Technology advances in automated deep-freeze distribution have provided advantages for increased throughput, system uptime and a better ROI. Laser-guided vehicles, playing a pivotal role in this sub-zero technological evolution, have recently taken a quantum leap forward.
The Latest Evolution of High-Performance Laser-Guided Vehicles Streamlines Pallet Movement in Deep-Freeze Warehouses
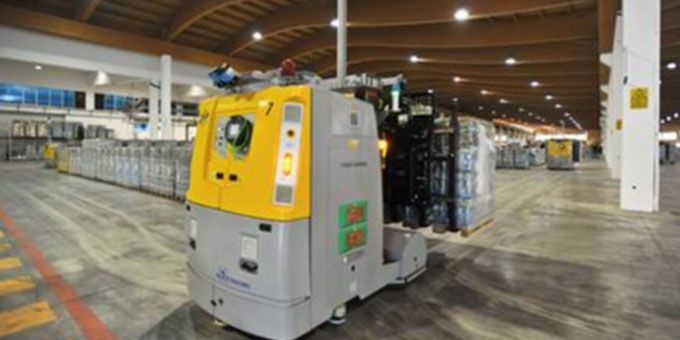
Jim McMahon for | Elettric80 S.P.A.
Deep-Freeze Challenges
Deep-freeze warehouse environments pose significant challenges for food processors, distribution centers and retailers who endeavor to have facilities operating at a high level of efficiency. The consumption of frozen products has increased dramatically, and rapid replenishment of retailers’ shelves is critical. Every aspect of deep-freeze warehousing is moving faster. Turnover of stock is faster, with an increasing number of products in the -4° F to -22° F range, and there is a need to respond quickly to market demands. Maintaining a high throughput rate, along with inventory and fulfillment accuracy is a much more difficult task than in an ambient-temperature or chilled warehouse.
While the temperature in these deep-freeze facilities is cold enough to store food products safely, it creates an extreme environment with difficult working conditions for personnel, increased safety issues, and staff recruitment and retention problems. Compared to non-deep-freeze facilities, most manually-operated sub-zero warehouses have a higher incidence of product damage, missed product rotation and wrong item fulfillment, which have negative impacts on production and cost efficiency.
Cold storage LGVs designed to handle various pallet types, with loads up to 3,400 lbs. (Elettric80)
Increasingly, frozen-food producers and distributors need to track and identify where each product lot originated, where pallets came from, where they were stored, what the temperature was in storage, and other critical data to keep track of their perishable inventory and ensure its product integrity. Manual handling leaves open the possibility of human error in recording and providing this data quickly, with reliable and verifiable documentation.
Automation in Sub-Zero Facilities
Automation of deep-freeze warehousing presents an optimum solution to these difficulties. The most streamlined deep-freeze warehouses today are highly automated sites, with material-handling systems that are engineered to function optimally under deep-freeze conditions. These include high-density storage utilizing robotic pallet shuttle systems and automated storage and retrieval systems, robotic picking and palletizing, smart modular conveying, and management systems capable of integrating all functions from receipt of materials, through production, end-of-line packaging, warehousing and shipping.
High-Performance Laser-Guided Vehicles
Critical amongst these automated systems are laser-guided vehicles, which provide for movement of pallets between these integrated functions. The use of LGVs has played a pivotal role in facilitating process and throughput efficiency in deep-freeze manufacturing and distribution operations. Interfacing with multiple systems, LGVs provide reliable raw material and product handling, with near zero potential for product damage.
LGVs accommodate single- and double-deep racking, and extended depths with satellite remote units. (Elettric80)
Utilizing a combination of logic software and wireless navigation, LGVs can perform tasks that are not possible with other transport systems – such as the uniform movement and positioning of pallet loads to within a fraction of an inch of their designated targets, without noise, and with a high degree of safety for workers and their operational environment.
Transporting heavy pallet loads, however, imparts huge forces upon these vehicles, resulting in significant maintenance and power requirements to keep LGV fleets functioning. The latest generation of LGVs, however, incorporates design, navigation, sensor, power and controls improvements that significantly streamline their prior operational performance.
An excellent example of these high-performance automated vehicles is Elettric80's latest forked, counterbalanced LGVs for pallet movement. Elettric80, a multinational leader specialized in creating automated solutions for companies that produce fast-moving consumer goods – in particular in the food, beverage and tissue sectors – has been a leading manufacturer of LGVs for almost three decades. Some of the company's latest technology advances have made LGVs particularly adaptable for deep-freeze environments.
Specially Engineered Materials and Components
Focusing on extreme cold temperatures down to -22° F, Elettric80's latest forked LGVs have been engineered to function optimally under these deep-freeze conditions. Specially blended steels, oils, greases and other lubricants for gearboxes, bearings and drives are specified for extreme low temperatures. Wiring and electrical cables are designed to flex in these temperatures. PLCs, PCs and other electronic control components are kept in heated cabinets. Photo-electronic sensors that feed computer information and detect pallets are maintained to be free from frost by being equipped with heating devices. Automated systems for deep-freeze need to be designed to include these features, not only so they can function reliably, but also for system longevity.
Battery Performance
A key factor in LGV operation, and particularly in deep-freeze environments, is battery performance. The most conventional power source used in LGVs has been, and still is, lead acid.
But lead is heavy, and these batteries require extensive maintenance, they are slow charging, and perform poorly in extreme sub-zero temperatures, making LGVs a limited technology solution for deep freeze.
Lithium flash battery technology, a better solution for LGVs in deep-freeze environments. (Elettric80)
Lithium ion batteries have changed much of this, however. A Lithium ion solution, for example, with the capability of putting out 140 amp hours (Ah) of power would weight about 150 pounds. Compare this to a lead acid battery putting out the same power, but weighing 700 pounds. A lithium ion phosphate battery will charge 4X faster, and deliver 4X the life compared to lead acid. Consequently, they are a better solution for LGVs in deep-freeze environments, but still lack the performance capability compared to operating in ambient or even refrigerated environments.
An even better solution for deep freeze is lithium flash battery technology, which was first introduced for use with LGVs by Elettric80, and remains a proprietary technology reserved for Elettric80 LGVs. Flash batteries provide higher performance than any other type of battery for industrial vehicles. With power output up to 300 Ah, they deliver 20 times faster balancing speed than other lithium batteries, and can be recharged to 50 percent in less than 30 minutes, compared to twice that time for traditional lithium batteries.
The control electronics in a lithium flash battery keep it balanced and efficient, eliminating the need for regular maintenance. It is also equipped with a remote monitoring system that enables the condition of the battery to be determined at any time, while reporting any malfunctions.
Only one lithium flash battery is required per LGV, compared to two or three batteries needed with traditional lead acid LGV applications.
With wireless induction flash battery charging, the battery stays in the LGV while charging. (Elettric80)
A very unique feature of this battery is wireless induction charging. In fact, the battery stays in the LGV while charging with no connecting wires. The LGV does not even have to leave the deep-freeze environment to be recharged. The implications of this are considerable – reduced time for not having the LGV leave the facility, and for not having to switch out the battery; and no connection sparks from cable connecting, improving safety within dry deep-freeze facilities.
Multi-Navigation
So critical to LGV performance, the latest-generation of LGVs designed for deep freeze – like those form Elettric80 – are equipped with multi-navigation based on laser guidance, supplemented with vision guidance. Both navigation methods are seamlessly combined which switches back and forth from laser to vision guidance without stopping the vehicle. This allows the LGV to move throughout a deep-freeze facility, where one system alone may not have access to the physical surroundings necessary to support that system.
Laser navigation is based on target triangulation to keep the vehicle on course. The vehicle is equipped with a rotating laser beacon, which scans 360 degrees around the vehicle for laser targets mounted on columns, walls and stationary machinery. The reflections from these targets are measured relative to angles from the vehicle, and triangulated to allow the vehicle to determine its position. This position is compared to a CAD-type map stored in the vehicle’s memory. The system uses positive-positioning feedback in real time, computing algorithms hundreds of times per second. The steering is adjusted accordingly to keep the LGV on track. It can then navigate to a desired target using the constantly updating position. Laser navigation can obtain tracking accuracy of about +/- .75 inch on these LGVs.
Vision navigation uses cameras or lidars onboard the LGV to detect the vehicle's surroundings and understand its position. Each vehicle has a CAD-type map of the system layout in its memory.
These LGVs are equipped with outboard laser bumper sensors for object detection. Covering the vehicle 360 degrees including upwards, the sensors are designed to cause the vehicles to adjust their speed, or stop if necessary, if an obstacle is detected in their path. Once the path is clear, the LGV will automatically continue its mission.
Real-Time, Integrated Controls and Logistics
The smooth functioning of LGVs is dependent on their controls system, which has the task of coordinating the orders received from the plants’ process system or warehouse management system, or ERP, then directing the work for the automated guided vehicles.
One of the most advanced LGV controls systems for automated deep freeze applications is Smart Integrated Logistics (SM.I.LE80®) from Eletcric80. The positional status of each LGV is continuously being updated through the controls system regarding such factors as whether it is loaded or unloaded, emergency stopped or soft stopped, operating in manual mode, and battery level. A simulation module simulates the LGVs in the system. An HMI graphical interface gives the operator a graphical overview of the LGV locations in the system and monitors each in real-time.
Operational flexibility is a key factor. Not just in its capability to direct and manage the fleet of LGVs, but also in its expandability. Any number of automated guided vehicles can be added to the network, at any time plant production or distribution needs require.
Latest LGV controls integrate seamlessly with production lines and warehouse functions. (Elettric80)
But the latest-generation of LGV control systems can do much more. For example, SM.I.LE80 ensures the integrated and automated management of systems and flows, communicating with production lines, palletizers and wrappers, as well as coordinating the movement of pallets in the warehouse, through to shipping. The entire logistics flow of the controlled-temperature environment can be centrally managed from an integrated-logistics software platform that ensures the efficient integration and optimization of all operations. Such a controls system also guarantees total product traceability and safety throughout the deep-freeze supply chain.
A WMS module within SM.I.LE80 can substitute for a traditional WMS. The WMS module contains the standard interface system that integrates with the factory's ERP. It enables the implementation of multi-site communication by providing a centralized ERP interface and transmitting information to different systems as needed. All system activities can be monitored in real time.
The WMS module also provides a statistics and reporting package for analyzing productivity, monitoring system KPIs and operator performance, and checking system exceptions, among other functions.
Another option within the SM.I.LE80 controls package is its Yard Management System (YMS) module, which oversees, manages and tracks trucks, trailers and containers in the yard of a production plant, warehouse or distribution center. This module encompasses: a) real-time information on the arrivals and locations of vehicles and containers, with associated parking times; b) real-time monitoring of order shipping and loading bays; and c) reports and dashboards on KPIs for processes and people, with statistical analysis of delays, workloads and yard parking times.
System Simulation
Today, 3D mapping in temperature-controlled environments permits extremely detailed LGV system simulations to be created that provide excellent system development guidelines. Variable conditions are factored into the simulation, such as human interaction on the floor where LGVs are in motion.
3D mapping simulation of LGVs in temperature-controlled environments. (Elettric80)
Fleet size is monitored by volume of product transported per move, and length of the route. The bigger the LGV system, the more important is the need for simulation. In a system larger than five or six vehicles, simulation would be highly recommended, as mathematics calculations alone cannot adequately profile vehicle-to-throughput ratios.
Flexibility, Modularity and Scalability
The most recent automation developments in forked laser-guided vehicles for pallet movement in deep-freeze environments enable warehouse operators and plant production supervisors to optimize for system flexibility, modularity and scalability.
Optimizing cold-storage LGVs for system flexibility. (Elettric80)
Designed to handle various pallet types – such as CHEP, EURO, Blockpallet and Stringer, with load requirements up to 3,400 pounds, these LGVs are able to accommodate single-deep and double-deep racking with a telescope fork. Using a satellite remote unit, lane depth can be considerably extended.
An increasing number of supply chain manufacturers, including food processors, bottlers and distributors, require 24-hour operation at maximum throughput in cold-storage facilities. Today's latest generation of LGVs have been designed to efficiently meet and exceed these requirements.
About Elettric80 S.P.A.
Founded in 1980 and headquartered in Viano, Italy, Elettric80 specializes in the development of automated logistics solutions for consumer goods manufacturers in the beverage, food and tissue sectors, and other diversified areas. Its automation solutions improve profitability and efficiency by streamlining product movement from receipt of raw materials through production, warehousing and shipping.
The content & opinions in this article are the author’s and do not necessarily represent the views of RoboticsTomorrow
Comments (0)
This post does not have any comments. Be the first to leave a comment below.
Featured Product
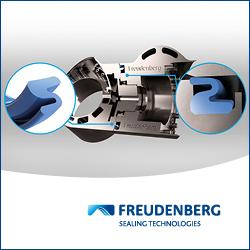