the application requires an opening has, thus, not necessarily been easy until now.
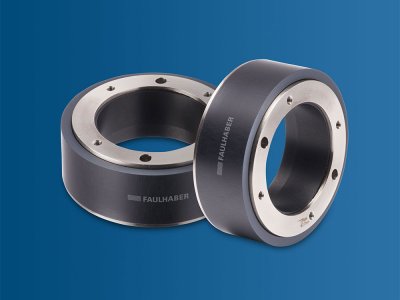
DM66200H
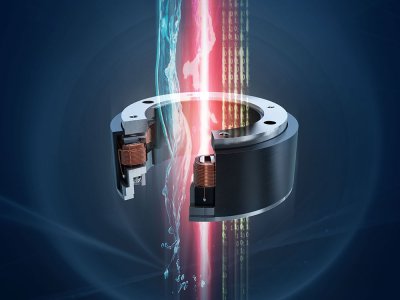
Ringstepper Visual
New approach – new possibilities
The drive specialist FAULHABER therefore took up this topic and developed an entirely new drive solution with the stepper motor of the DM66200H series, which is designed especially for applications that require a large opening. With a total diameter of 66 mm, it offers a very large hollow shaft inner diameter of 40 mm. And it is only 24 mm thick and weighs just 218 g. As a result, the compact drive is easy to mount and requires very little installation space. The rotor with the opening directly drives the mechanics, which are arranged around the opening and does so without transmission. As a result, there is no mechanical backlash that needs to be compensated for.
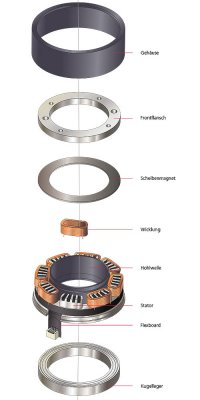
DM66200H Explosion
Originally designed for optics and photonics applications, the new hollow shaft direct drive also opens interesting possibilities in many other areas, such as wheel drives in cases where the drive shafts are guided through the motor for space reasons or in prosthetics with artificial knees or shoulders. In principle, it can be used wherever cables need to be guided through the opening or in cases where gases, fluids or light signals are to pass through the opening. Apart from the field of optics – e.g. for microscope stages, apertures, zoom lenses, laser beam controls, etc. – it can thus be used for a wide range of control and positioning tasks. Typical applications also include turntables, antenna feet as well as air and gas vents.
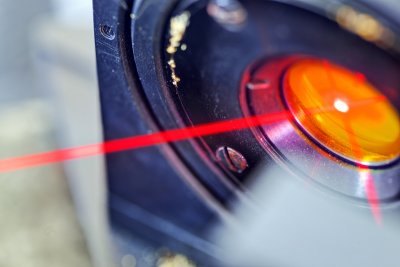
Optic Photonics Laser
High performance values in optimum combination
The direct drive is based on the proven stepper motor technology from FAULHABER. The multi-pole, two-phase motor with permanent magnets delivers 200 steps per revolution. With a high resolution of 1.8° in full-step mode, it can execute positioning tasks precisely in open loop operation. It achieves a dynamic torque of up to 200 mNm and can move correspondingly large loads. The maximum static torque is 307 mNm, and even 581 mNm when boosted. Brakes are thus unnecessary. Speeds of up to 2,000 revolutions per minute can be achieved. For many applications, the compact direct drive thereby offers a perfect balance of speed and torque. It enables maintenance-free continuous operation, as the only wearing part is the ball bearing. Application-specific modifications are possible on request, for example, specific lubricants, customer-specific windings, special cables and connectors as well as mounting flanges.
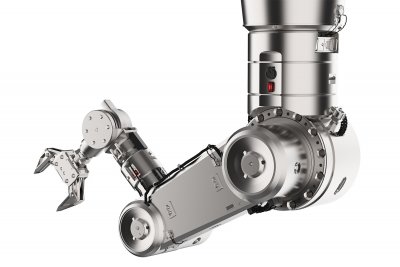
Robotic arm
Link to direct drive with very large aperture and high performances (faulhaber.com).
The content & opinions in this article are the author’s and do not necessarily represent the views of RoboticsTomorrow
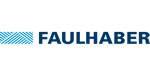
FAULHABER MICROMO
Since 1961, FAULHABER MICROMO has partnered with OEMs to deliver high precision, high performance, custom micro motion system solutions to markets such as medical, robotics and automation in North America. FAULHABER MICROMO's tradition of innovation started decades ago in Germany. The groundbreaking invention of the FAULHABER coreless winding started it all for a market that produces millions of motors today. How can the FAULHABER MICROMO team help you deliver your next innovation to market first? Learn more about MICROMO's solutions for the most demanding applications, our diverse motion products and technologies, online ordering, Engineering and R&D teams, Clean Room Assembly, Machining Center and other services at our Clearwater, FL facility at https://www.faulhaber.com.
Other Articles
Walking naturally with artificial foot
Testing drive systems virtually - Simulink library for development and digital twin.
At least 60 million strokes
More about FAULHABER MICROMO
Comments (0)
This post does not have any comments. Be the first to leave a comment below.
Featured Product
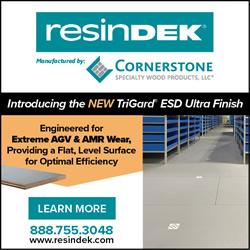