Can you be assured that each AMR in your fleet will position itself consistently to reliably pick up or deliver goods from your conveyor systems, exchange a pallet, or perform any number of automation tasks?
How to Choose a Mobile Robot
Article from | Omron Automation
You have decided to automate your operation’s material handling with autonomous mobile robots (AMRs). After identifying a few AMRs that have the capacity to carry a sufficient payload for the job, you will want to find some other factors that you can directly compare. If you are looking at datasheets side-by-side, repeatability and accuracy specifications stand out as a place to start. You will see numbers like +/- 10 mm, or +/- 25 mm—but what do these numbers really mean, and why do they matter? Do these numbers mean the same thing on the datasheets of different AMR manufacturers?
Can you be assured that each AMR in your fleet will position itself consistently to reliably pick up or deliver goods from your conveyor systems, exchange a pallet, or perform any number of automation tasks?
In the following sections, we will provide the background needed to properly consider repeatability and accuracy in your AMR selection process.
What’s the difference between “Repeatability” and “Accuracy”?
Repeatability is the consistency in which an AMR will return to the same desired location in your facility. Accuracy is a measure of how closely the AMR will align itself with some real-world geometry of interest, for instance, the output of a conveyor line.
The distinction between repeatability and accuracy is very important for many fully automated applications. Repeatability is what makes the difference between a hands-off operation and one that requires frequent manual intervention.
AMRs typically use data from multiple sensor types to compile a digital ‘map’ of the space they are expected to navigate. As the AMR travels through a facility, it uses those same sensors to update its position on the map. This process is called ‘localization.’ Common forms of localization compare live sensor data to maps made from scanning lasers, cameras, code readers, or magnetic sensors.
Once you have created a map, you will teach goal positions for your AMR. For example, you might manually align your AMR with the output of a conveyor line and add that goal to your map. Each time the AMR is instructed to return to this goal it will be subject to some localization error. There will always be some measurable deviation from the ideal position due to sensor noise, a dynamic environment, mechanical tolerances, etc. For your operation to be reliable, it is important that this deviation is within your allowable constraints. In this example, it is important that the AMR is aligned well enough with the output conveyor to receive the box, tote, or pallet from the conveyor without jamming or dropping the goods. If you mark the point on the floor that the AMR positions itself each time it returns to the taught goal for a number of times, you will find a grouping of points. The tightness of this grouping is your AMR’s repeatability. Is the center of that grouping at the exact place where you initially taught the goal? If so, your AMR is both repeatable and accurate at this goal. If your grouping is tight enough for your needs, but the AMR is not aligning well enough with your conveyor, then your AMR may be considered repeatable, but not accurate enough at this location.
Resolving this may be as simple as shifting the taught goal location so that the center of the recorded grouping is in a more accurate location. In practice, measuring and editing locations may quickly become untenable when adding more goals, frequently rearranging your production lines, or most importantly, when adding additional AMRs to your fleet.
If I have a large fleet of AMRs, will they all arrive at each goal with this repeatability?
Most fleet controllers provide the convenience of sharing a single facility map with an entire fleet of AMRs. This feature comes with the subtle but important consideration that the AMR that made the map will be the most accurate AMR in the fleet. Differences between that AMR and others in the fleet can be attributed to several factors that are difficult to eliminate, including:
-
AMR assembly tolerances for sensors positions and wheel locations
-
Sensor calibration differences
-
Uneven wheel wear
-
Gearbox backlash, etc.
It’s also important to consider sources of error that aren’t represented in the AMR manufacturer’s original specifications. For example, if a system integrator builds a conveyor system on each AMR, then the assembly tolerance of the conveyor and its mounting will affect the overall fleet accuracy.
A successful demonstration of a single AMR is a good start, but it’s not necessarily a guarantee that a larger fleet of AMRs will perform as reliably unless the manufacturer or system provider can also supply you with a value for fleetwide performance.
Conducting a fleetwide repeatability test with multiple AMRs will yield a more trustworthy spec. However, it is not practical to gather data from dozens of AMRs. Start testing with four AMRs to confidently asses the repeatability of a larger fleet. We recommend adding more AMRs to the test sample if any unit in the test fleet stands apart as an outlier without showing any recognizable physical defects or sensing problems.
How do AMRs achieve alignment where is really matters?
Let’s return to the conveyor example. If a fleet of AMRs will receive goods from the same conveyor, it is critical that they all align themselves accurately enough for a safe and reliable transfer. If an AMR is too far to the left or right, or if it leaves too large of a gap between the AMR and the conveyor, there’s a risk that the transferred goods will be jammed. Rotational alignment between the AMR and the conveyor is often the most important dimension to consider. A few degrees of misalignment can mean the difference between a successful transfer and delays in your operation.
Some AMRs improve their accuracy at these critical locations with additional sensing that can be used with tape or painted lines, retro-reflectors, bar-codes, or other infrastructure. For instant, you can place a magnetic line on the floor, and installing sensors on each AMR, a fleet will be enabled to stop at a conveyor station within +/- 10mm and +/-0.5 degrees.
Another approach to improving local accuracy is to use the AMRs existing sensors to detect known features near the location-of-interest. These features provide a landmark relative to which the AMR can position itself. Some automation solution providers have developed a Cell Alignment Positioning System, or CAPS for short. CAPS enables the AMR to use its existing scanning lasers to identify a specific geometry and position itself at destinations where fleetwide repeatability and alignment are crucial.
Tips for considering key factors that affect repeatability
Environmental density
In general, an AMR will perform better in places where it has lots of features to localize than it will in very spare environments.
Noisy environments
The conditions of a repeatability test should be modeled after those of the intended environment. AMRs rely on detecting environmental features like walls and other permanent fixtures. AMR localization will be most accurate immediately after a map is made, before any mapped features have shifted or become obscured. In practice, a productive facility will be changing constantly; pallets full of goods may obscure mapped walls, or people and other vehicles may prevent the AMRs sensors from recognizing as many landmark features.
Direction of approach
You may find your fleet’s positioning accuracy to be better when AMRs always approach a destination from the same direction. This may be caused by differences in environmental factors when approaching from different directions, such as the number of visible features, or the amount that those features are obscured by unmapped obstacles. This may also be caused by AMR-specific factors that lead to a tendency to overshoot or undershoot.
Floor conditions
AMR repeatability may be affected by a floor’s flatness, levelness, imperfections, and coefficient of friction. It’s important to record the floor conditions when conducting your own tests. Keep the flooring condition of the intended operating environment in mind if your testing will be done in a different space.
Speed/Acceleration
Does meeting the specified accuracy or repeatability spec require using a speed or acceleration different than the AMRs default? If so, this should be specified, especially if the difference is significant enough to impact overall cycle-times or AMR availability.
Conclusion
The use of AMRs - once a technical marvel - is starting to become mainstream in factories and warehouses around the world, helping companies sustain and grow without incurring unnecessary cost. We hope this White Paper has helped you understand the importance of fleetwide repeatability and that it will help you mobilize a fleet of AMRs that will quickly and truly benefit your operations.
The content & opinions in this article are the author’s and do not necessarily represent the views of RoboticsTomorrow
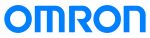
Omron Automation
Omron is an industrial automation partner that creates, sells and services fully integrated automation solutions that include robotics, sensing, motion, logic, safety, and more for manufacturers in the automotive, semiconductor, food and beverage packaging and other industries. Established in 1933, Omron helps businesses solve problems with creativity worldwide, with more than 37,000 employees serving over 110 countries. Adept Technologies is now a valued part of the Omron family.
Other Articles
Advancing Machine Design with the Power of Collaboration and AI
Preparing Your Facility for Mobile Robots: Key Considerations for Seamless Integration
Transforming Manufacturing Processes with AMRs: Boosting Efficiency and Adaptability
More about Omron Automation
Comments (0)
This post does not have any comments. Be the first to leave a comment below.
Featured Product
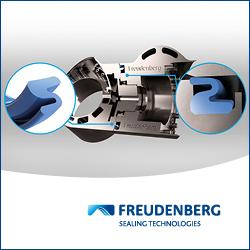